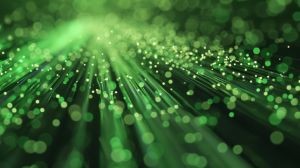
For challenging machine vision applications, the CoaXPress ("CXP") interface is a clear winner. This is thanks to its data transmission rates of up to 12.5 Gbps per link which, when four links are aggregated, deliver a staggering 50 Gbps. Besides machine vision, CXP has proven to be a smart upgrade for legacy coax-based analog systems, such as those found in military and aerospace systems or Intelligent Traffic Systems (ITS), because CXP lets the already installed 75-ohm coaxial cable be re-purposed as the transmission medium.
Another use case for CXP has come to light – pardon the pun -- and it could be a blockbuster: Running the unaltered CXP protocol across long-distance fiber optic cables. Before we move on, let's examine circumstances in which a combo of fiber and CXP adds value.
- Pipelines: Checking the inside of pipelines for cracks, corrosion, or leaks, especially in remote or “hazardous” rated locations. Explosive dust, fumes, or liquids may be present in areas rated as being "hazardous” by the NEC or IEC.
- Infrastructure: Monitoring stress, vibrations, and other damage to bridges, large structures, and wind turbine blades.
- Remote sites: Inspecting difficult-to-reach places, such as inside processing tanks, machinery, or aircraft parts. This would also be valuable in destructive testing.
- Surveillance/Defense: Monitor, track, and interact with high-value surveillance targets—like military bases—from a distance. Also utilized to support intelligence or reconnaissance operations and to secure borders.
- Industrial Automation: Observe assembly lines or very large factories with numerous cameras installed.
- Underground: Examine the state of sewer lines, cables, or tunnels.
- Aerospace: Scientific observation of all aspects of a rocket launch.
Fiber is the ideal complement to CoaXPress owing to its high bandwidth, immunity to EMI, safety, durability, and compact dimensions. With single-mode fiber, targets up to 120 kilometers from a host can be monitored with little latency and no signal deterioration from attenuation. Plus, fiber is more resistant against tampering than copper.
The Old Way: GigE Vision Over Fiber
GigE Vision over fiber has been the "go to" option for long-distance imaging. GigE Vision is a camera interface standard that uses Gigabit Ethernet for transmitting high-speed video and control data. Because of the protocol's independence from the physical media, GigE Vision cameras can use Ethernet hardware over fiber.
A basic system is comprised of a fiber cable run between a GigE Vision camera and two copper-to-fiber media converters. The first converter near the camera converts its Ethernet signal to fiber optics, while the second converter at the host PC converts that signal back to copper. Alternatively, a high-end GigE Vision camera supporting fiber optic connectivity with an SFP port or an adapter might be connected to an industrial Gigabit Ethernet switch featuring SFP or SFP+ fiber optic ports. GigE Vision relies on standard Ethernet protocols, so the fiber connection should be transparent to the application as long as the physical layer is compatible.
Sounds good, right? Here’s the catch: While GigE Vision can take advantage of Ethernet networks' 100 Gbps capacity, the standard does not function at that speed by default. Most GigE Vision cameras are really operating at 1 Gbps, which, after overhead, corresponds to a maximum data rate of roughly 100–125 MB/s. Bottlenecks occur when cameras surpass the bandwidth.
How about 10GigE Vision? There are problems here, too. Over time, it has become evident that CPUs are unable to manage 10 Gbps traffic, leading to missed frames and unacceptable levels of latency. In contrast to CXP or Camera Link systems equipped with frame grabbers, GigE Vision uses the CPU of the host computer to parse Ethernet packets and control data streams. Although 10G frame grabbers with offloading capabilities or smart NICs can lower CPU usage, this method negates GigE Vision's main benefit over CXP, which is the elimination of a frame grabber. To support 10GigE Vision, older cable infrastructures must also be upgraded with CAT6 or CAT6a, which raises system prices even further.
Other drawbacks of the protocol include its high-power consumption which leads to overheating, its frame latency, its inability to send real-time triggers, and that multiple cameras cannot be connected to the same PC. Long-distance system applications only make these issues worse.
For simple applications, GigE Vision remains a flexible, reasonably priced option. However, its shortcomings make it less suitable over long distances, where its initially low cost of entry can quickly skyrocket.
CXP Goes the Distance
The Japan Industrial Imaging Association (JIIA) standards committee published CoaXPress 2.0 and 2.1 in 2021, and the Global Coordination of Machine Vision Standards (G3) quickly adopted them. The use of Micro-BNC connectors, the doubling of the uplink speed for triggering at over 500kHz, the support for additional speeds (CXP-10 and CXP-12), and compliance with GenICam and GenDC were the main improvements.
Overlooked amid this news was the addition of CoaXPress over Fiber (CoF) to the version 2.1 standard. CoF is transformative because it permits fiber optic links to function with the CXP protocol without alterations— the data protocol is still CoaXPress. To ensure interoperability with current fiber networks, CXP data is encoded into the fiber using normal Ethernet signaling, such as 10GBASE-R for 10 Gbps.
Until very recently, there were only two methods to transmit CXP over fiber. Both work but introduce additional hardware, costs, space requirements, and potential failure points to the system.
-
Option one is to convert the camera’s CXP output to fiber using a dedicated set of converter boxes with a long run of fiber cable in between. The signal is transformed back into copper at the PC end and connected to a CXP frame grabber. Although this setup is feasible, it might be too expensive.
PHORTE CoaXPress Fiber Extender 4 Channel (quad) that supports all high-speed bit rates, up to 6.25Gb/s and extends up to 80 kilometers -
The second option is to have a camera manufacturer redesign its non-CoF CXP camera with a fiber interface. The problem is that a basic CXP camera, particularly the lower-cost single or multiple link CXP units that have a compact footprint, would need to be increased in size and power to integrate a fiber output. Practically speaking, the camera manufacturer's return on investment will probably be too low to move forward.
JAI GOX-8105C-CXP is a small industrial area scan camera with a single CoaXPress 6.25 Gbps link
Option 3: BitFlow and Advantech
BitFlow QFi connects directly to a camera via normal CXP on coax and can also power the camera. It uses CoaXPress over Fiber (CoF) on the frame grabber side. CoF can run many kilometers on low cost fiber cables. The fiber then plugs directly in to the BitFlow Claxon fiber frame grabber.
A third option has emerged to address long-distance machine vision, thanks to Advantech and BitFlow. It centers on the new BitFlow QFi CoaXPress 1.1/2.0 compliant module that is specifically designed to work with standard single-link CXP cameras featuring Micro-BNC (HD-BNC) connectors. For imaging professionals, the QFi is a true game-changer the reduces long distance link complexity and speeds up commissioning.
Here’s how it works: a coaxial cable runs between the QFi and the CXP camera, connected directly to the CXP camera’s Micro-BNC output and into the BitFlow QFi input. To increase deployment flexibility, cables can reach a maximum length of forty meters. Once connected, the BitFlow QFi provides 13W of power to the camera, not unlike a standard CXP installation relying upon PoCxP. Additionally, the QFi offers full uplink channel capability for firmware upgrades, triggering, and camera configuration and control.
Next, the fiber output port of the QFi is linked to an off-the-shelf single mode fiber optic cable with a single QSFP+ transceiver on the input side and as many as four transceivers on the other. The output end of the fiber cable of that fiber cable links to a BitFlow Claxon FXP4 CXP-12 frame grabber embedded inside an Advantech industrial PC (IPC). No programming is required.
In five minutes or less of setup time, data from the camera will begin continuously streaming at a steady 10 Gbps at distances of up to 128 kilometers (75 miles) without experiencing signal degradation. Data is received from the QFi in CXP standard format.
Require more cameras at the site? BitFlow has the answer. Output of up to four QFi boxes can be connected to a single quad-link frame grabber to support multi-camera setups. Also, several QFi modules can be used for multi-link cameras.
The Advantech/BitFlow QFi solution eliminates multiple conversion steps, streamlining the process and opening new opportunities for system integrators. And now Advantech and BitFlow have taken an additional step to significantly reduce installation time and configuration inconsistencies by offering Advantech IPCs with a fully configured Claxon FXP4 frame grabber as a single unit.