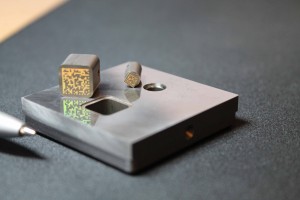
In sectors such as automotive and electronics, traceability is increasingly important, yet it’s challenging to mark plastics and elastomers—particularly for small parts. Most methods are time- and labor-intensive, need additional work cycles, or can contaminate the final product. And some methods carry a large risk of failure.
Traceability is “backtracking” to the origin of a component or ingredients. This capability is essential when making consumables or producing component-laden products like electronics. Should an element be flawed, a firm must launch a costly recall campaign to fix, replace, or refund users.
A medical device manufacturer approached the Danish company, Rel8, seeking an ultra-small barcode to prevent “mix-ups” during assembly. And the firm wanted to read these new barcodes without changing its existing vision system.
Rel8 is a specialist in track and trace and recently launched imZERT direct part marking (DPM) technology that creates barcodes as small as 1mm2 designed to tackle the traceability and counterfeit issues facing the world’s makers, including discrete manufacturers (e.g., automakers) and process manufacturers (e.g., pharmaceutical firms). imZERT barcodes are scanned and decoded via smartphones equipped with commercially available barcode scanning development kits (SDKs), Rel8 found that Code Corporation’s CortexDecoder SDK was optimal for scanning and decoding such small codes.
imZERT technology can help maximize traceability via barcodes made from nanostructures—no small feat considering that a strand of human hair is about 60,000 nanometers in diameter.
The way it works
imZert technology arranges nanostructures, “engraving” DPM barcodes into a mold. This process presses incredibly sharp, high-contrast 2D barcodes directly onto a component’s surface, instantaneously during molding. When scanned, these DPMs reveal relevant data like the lot number or mold cavity ID for tracking and tracing parts or ingredients through production and use.
Traceability is as clear as black and white
Like many innovations, imZERT was born out of necessity. A medical device manufacturer approached Rel8, seeking an ultra-small barcode to prevent “mix-ups” during assembly. And the firm wanted to read these new barcodes without changing its existing vision system.
"The manufacturer had barcode technology in place, but it only worked on a very dark polymer, and they wanted to switch to a white one,” explains Guggi Kofod, Rel8 CEO. “They asked if we could achieve a higher contrast with our nanostructures for better scanning. And that's when we realized what was possible."
In sectors such as automotive and electronics, traceability is increasingly important, yet it’s challenging to mark plastics and elastomers—particularly for small parts. Most methods are time- and labor-intensive, need additional work cycles, or can contaminate the final product. And some methods carry a large risk of failure. imZERT’s relative simplicity makes these all obsolete.
"Most manufacturers rely on barcode labels transferred from packaging or containers,” Kofod explains. “But can you imagine if these get switched around or fall off the box? One mistake creates the risk of shipping wrong parts to an assembly line.”
Errors can be costly—especially to sub-suppliers whose profits rely on a few accounts.
“If this goes wrong a few times, that firm won't sell to the auto factory anymore," Kofod cautions.
The imZERT product traceability system allows manufacturers to quickly identify faulty products (especially during production). If poorly formed parts are discovered during assembly, the manufacturer can go back—not just to the mold but to the individual cavities. Additionally, if a manufacturer expands an existing product’s features, it will perform a revision update in which a mold is easily modified and given a new revision number. imZERT allows all of this to happen without requiring new automation equipment for the new DPM method.
Countering the counterfeits
Beyond medical devices and manufacturing, imZERT’s tiny barcodes can have an outsized impact on fashion, medication, and consumer electronics.
How?
These sectors need to innovatively fight fakes that shrink profits, pose safety risks, and often fund illegal activities. Take, for instance, frugal fashionistas and chic superfakes. Gone are petroleum-scented fake bags with slightly off logos; superfakes are uncanny replicas that meet (or beat) the quality of designer goods.
While these counterfeiters are practically untraceable, their economic disruption is everywhere. The Organisation for Economic Cooperation and Development reported a 154 percent increase in counterfeits traded internationally, rising from $200 billion in 2005 to $509 billion in 2016.
There’s big hope in tiny barcodes
Compared to laser engraving, nanostructures enable creating 1mm2 barcodes with much higher contrast and sharper edges. These features make it easy for powerful barcode reading software, such as Code’s CortexDecoder, to scan and decode. Because they’re the world’s smallest, imZERT barcodes can be easily camouflaged on a fastener or within a bag’s interior liner to verify authenticity for a distributor, detective, or end consumer.
Beyond fashion and electronics, imZERT barcodes can be placed inside containers of consumable liquids, such as medications and ingredients. This is because imZERT barcodes withstand 150,000+ molding cycles without degradation and pose no contamination risk. When scanned with a CortexDecoder-equipped smartphone, recalled consumables are caught before use.
The challenge in scanning super small barcodes
Rel8 found that most barcode scanning technologies couldn’t readily scan imZert’s ultra-small barcodes. This is because quickly and accurately scanning small barcodes presents several difficulties for barcode scanning SDKs. Chief among these challenges is the inherently low contrast of most small barcodes, which creates the need to maximize the camera’s contrast. This is often accomplished by exaggerating the camera’s tilt angle, which can severely distort a barcode, making it difficult for the software to read and decode accurately.
Through trial and error, Rel8’s team came across CortexDecoder, which simplifies scanning while providing industry-leading accuracy. Testing revealed that CortexDecoder could meet all their metrics for speed, consistency and accuracy. This repeatability is due to Code’s engineers optimizing their SDK’s decoding algorithms to read distorted, laser-engraved, low contrast, and even damaged barcodes. Because imZERT’s DPM barcodes are high contrast (and very clear), CortexCoder became a turnkey decoding solution for the tiny barcodes.
"At the beginning, we used a smartphone to film the barcode, another one to enhance the picture, and the last one, which had software on it, to read the barcode,” Kofod recalls. “After this enhancement work, it turned out that we could do that with CortexDecoder. It can also recognize the quality of the barcode in one millisecond; it's that good.”
Although reading a 1mm2 can be possible with other scanning SDKs, Kofod added that success boils down to variables like user skill, environment, and smartphone accessories.
“CortexDecoder on a regular smartphone easily decodes imZERT barcodes down to 2mm2; with some attention to detail, even 1mm2 can be scanned directly,” he shares. “Adding a simple macro-lens to the smartphone ensures that 1mm2 barcodes scan every time [with CortexDecoder].”
Besides traceability and counterfeits, Kofod envisions imZERT for marketing. Thanks to CortexDecoder’s quick and accurate scanning, he sees developers leveraging Code Corp’s software development kits (SDKs) to make their own iOS or Android apps. Through scanning with a branded app, companies can provide users with conveniences, e.g., links to refill pages.
“It makes a good impression if you are talking to a potential B2B customer when the barcode scans immediately,” Kofod adds.
Within industry, smaller almost always means pricier. But compared to any other marking technology, imZERT is very cost-effective.
"We've had an inquiry from an auto manufacturer with two-cavity injection molds that output two parts each cycle. A manual laborer had to pick up the parts and place them in the laser engraving station for each cycle,” Kofod explains. “So, one person and one laser engraving station were only doing this. It’s a process that we could replace for a tiny fraction of the cost."
Written by Dr. Ming Lei is the VP of Technology at Code Corporation.