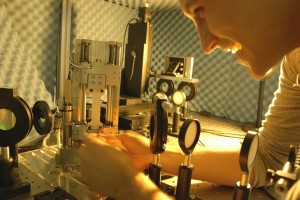
At Heriot-Watt University in the UK, a team at the Institute of Photonics and Quantum Sciences is focusing on stress analysis in ceramics and engineering plastics. They are particularly interested in ceramic thermal barrier coatings used on airplane engine turbine blades or power generating turbines. Typically, the air around these blades is hotter than the melting point of the blades themselves, therefore, they must be coated with a ceramic thermal barrier coating. These coatings, which have been used since the 1970s, enable the turbines to withstand higher temperatures in the engine. The trend today, according to Dr Peter Schemmel, a postdoctoral researcher in Applied Photonics at Heriot-Watt University, is to run engines at higher temperatures because the hotter you run them, the more efficient the engine is and more power is produced.
To improve the safety of airplanes and reduce maintenance costs, the team is studying ways to increase the useable lifetime of these coatings
The problem, as Schemmel pointed out, is that coatings don’t have a definite lifetime Coated turbine blades must survive hot temperatures, high pressures, foreign object debris impacts and CMAS (calcium-magnesium-alumino- silicate) accumulation. Eventually the environment causes too much degradation and the blades must be changed during the subsequent engine service. But to avoid catastrophe, maintenance is done on a recommended schedule, which may be far less than the actual longevity of the coatings and blades.
To improve the safety of airplanes and reduce maintenance costs, the team is studying ways to increase the useable lifetime of these coatings by understanding the stresses built up in the coatings during manufacture and over time in service.
Finding the stress optic coefficient
The researchers are using a 2 kN tensile stage from Deben to find the stress optic coefficient of a material. The stage helps measure the birefringence while a known stress is applied to the sample. Deben is a UK precision engineering company specializing in the field of in-situ tensile testing, motion control and specimen cooling for microscopy applications.
The team is using a quantity known as the “stress optic coefficient” to convert measured sample birefringence into stress distributions. In a paper published in Optics Express, they reported on the first measurement of the direct stress optic coefficient for yttria-partially stabilized zirconia (YTZP) ceramic, using illumination between 260 and 380 GHz with applied stresses up to 27 MPa. YTZP exhibited a linear change in refractive index as a function of stress across the entire applied stress domain.
A direct stress optic coefficient was also measured for polytetrafluoroethylene (PTFE). PTFE showed viscoelastic behavior at stress values above 4.5 MPa. These results open the way for quantitative sub-surface stress measurements in structural ceramics and ceramic coating systems at GHz and THz frequencies. What they found was that each material has a different coefficient, which can depend on several factors. Some things that can alter the stress optic coefficient of a material include the frequency of the radiation used in the test, the manufacturing methods, material density and atomic structure. This list is not exhaustive. Part of the research tries to understand how the stress optic coefficient of a material can change.
One of the advantages of using Deben’s tensile stage is that constant loads can be applied to the sample over the course of each birefringence measurement.
According to Dr. Schemmel, to find the stress optic coefficient of a material, “we must measure the birefringence whilst a known stress is applied to the sample.”
One of the advantages of using Deben’s tensile stage is that constant loads can be applied to the sample over the course of each birefringence measurement. “Such measurements take around ten minutes. If the stress on the sample changes during this time, the measurement is invalid. Without the Deben tensile stage, we would not be able to accurately calibrate our materials.”
The benefits of the stage are fourfold. Dr Schemmel continues: “Firstly, it is small. We required a small stage to sit on our optical bench, inside an anechoic chamber. Secondly, Deben was able to machine a specifically sized window in the back of our tensile stage so that we could pass our GHz - THz beam through the sample under test. Thirdly, and most importantly, the Deben system allows us to control the applied load with great finesse. We are able to maintain a constant load on each sample during the birefringence measurement period, which is critical to achieve accurate results. Finally, the system is extremely easy to operate. It is really a “plug-and-play-system,” which allows us to be more productive.”
The small testing chamber
The overall goal is to create an instrument capable of measuring component lifetimes after manufacture but before entry into service. By achieving this, Schemmel pointed out that maintenance costs will be reduced, but airplanes will also be safer and the researchers will gain knowledge of how coatings work and how components changed with age. The team is currently conducting mock trials in collaboration with Cranfield University and Rolls Royce by imaging samples that have been aged in furnaces, which represent flying conditions. Schemmel said that once they’ve proven that they can make these measurements, they can construct the test boxes and move toward commercialization.
Written by Anne Fischer, Managing Editor, Novus Light Technologies Today