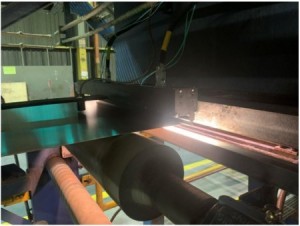
InDeep-solutions specializes in providing comprehensive solutions for production quality inspection and industrial process monitoring, with a focus on in-line inspection across various production lines. With over a decade of experience in process automation, they have developed an innovative inspection system for TI Fluid Systems. This company produces steel strip for the automotive industry, which is later transformed into tubes for brake and fuel supply circuits. Depending on the end customer’s specifications, these steel strips are coated with copper or nickel.
Shortcomings of the previous inspection system
Previously, TI Fluid Systems used a camera-based system positioned at a height of 3 meters above the steel strips. This system was plagued by complex calibration requirements and frequent inaccuracies, resulting in numerous false detections and operational failures. These shortcomings necessitated the development of a more reliable inspection solution.
System requirements
The inspection system must detect every potential hole of at least 1mm in size on steel strips moving at a speed of 95 meters per minute (1580mm/s). Given the critical application of these steel strips in brake and fuel supply circuits in cars, the accurate hole detection is essential to avoid severe consequences.
Development of the new inspection system
InDeep initially experimented with a laser profiler to meet the inspection requirements. However, the trials revealed insufficient frequency and resolution, making the laser profiler inadequate for detecting the small holes required by TI Fluid Systems.
In search of a suitable solution, the company turned to the machine vision experts at phil-vision. Thanks to their extensive experience from numerous integration projects with Teledyne Dalsa components, they proved to be the ideal partner for selecting the suitable camera technology. The specialists suggested utilizing the AxCIS contact image sensor, which was originally developed for battery inspections and print image checks, for a completely different application and using alternative lighting to accomplish the task.
Changing the approach, InDeep decided to test the compact image sensor and selected Teledyne Dalsa’s mono compact image sensor AxCIS (18628x2), a high-speed, high-resolution line scan sensor designed for demanding machine vision applications. This sensor integrated into a compact housing, in combination with an Xtium2 CameraLink HS frame grabber, provided a short working distance and simplified installation without the need for complicated cabling, complex alignment or calibration.
The sensor allows for a high acquisition frequency. For this application, it has been fixed at 10kHz giving a minimum resolution of 0.15 mm in the direction of travel. The resolution along the width of the steel strip is even higher: 0.022 mm. This level of accuracy ensures effective defect detection.
Measurements are gathered and processed in batches of 4,000 lines. This reduces CPU load while maintaining a fast response time of 0.4 seconds. Each image generated is analysed immediately upon release. During processing, the next image is built in parallel.
Tests and result
InDeep has conducted extensive testing, demonstrating the system's reliability in detecting all holes with no misses. The resolution achieved surpasses that of the old camera-based system, with a significantly reduced number of false alarms. In addition, the system accurately pinpoints the position of each hole.
InDeep also developed a customized software that provides high-resolution images and enhances defect detection with specific features tailored to highlight defects. This software plays a critical role in ensuring the effectiveness of the system and is highly valued by TI Fluid Systems.
The software is designed to be very easy to use. Configuration is very simple and once done, no additional human intervention is required.
An example of image with defect is show here, the defect is barely visible
The next image is a zoom to see the defect
Detection is based on threshold crossing. First, the edge is defined as the first point below the level defined in the configuration tab. Holes are then detected when the level rises above the high level also defined in the settings. The next graph shows an example of detection.
An example of detection
Due to the very high resolution and the small size of the holes, the defects are highlighted with a red rectangle so that the operators know where to look for it. The software can display the last 10 holes detected. In addition, all the detected defects are stored on the hard disk for 6 months.
The defects are highlighted with a red rectangle so that the operators know where to look for them
Collaboration with phil-vision
The project involved extensive collaboration with phil-vision. Thanks to its many years of experience in a wide range of integration projects with cameras and image processing components from Teledyne Dalsa, the system house from Puchheim was the perfect partner for selecting suitable components. The machine vision experts provided crucial support in the selection of suitable components. After inDeep-Solutions originally wanted to implement the project using a laser profiler, but this did not deliver the desired results, they turned to phil-vision.
The specialists recommended ‘repurposing’ the AxCIS contact image sensor, which was originally developed for battery inspection and print image control and using a different type of illumination to solve the problem. As the AxCIS sensors are small, quasi-telecentric line scan cameras, they are also ideally suited for highly precise measurement tasks. phil-vision then provided a test sensor for feasibility studies and assisted with sensor timing, programming and software integration, thus contributing to the successful implementation of the inspection system.
Summary
InDeep-solutions successfully developed an advanced inspection system for TI Fluid Systems, that solved the challenges of their previous setup. Using Teledyne Dalsa’s AxCIS sensor and customized software, the new system provides superior resolution, reliability, and accuracy in detecting small holes in steel strips. The collaboration with phil-vision and the use of the high-speed contact image sensor from Teledyne Dalsa was instrumental in achieving these results and represents a significant improvement in production quality control for the customer.
Images
Transport of steel strip
Teledyne Dalsa AxCIS mounted above steel strip
About Indeep-Solutions
Indeep-Solutions specializes in delivering innovative, high-performance solutions tailored to the specific needs of modern industries. Founded on the principles of precision, efficiency, and technological expertise, the company is dedicated to developing advanced systems that streamline production processes, improve quality control, and enhance operational reliability.
With a strong focus on automation and detection technologies, Indeep-Solutions has become a trusted partner for clients seeking cutting-edge tools to meet demanding challenges. From automated inspection systems to real-time data processing platforms, the designed solutions combine robustness and ease of use, ensuring seamless integration into existing workflows.
About phil-vision GmbH
phil-vision GmbH is a specialist in machine and computer vision with a comprehensive range of services. As a value-added distributor of image processing components from leading manufacturers with many years of integration expertise, we are not only a system house with clear added value for our customers, but also the ideal consultant and partner for integrators in the selection of suitable machine vision components.
Based on many years of experience, we develop image processing subsystems and realise intelligent, customised solutions for demanding image processing tasks in a wide range of industries and applications. The range of services is rounded off by a training programme covering a wide range of machine vision topics.