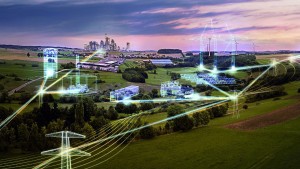
Automotive and turbine manufacturers, steel and chemical companies all have one thing in common: They see their future in hydrogen economy. The energy carrier is expected to serve as a large-scale storage for renewable energies, split off from water by industrial-scale wind and solar powered plants. In June 2020, the German government rang in the age of hydrogen economy with its “national hydrogen strategy” and a stimulus package worth nine billion euros. It describes the gas as a “key material for a successful energy revolution.” The industry supports this course: turbine manufacturers are converting their products for pure hydrogen operation; the same is true for steal manufacturers and their furnaces. Automotive manufacturers are pushing the development of fuel cell drives forward and are contributing to the establishment of a network of hydrogen fueling stations. The German Chemical association VCI declares that there is “no alternative” to using green hydrogen to reduce greenhouse gas emissions.
Wanted: efficient procedure for hydrogen production
According to recent studies, about 650 terawatt hours (TWh) of green energy would have to be converted to hydrogen in Germany alone to power industrial processes, road and air traffic with the clean energy carrier. In 2019, however, the total production of renewable electricity in Germany was just below 240 TWh—or 46 percent of net electricity generation. These numbers illustrate the magnitude of the challenge ahead. What’s more, the previously established electrolysis processes used to generate hydrogen from power work with efficiencies between 70 and 90 percent, which means up to 30 percent of the electricity used is lost in the conversion process.
At this stage already, lasers can make improvements. In the GreenH2 project, researchers from the Fraunhofer institutes HHI and IFAM, experts from Amphos and further partners collaborated to prove that the efficiency of electrolysis is significantly increased if the metal electrodes are structured by ultrashort pulse (USP) lasers to increase the electrochemically active surface. The long-term stability and electrical conductivity of USP-structured electrodes is also increased.
Splitting water molecules with concentrated sunlight
In future, however, the contribution of photonics to hydrogen economy could go beyond such specific contributions to electrolyser production. Scientists are working on the photocatalytic splitting of water molecules, using light instead of electricity to separate the compound of hydrogen and oxygen atoms.
Currently, three procedures are favoured by hydrogen producers: alkaline electrolysis on the basis of caustic potash solution, polymer electrolyte membrane (PEM) electrolysis with precious metal catalysts and high-temperature electrolysis with ceramic electrolytes. The large EU-funded project Hydrosol is based solely on the solar splitting of hydrogen and oxygen. With several hundred parabolic mirrors, the hot Andalusian sun is concentrated on a reactor, which heats up to temperatures between 800 and 1400 degrees Celsius. The splitting takes place in two steps: First, redox materials such as nickel ferrite or cerium oxide are heated to 1400 degrees in the reactor to trigger a chemical reduction. They release oxygen molecules and fill the resulting gap in the second step by extracting the oxygen from the stream which is introduced into the reactor. The released hydrogen is stored. But currently, the research facility only produces a few kilograms of hydrogen a week and is still far from industrial standard.
RPE.InfraTherm, a Saxon specialist for highly efficient infrared emitters on the basis of coated functional ceramics for the food and construction industry has been driving its own photocatalytic splitting procedure forward for years. At the heart of this procedure is a photo catalyst with an absorbing ceramics coating. According to director Dr. Peter John, the ceramic heats up quickly when hit by concentrated sunlight because it absorbs significantly more photons than it emits. However, he explains, the key to dehydrogenation is the emission ceramic inside the catalyst. The doping causes the functional layer to emit infrared light pulses in the wavelength range between three and ten micrometers in high frequency. In a catalytic process, either methane or steam is heated to temperatures of around 400 degrees centigrade. The infrared light pulses set the molecules to oscillation, causing amplitudes to increase until the atomic bonds break and hydrogen is released. According to the Saxony-based company’s own information, they have achieved efficiencies of more than 30 percent with their photocatalytic splitting procedure and proven its feasibility. Together with their investor SPS Group and a globally active steel group, they will now realize first prototypes. They plan to keep the level of variable costs between 0.05 euros per kilogram hydrogen for splitting water and 0.50 euros per kilogram for splitting methane, while the pure carbon released in this process is very valuable for other high-tech applications.
Material research for photocatalytic water splitting
At the same time, researchers at the University of Vienna are working to better understand the interaction between photons, catalysts and water molecules for a more targeted development of catalyst materials for photocatalytic water splitting. They are seeking to understand precisely what happens at the interfaces before and during the splitting on a molecular level. To understand the reaction path from water to hydrogen and the behavior of the molecules and the influence of photons, they are employing—as you may have guessed—photonic processes. They activate titanium oxide catalysts with UV laser pulses and analyze the reactions on the interfaces using surface vibration spectroscopy. Professor Ellen Mezger-Backus presented their research at the World of Photonics Congress 2019 and on other platforms.
Scientists at the California Institute of Technology (CalTech) are following similar paths. They are searching for catalyst materials that ensure highly efficient photocatalytic water splitting while remaining stable for years or even decades despite the constant binding and release of oxygen. Their search for the ideal material combination is aided by automated, software-based analyses. The race for the most efficient hydrogen generation procedure is well under way. Whether electronic or photocatalytic processes prevail—photonics will certainly play an important role in the solution.