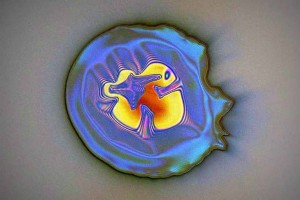
Jose Pozo, EPIC’s CTO, had the opportunity to talk to Andrius Melninkaitis, CEO of Lidaris, a Lithuanian-based specialist in optics characterization services focusing mainly on Laser-Induced Damage Threshold (LIDT) testing.
Early research
In 1998, Andrius began his physics studies at Vilnius University in Lithuania, which six years later led him to Ph.D. studies on the topic of Laser-Induced Damage Physics. At that time, Andrius saw the world of lasers as something mysterious, prospective, and attractive. During his master studies, he has spent one year in Germany in 2003 as an Erasmus exchange student at the University of Hannover. Simultaneously he also did his nearby practicum in Laser Zentrum Hannover (LZH) at the group of Optics Characterization. Later this connection also developed into long-lasting fruitful cooperation with Laser Research Center of Vilnius University. During Hannover time he got involved in research of laser-induced damage for the first time. After his return to Lithuania, he continued to deepen his knowledge in Vilnius, became an informal leader of a laser damage subdivision at Vilnius University.
A bit earlier in the year 2000, scientists of Vilnius University also initiated a related NATO Science for Peace project that was aiming to establish a laboratory for testing optics in response to the need of local companies. Andrius was keen to get involved in the project and quickly came to recognize the importance of testing activities:
First of all, a gap of optics characterization became apparent among local companies that were designing and manufacturing optics: usually, they had no clear feedback on the quality and best parameters of their technologies. What they needed, was appropriate benchmarking of their products as well as consulting on how to make better optics.
Secondly, companies trading (buying and selling) optics had only a little or no information on the laser damage performance from their goods (suppliers from various suppliers), but their customers became more and more demanding in terms of what they buy.
And thirdly, due to lack of expertise in the laser damage phenomena, communication errors between companies selling and buying were non-exceptional. As a result, people were not always satisfied with the “of shelf” choice as longevity and reliability of the sold products were often not sufficient for the end-use application. Production was not always reproducible from batch to batch that sometimes resulted in endless disputes.
As he said: “It was important to understand what compromises are allowed when ordering optics. It is not always trivial to assess what is needed for a particular system. After launching a testing business, we started to communicate with all the groups constituting a value chain and we got a lot of very interesting inputs. We learned that meaning of testing is very different for each group within the value chain.”.
Starting from scratch, Andrius and his team began an interesting and fruitful journey, trying to learn as much as possible and having fun in an open, friendly laser damage research community.
Altechna Co. Ltd.
During the Ph.D. studies, Andrius has had a side job at Altechna Co. Ltd. a Lithuania-based custom laser optics company with worldwide customers. He was mainly involved in various R&D activities related to high power laser applications. At that time, he was also curious to understand how high-tech companies functioned. He worked on various micromachining activities as they were quite related to laser damage topic, however, his main focus was still on his Ph.D. studies at Vilnius University.
Lidaris Ltd
After his Ph.D. thesis defense in 2009, he became an independent researcher at Vilnius University, intending to go deeper into the physics of laser damage. He supervised diploma works of many talented physics students that were working on the topic of thin-film coatings and laser damage. All his research was directed in finding out two answers to the fundamental questions, namely - how to predict laser damage? and how to avoid it?
Left to right: Dr. Andrius Melninkaitis (CEO at Lidaris), Dr. Gintare Bataviciute (Project manager at Lidaris), and Carlos Lee (Director General at EPIC)
By 2012, it had become apparent that while the projects related to laser damage have been successful in meeting the needs of local companies, his work would not be sustainable if they only would rely on national funding form local industry and national science agencies. The whole sector was simply not big enough. At the same time, they also had started to receive first interesting inquiries from institutions abroad within the network of LaserLab-Europe and so they decided the time was right to open up the new project, namely establish a spin-off company, LIDARIS Ltd.
For Andrius, it was the next logical step: “We were already working as a very young and enthusiastic scientific team well trained in the field laser damage, so the core of the company was de facto there”.
The idea was to open up for the rest of the world and provide advanced Laser-Induced Damage Threshold (LIDT) testing solutions to meet the increasing demand from manufacturers, integrators, and resellers of high-power lasers and optical components and systems worldwide.
Over the past 8 years, Lidaris has become a world-renowned laser damage testing laboratory that is also providing support for the optimization of the manufacturing of optical elements towards high-power laser applications. During this period, the company’s scientists were closely cooperating with Vilnius University, as a result, joint research was recognized and awarded by the SPIE Laser Damage community. Currently, Lidaris is proud to serve more than 90 customers worldwide, including the European Space Agency for whom they have contributed a way for qualification of optics’ longevity required by space programs. This year Lidaris will be a sponsor of a double-blind laser damage competition contest that will be organized together with Lawrence Livermore National Lab. (USA). It will determine the state of the art of current nanosecond laser damage resistance of 532-nm multilayer mirrors worldwide. The results will be shared at the SPIE Laser Damage 2020 conference in Rochester (USA).
Business models
Lidaris operates three different business models, namely: ISO standard based “black box” testing, project-based R&D activities as well as dedicated services:
Standard testing: Lidaris provides a service of ISO 21254 based standard LIDT testing:
1-on-1 for determining “non-fatigue” LIDT, well suited for quick testing and optimization of various manufacturing technologies;
S-on-1 LIDT test for characterizing multi-pulse laser-induced damage threshold and so-called fatigue effect;
Laser Damage Certification pass-fail testing at user-specified fluence e.g., qualifying of purchased optics before end-use in critical applications.
R&D projects: To answer a specific question related to laser damage related problems (optimize manufacturing technology, overcome bottleneck or establish customer unique testing capability) they also can organize a dedicated team of experts to provide non-standard LIDT related solution. In this case, Lidaris can support the process with an expert’s guidance. In those cases, various non-standardized approaches to LIDT research can be used. Customer-specific objects can be investigated with non-standard testing ways. For example, the R-on-1 LIDT test can be used to provide information about the LIDT of the surface limited samples, e.g., fiber tip or small crystal; the raster scan technique can be used to detect rare defects, which could be missed by only applying the standard S-on-1 test. In some specific cases, optics can be tested for an extended period.
Dedicated testing: For customers requiring high throughput non-standard laser damage testing Lidaris offers dedicated testing services. For most demanding customers Lidaris helps to establish a customer dedicated testing capability that is operated at Lidaris premises for only one customer. In this case, Lidaris works as an outsourced virtual department of the customer organization.
Training and education: For entrusted customers, LIDARIS can also provide on-site training to educate customer’s sales teams or engineers in the field of laser damage. In this way, Lidaris helps to recognize where the potential problems and opportunities lie and how to avoid miscommunication when addressing the LIDT topic.
Issues and features of LIDT testing
Testing protocols: Standard-based testing procedures are conducted following the guidelines of the latest existing international ISO standards 21254-1-2 and-3. As Andrius explains, the reason for the existence of so many different test protocols is related to the fact, that each set of optics is unique. Different testing protocols could be seen as a toolbox of specific instruments to address a specific problem. For example, the protocol for testing a fiber tip, where only a few micrometers of the area are available is different from the protocol for testing meter-sized optics. In addition to completely different properties, customers also have very different needs: some want to know if their optics are good enough for their applications, and another might want to know if their satellite is going to work after two years of operation.
Quality and certification: Most of the end-users of the optics, i.e., laser system developers, require a certificate from supplier confirming that the purchased component will perform reliably. While the LIDARIS Laser Damage Certification Test can confirm the quality of optics in large quantities, the certificate is made only one particular batch. Not every company is committed to the same values or cultures. As Andrius confirms: “It is sometimes interesting to watch what’s going on in some overseas markets: newcomer companies often order optics from well-recognized suppliers and then is sending this good optic to us for testing to obtain a good looking certificate. As they get a certificate for good optic, they show it to their customers, claiming that this is the quality they will provide. But as soon as higher quantities of goods are ordered, they supply a different product that has no relation to the one-time certificate. We can help to resolve similar issues by cross-checking every new batch from different suppliers. In this case, abuse or potential error in production can be cached in the early phase so that a lot of time and money can be saved for every party in the future.”.
However, in the context of quality, for Andrius, the saying “European optics are better, but Chinese optics are cheaper” is a myth. First, you can find top-level optics and very bad optics from the same supplier, e.g., because they're using different devices for different coatings. Secondly, because the supply chain is now global, you never know where the optics come from: suppliers selling optics in Europe may be buying them from China or from anywhere, or vice-versa. There some trends, but also there are good and bad optics everywhere.”.
Damage in transit: As customers have to send their optics samples to Lidaris, there are sometimes problems with awareness on packing and handling. Cross-contamination is often underestimated. As a result, there are many cases when optics arrive in a contaminated state and needs extra cleaning. Not all optics can be cleaned well thus it is worthy to invest some time in avoiding contamination so that LIDT numbers are not screened fingerprints. The same applies to the logistics of high power laser components, which is often underestimated even in large organizations.
The Future
With an increasing number of laser suppliers coming onto the global market, the future for Lidaris looks bright. The strength of the company is not only that they test customers’ optics, but they also help the customer to understand the limits of those optics and to remove any obstacles so they can realize the potential of their technology.
Although their market is global, for Andrius, one of the main challenges for the future is to make companies in the sector less shy and more aware of the advantages of using Lidaris’s services. To this end, the company is considering a move to becoming a real international company and not just operating from Lithuania. Also, LIDARIS is considering a business model innovation that could better satisfy the market’s needs.
If you could start all over again, what would you do differently?
“Although it was fun, the business development took a lot of energy because we’ve always tried to do everything the best we can. It’s taken up a lot of time and personal involvement and if I started again, I’d try to establish more clear boundaries between family and work-life; spend more time with a family”.
“Another thing I’d do differently is to attract more people with business and organizational expertise earlier. When we started, we had almost zero understanding of the business operations and development and little knowledge on how to standardize things - everybody was doing everything: there was some randomness at the beginning and it took some time to establish a structure within the company”.
Written by Jose Pozo, Director of Technology and Innovation at EPIC (European Photonics Industry Consortium).