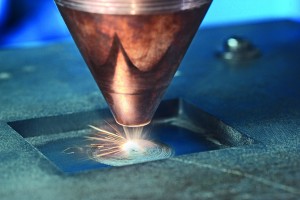
Damascus steel is a material of almost mythical fame, used to forge legendary swords such as Excalibur and Mimung. The Fraunhofer Institute for Laser Technology ILT in Aachen and the Max-Planck-Institute for Iron Research (MPIE) in Düsseldorf have been investigating a 3D printing method that could be used to produce a ferrous composite material of balanced hardness and toughness – all without the need for forging skills or furnaces.
Created by folding and forging steel in layers, Damascus steel owes its name to the city of Damascus, once home to numerous workshops that forged weapons from steel. Experts can instantly identify this steel thanks to its light and dark layers, which make it both tough and hard.
Steel with Damascus properties
But might a laser be equally adept at building a comparable composite material layer by layer without requiring forging skills or furnaces? This was the question posed by process engineers at Fraunhofer ILT und material developers at MPIE, who have spent years working together on strategic projects in both fundamental and applied research. “We opted for a precipitation hardening iron-based alloy which, with a different composition, is also known as maraging steel,” says Dr. Andreas Weisheit, manager of the Material Development for Additive Manufacturing group at Fraunhofer ILT. “It reacts to relatively short temperature spikes by forming precipitates that increase strength and hardness. We can make targeted use of this effect when building a product layer by layer.”
Laser material deposition for metal composites
These kinds of composite materials generally consist of thin layers. The microstructure of each layer can be modified by controlling the process temperature in a targeted manner, a technique known as intrinsic heat treatment. To do this, the researchers from Aachen and Düsseldorf applied the method of laser material deposition (LMD) developed at Fraunhofer ILT. Just like all additive manufacturing processes, LMD builds parts in layers. That made it a good option for manufacturing composite materials consisting of a range of thin layers.
No hardening furnace required
The LMD process was chosen because it can be controlled very accurately. This enabled the scientists to adjust the temperature with a great deal of precision, allowing them to perform heat treatment during the 3D printing process itself. In conventional manufacturing, materials of this kind end up in a furnace for the final heat treatment process (in order to adjust the final materials mechanical properties). The material normally remains in the furnace for several hours at a high temperature to allow it to gradually harden. “We don’t have that kind of time available!” says Markus Benjamin Wilms, a research fellow at Fraunhofer ILT. “With our method, this hardening process actually occurs during the 3D printing step. That eliminates the need for most, or even all, of subsequent heat treatment processes.” The team does this by harnessing cyclic heating, with deposited layers heated by the deposition of subsequent layers. Heat treatment in a furnace is still required in cases where the formation of precipitates in alloys proceeds too slowly.
LMD not only suitable for steel composites
The limits of the LMD method therefore lie in the selected material. “You obviously need to use a material that reacts to these short time-temperature cycles – it’s not something you can just apply to any hardenable material,” says Weisheit. “But LMD is not just limited to iron-based composites. Experiments have shown that it also works with aluminum alloys.” In other words, the principle of intrinsic heat treatment using laser material deposition can also be applied to other alloy systems.
Need for collaboration on material development
So what conditions must a composite material meet to make it suitable for laser material deposition? There are two key requirements, says Weisheit: it needs to be a printable alloy, and precipitation needs to occur relatively quickly. “This is a job for material developers,” says Wilms. “In other laser-based 3D printing methods, the user would have to adjust the alloy composition because the temperature control process works a bit differently.”
Deliberate pauses for cooling
This particular project used an iron-nickel-titanium model alloy developed at the Max-Planck-Institute. During 3D printing of the iron-nickel-titanium structures, the researchers briefly paused the process after the deposition of each new layer to allow the metal to cool to below 195 degrees Celsius. “We need the austenite-to-martensite transformation,” says Weisheit. “And we can only get the precipitates to form by applying small, carefully dosed temperature peaks.”
From cubes to pyramids
Fraunhofer ILT confirms the method already works very well for LMD, but the principle of building things up layer by layer has so far only been applied to certain simple geometric structures such as cubes. “By continuing to improve the method, we’ll be able to build more complex structures,” says Wilms. “We’ve already incorporated complex forms into the material during printing, such as triangular and pyramid-shaped hardness profiles.”
Two methods under consideration
But LMD is not the only option. The scientists also highlight the potential of using another method developed at Fraunhofer ILT known as laser powder bed fusion (LPBF), sometimes referred to as SLM. Preliminary studies at Fraunhofer ILT have shown that LPBF is also suitable for 3D printing of composite materials. “If my goal is to build very complex parts with very high-resolution details, then I would obviously always go for LPBF,” says Weisheit. “I would also lean toward LPBF if I’m looking for a very precise hardness profile in my 3D printing. But otherwise I would opt for laser material deposition.”
Hunt for industry partners
Another benefit of LMD is its suitability for hybrid processes, says Weisheit. For example, it offers complete freedom for building composite structures on free-form surfaces. “It’s not like these two approaches are competing with each other,” says Weisheit. “It’s about choosing the one you prefer for each particular use case. I’m looking forward to working with industry partners to bring new practical applications forward.”
The Aachen-based team has already come up with new ideas to take the method to the next level: Weisheit says it might be possible to control the process so skillfully that a third state could be achieved – for example a partially hardened area in addition to the fully hardened and unhardened layers. “So far we’ve stuck to working with the pause times. But the temperature profile could also be controlled using other process parameters such as laser output power.”
For more scientific details, please see the article “High-strength Damascus steel by additive manufacturing” which was co-authored by Weisheit and Wilms and published in the journal Nature on June 24, 2020.
Written by Nikolaus Fecht; commissioned by Fraunhofer ILT