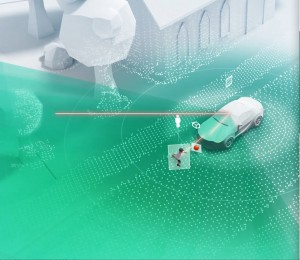
In the future, technology will take over the steering wheel in autonomous vehicles; humans will only be passengers. But in order to lean back and relax, you need high safety standards. The car must independently recognize obstacles and dangers and brake in good time in an emergency. A new microscanner mirror from the Fraunhofer Institute for Photonic Microsystems IPMS scans the environment three-dimensionally and records ranges of over 200 meters. Installed in a lidar system, it replaces the human eye and makes a decisive contribution to safe, autonomous driving.
A research team at Fraunhofer IPMS in Dresden has now developed a new type of microscanner mirror, an important component for lidar systems that enables digital vision in three dimensions. By steering the scanning laser, the component contributes to the three-dimensional measurement of the environment. The company AEye already uses the microscanner mirrors: The specialist for light detection and distance measurement systems for autonomous vehicles uses the microscanner mirrors in its lidar sensor 4Sight. "With our technology platform we can meet the respective design needs for the development of microscanner mirrors for lidar. Lidar systems can capture the environment in three dimensions and are therefore able to detect pedestrians, cyclists or other vehicles. Our MEMS mirror distributes laser beams in two dimensions and bundles the light in the currently measured position. With the travel time of the reflected light, the distance to the object is measured as a third dimension, ”explains Dr. Jan Grahmann, scientist at Fraunhofer IPMS.
In detail, the following process takes place: The light that is sent by a laser diode or laser source first hits the microscanner mirror, which is located on the transmitter unit of the lidar system. The mirror scans the scenery two-dimensionally. The third dimension is captured by a lidar sensor on the receiving side using the light reflected from the object. The following applies: The more light hits the sensor, the more precisely the distance can be determined - a task that is performed by an evaluation algorithm. The distance information for each scanned position in the scenery results in a 3D point cloud that shows the lidar's field of view.
Fatigue-free, robust, shock and temperature stable
The MEMS scanner is made of single crystal silicon. The advantage of the material: It is fatigue-free and robust and is characterized by high shock and temperature resistance. There is a reflective coating on the silicon that intensifies the reflection of the light. Thanks to a position detection integrated in the chip, it can be determined at any time where the mirror is directing the laser light and which position is being measured in the image. This in turn enables corrections to be made to the operating point. In the vehicle, the lidar sensor is usually located behind the rear-view mirror and scans the scene directly through the windshield. In addition to the normal perception by the passenger or driver's eyes, the 3D measurement in the infrared range can be implemented in this way.
“Our MEMS mirrors are typically up to around five millimeters in size. Larger mirrors are possible in special cases, but lose the advantages of MEMS with increasing size. In addition to the microscanner mirrors, we also offer the required packaging and drive electronics. All components can be customized to ensure optimal integration into the different lidar systems. For example, we also develop MEMS scanners for head-mounted displays or industrial robots, ”says the researcher.
The microscanner mirrors from Fraunhofer IPMS work, for example, with the wavelengths of 905 to 1550 nanometers typical for lidar and have a significant influence on the ranges due to their opening width. Built into the smart lidar sensor from AEYE, long ranges of more than 200 meters are possible. The company's first driving tests with the MEMS scanners from Fraunhofer IPMS used in the lidar system have been successfully completed.
"Currently, lidar can be seen as a driver assistance system that offers more comfort and safety. Autonomous driving is divided into five stages, in which the driver has to intervene in the driving process in different ways. It will be some time before fully autonomous driving becomes a reality, but with our technology we can advance the topic, ”says Dr. Grahmann. In the next step, the microscanner mirrors are to be produced in large numbers and transferred to large-scale production.