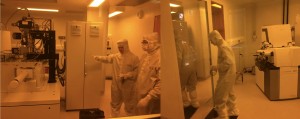
Electron beam lithography (EBL) is a technology commonly used to manufacture small devices in computers, photonics and sensors. Because this relies on accurate positioning of the electron beam, it is very sensitive to interferences such as stray electromagnetic fields and vibrations. Reearchers at the Centre for Microscopy and Microanalysis (CMM) at The University of Queensland (Australia) describe how they overcame the interference problem.
CMM is an electron microscopy (EM) facility involved in research and teaching, as well as providing consultancy services. The centre offers expertise in different EM technologies and has recently built a new clean room where computer, photonics and sensor devices are fabricated using EBL. However, the new facility immediately began to present real challenges to the researchers when they started observing unexplained background noise in their data.
Elliot Cheng explained: “The devices we’re making are extremely small, and it’s therefore crucial that the electron beam is accurately positioned. This is unfortunately something that is greatly affected by any magnetic interferences. Ideally, levels on this kind of application should not be higher than 0.5 milligauss, but we were seeing peaks located around 50 Hz that were relatively much higher, which jeopardised the accuracy of the instrument.”
“We used the Spicer SC11 analysis system to scan for factors that might cause this interference around the lab. It was extremely convenient to have a portable sensing system that allowed us to pinpoint the sources of noise without having to call in an external contractor. We first investigated the vibrations, which we quickly realised were not causing the problem, then moved on to checking the AC magnetic fields, looking at the contributions from various frequencies. When that proved fruitless, we analysed the DC fields and found that this was the root of the issue. This led us on a ‘ghost hunt’; we walked around with the SC11, turning different instruments on and off, moving the elevators, all while constantly measuring the changes in the field. We eventually found that some of the spikes attributed to the elevators, which was not surprising, but another unidentified, periodic source with a one-minute cycle remained. We eventually tracked this down to being caused by the inductive heating of the lab.”
“Although we had the answer, it didn’t really help us solve the issue. We couldn’t remove this source of interference, and started to schedule our runs between 11pm and 4am, when no one else was in the building. Some of the processes were automated and we could get around this by programming them in advance, but this really limited the usability of the instrument. We therefore decided to purchase the Spicer SC24 magnetic field cancelling system, and immediately noticed a significant reduction in the noise, going from around two to just a few tenths of a milligauss. We no longer have to worry about moving elevators or the nearby traffic. The location of the sensors still needs optimising, to get the best performance out of them, but the instrument is already doing a great job now that the problem of interference has been mostly eradicated.”
Roger Wepf continued: “I have worked with Spicer for a long time; I started using the company’s products around 1996, and have used its instruments to perform an environmental survey whenever we have installed a new instrument. I believe that it is absolutely essential to have a Spicer analysis system in every EM lab, because it saves a lot of time, and gives the team the freedom to perform on-site measurements as soon as they are needed, or if changes to the environment occur.”
Spicer Consulting magnetic field cancelling systems protect electron beam instruments, including Scanning Electron Microscopes (SEM), Transmission Electron Microscopes (TEM), Electron Beam Lithography tools, SEM-based metrology and inspection tools in the world's leading laboratories, universities, semiconductor manufacturing plants, as well as in the test facilities of electron and ion beam equipment manufacturers. Its magnetic field, vibration and acoustic analysis systems have been adopted as standard equipment for the conduct of site surveys by leading equipment manufacturers.
Written by Elliot Cheng, EBL Specialist, and Roger Wepf, Director of the Centre for Microscopy and Microanalysis (CMM) at The University of Queensland,