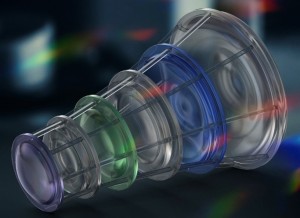
In this interview, Jérémy Picot-Clémente, EPIC’s Photonics Technologies Program Manager, talks to Robert Kirchner, co-Founder and CEO of HETEROMERGE, a German start-up who have developed a printhead system for miniaturized functional 3D multi-material prints with two-photon laser lithography.
What’s the background to you co-founding Heteromerge as CEO?
In 2007, after completing an MSc in Electrical Engineering at the Technical University of Dresden, I studied a PhD in Electrical Engineering focusing on microsystems/MEMS that focussed on UV-nanoimprint lithography as a direct patterning tool for polymeric microsystems exploiting 2.5D and 3D patterns
I’d always been interested in biomedical devices and how semiconductors are made, so after finishing my PhD in 2011, I worked as a postdoc researcher on nano packaging techniques for electronic systems at the University’s Institute for Semiconductors and Microsystems. This was followed by a postdoc position at the Paul Scherrer Institute in Switzerland, where I worked mainly on nanoimprint, electron beam lithography and 3D printing using 2-photon absorption-based laser writing.
On my return from Switzerland in 2017, I became Head of 3D Mesoscopic Systems at the Technical University of Dresden focusing on microsystems and the fabrication of 3D structures. During this period, we encountered a problem in 2-photon laser 3D printing of combining different materials in a single structure with very high precision. Specifically, since back then 2-photon laser printers could only process one material at a time, there was a realignment problem when changing printing materials. In addition, the material exchange was quite time-consuming as it was not automated.
We looked at what was done in other 3D printing technologies and came up with the idea of an open-fluidic system in the form of a multi-material printhead with a fast automated material exchange that could be used with existing 2PP 3D printing technology. This in situ replacement allowed for perfect realignment, and building structures from multiple materials gave them functionality beyond that of a single material. With these features, we were convinced that our groundbreaking technology would have applications, for example, in multi-material compound lens systems, photonics packaging, and multi-material micro needles for the medical sector.
Accordingly, in 2023, two colleagues and I co-founded HETEROMERGE as a spin off from the Technical University of Dresden to commercialize our printhead technology.
How has the company developed?
With funding from the German Federal Government’s EXIST Transfer of Research aid program, we spent two years since 2021 on developing a prototype for pilot customers - the MergeOne - a printhead system based on patented fluidic delivery technology. This device enables automated material exchange with perfect alignment on all substrates together with miniaturized functional 3D multi-material prints with two-photon laser lithography at the highest precision down to the nanometre range. The MergeOne comes with control software, supporting components for upgrading existing 2PP printers, and intensive user training.
In January 2023, we became legally incorporated, and in July, we delivered the first prototype to the Laser Center Hannover, followed by another to the NanoLab of the MESA+ institute, University of Twente in August. Since the project start in 2021, our workforce has grown from 4 to 8 today, including students.
What are the advantages of your technology?
Our open-fluidic system is fully compatible with existing 2PP 3D printing technology and has four main advantages over direct and indirect competitive solutions.
Firstly, the in-situ material exchange during immersion prevents any relative movements of the printer focus and the substrate. This guarantees perfect alignment with a lateral overlay accuracy better than 50 nm between two consecutive material sections - up to 100x better than standard solutions.
Secondly, with the in-situ automated material exchange, you don’t need any manual handling steps to change the print material, making it up to 10x faster than manual material exchange.
Thirdly, our printhead is entirely independent of the substrate chosen for printing, which allows for highly flexible multi-material printing, from small prototypes to large scale fabrication on any surface at a module or even at wafer level.
Finally, our system supports the finest 3D definition: down to 150 nm half-pitch resolution and about 350 nm pitch resolution laterally, and 400 nm half-pitch and 850 nm pitch resolution vertically.
What kind of materials are you able to print and what are your target applications?
We use polymer dielectric materials with various functions, refractive indexes, stiffness, and different compatibilities with biological matter. They are all dispersive materials, so the most promising applications for high volume production are photonics integration and co-packaged optics to improve the efficiency of the couplers and to reduce weight and size by doing it in one single print run. The other applications are life science, medical devices and tissue engineering involving the printing of scaffolds, vascularization and other kinds of very small structures that need high precision and high resolution.
What have been the main challenges since you started as CEO?
The biggest challenge in moving from research to running a business was that as we were a small team with limited resources, we had to become knowledgeable in a wide range of areas such as technical issues, business administration, finance, programming, hardware, software, legal, IP etc.
A requirement of the EXIST funding was that one of the founders had to have a business development background, which was very useful. Nevertheless, I still had to learn a lot and the challenge was not to get distracted while learning and to keep focussing on getting the prototype finished on time while working with minimum resources.
How do you see the see the future?
Our system has removed design, functional and production barriers for the printing of microscopic 3D structures so our customers can focus on their products. Our vision is to go for full additive fabrication of microsystems at the volume level, where the benefits of perfect alignment, speed, substrate flexibility, and the finest 3D definition will be most relevant. For example, instead of putting sub mounts together, a super compact optic lens stack can be directly printed in a single run with the individual lenses made of different materials including also apertures etc..
Over the next five years, we aim to become the enabler for multi-material, high resolution printing by providing the technology and know-how to help our customers transition from prototyping and small volume to larger volume production. Of course, to achieve this, we will need to grow our work force to around 30 and significantly increase our revenue. Another challenge is finance as although we’ve received some business Angel funding and some additional government funding, we have a need to secure seed funding this year.
If you started again, what would you do differently?
In the beginning, we had a lot of advisers telling what to do, what not to do and saying what was and what wasn’t a good idea. Although we listened to what they had to say, we came to realise how difficult it is to convince others of the benefits of the technology, so in the end, we stayed more or less with our original idea.
So maybe, if I started again, I’d spend less time listening to advisers and start earlier - follow my gut feeling and see if it works, and if not, bad luck.
What’s your advice for the next generation of entrepreneurs?
Like I said, in the beginning it’s very difficult to convey to others the potential benefits of your ideas. Basically, the only way to prove your ideas is not to waste time but to put them into practice and see if they work. To do this with minimal resources is difficult and you may fail, but it can also be a lot of fun.
Written by Jérémy Picot-Clémente, EPIC’s Photonics Technologies Program Manager.