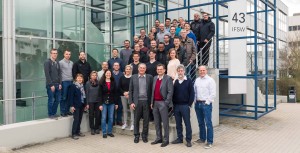
In this article, Jose Pozo, EPIC’s former CTO, talks to Thomas Graf, Professor and Director of the University of Stuttgart’s Institut für Strahlwerkzeuge (IFSW), a leading developer of laser technology for industrial applications.
Early career
With a passion for science since high school, in 1991, Thomas graduated with an MSc in Physics from the University of Bern. Having developed a fascination for lasers he then studied a PhD in Physics, which focused on the development of high-power lasers for industrial applications. After receiving his PhD in 1996, he chose to stay in academia and worked as a postdoc researcher in applied physics at the University of Bern, and then from 1998 – 1999 at the University of Strathclyde in Glasgow. Working in Scotland was interesting because it gave him invaluable cross-cultural experience and also the opportunity to work with fundamental physicists on experiments with atom traps, which led to him making the first high-power mode-locked trap for laser-cooled atoms.
In the 90s, industry began to shift from CO2 to solid-state lasers, but to become mainstream they required power scaling. To this end and convinced that solid-state lasers would soon enter industrial manufacturing, in 1999, Thomas returned to Bern as Head of the university’s High-Power Lasers Group, where he worked mainly with rod lasers.
In 2002, he received a lecturing qualification and became Assistant Professor and Head of the High-Power Lasers Group. Then in 2004, he was persuaded by his Head of Department to apply for the position of Professor and Director of the Institut für Strahlwerkzeuge (IFSW) at the University of Stuttgart, which was shortly to become vacant. The IFSW had been set up in 1986 to develop laser technology for manufacturing applications with an emphasis on R & D work and teaching activities. His initial reaction was that he didn’t have enough experience for the job. Being a senior scientist managing a team of 12 researchers at Bern was not the same as a Director of a prestigious institute like the IFSW with a workforce of more than 30.
Nevertheless, the prospect of working at the IFSW was attractive as not only could he continue to develop lasers he could also develop industrial applications for them. With nothing to lose and encouraged by his girlfriend, he decided at apply, and to his astonishment he was offered the post.
Development of IFSW
One of his first priorities was to streamline the organisation by closing two companies that had been set up under the auspices of the institute. Working with different entities made the management of people and resources difficult and closing the companies meant they only needed to focus on a single unit - the institute itself.
Since 2004, the IFSW has grown to a workforce of 50 and its scientific activities now range from fundamental scientific investigations and developments to demonstration projects for industrial applications. Their work is organised in three divisions: 1) Laser Development and Optics - to develop reliable and powerful laser sources, especially thin-disk lasers and laser systems with specifically optimized properties for different fields of application;2) System Engineering - focused on solutions for highly dynamic beam delivery, the design of machines and systems, laser safety, and the integration of laser sources; and 3) Process Development - concerned with the interaction between laser beams and matter to develop improved laser-based manufacturing techniques for processes like ablation, drilling, joining, cutting and additive manufacturing.
In order to work efficiently on complex research and development projects, the IFSW has a holistic approach in that the three divisions work in collaboration to achieve the strategic goals of the institute. To this end, Thomas meets regularly with the three divisional directors, sometimes including the PhD students, to review the development of the laser technology in general and to try and figure out future needs. This is not always easy as although they need to say ahead of the industry, at times they have to respond to current demands.
As an example of a specific project, a major advance was made in 2015, when the IFSW, in collaboration with Trumpf Laser, demonstrated a multi-pass thin-disk laser amplifier generating record output powers. The laser’s architecture was originally developed as a solution to a spectroscopy problem with hydrogen muons that required a laser that could generate a high-energy pulse over just a few hundred nanoseconds to take the measurement. Based on this experience they came up with a kilowatt multi-pass thin-disk laser amplifier, which had important industrial applications like cutting carbon fiber and reenforced plastics. This was a huge benefit to the IFSW as they were able to demonstrate their holistic approach, that is, not just engaging with blue sky research but also thinking about how the research can be applied to industry.
The Future
As Thomas explains, in the 90s the challenge was how to improve laser performance in terms of better beam quality, longer lifetime and higher power. But everything has changed: lasers now have plenty of power and beam quality - even for ultra-fast lasers, and currently, the main problem is with the machines. More precisely, the problem is that the laser power available cannot be exploited to scale productivity because the new generation of lasers require much faster and more precise machines. In other words, the bottleneck is now the system engineering and not the laser sources. To address this challenge the IFSW have created a new professorship that will be focused on system engineering.
A second concern for IFSW is how to tap the flexibility of the laser tool. For many decades lasers have been presented as a universal tool that can do everything. But in practice, for example, when Daimler buy a laser for welding, they buy a continuous wave (CW) laser, and for structuring an ultra-short pulse laser. This has to change, and the idea is to build a single laser that that can operate in both modes. The problem is more technical than scientific and in theory, it's only a small step to set up a laser in such a way that can operate in either CW or pulsed mode at the flick of a switch. Such a system will make manufacturing and design processes a lot more flexible as the same laser can be used for welding, cutting, drilling or structuring.
A good example where CW and pulsed lasers in the same machine would be an enormous advantage is in relation to a current project involving the printing of stators for electric motors. The project is part of a larger collaboration between University of Stuttgart and the Karlsruhe Institute of Technology, who together created an innovation campus for future mobility to find new solutions for the automotive industry and to develop the production technology required to make these solutions a reality.
The stators, which provide a magnetic field that drives the rotating armature, are printed by 3D laser powder bed fusion using a CW laser, a process which is both scalable and gives a much higher freedom of design compared with conventional manufacturing.
The problem is that air gaps must be left between different sheets of material, but due to the lack of precision of powder bed fusion the gaps were not very precise - causing a bottle neck. As a solution, after printing of each layer of the components with a CW laser, an ultra-fast laser is used to shoot the slits open again with much better precision down to some 30 microns, before the next layer is added.
As Thomas points out, so far, the industry has done well selling two different lasers. But sooner or later a company will come on to the market with a laser that can do both ultra-pulses and CW operation. Then, the industry will have a truly universal tool that can be used for most of the laser-based material processing processes that are currently applied in industry.
If you started again, what would you do differently?
So far, everything has gone rather well, and I haven’t made any huge mistakes. If I had, I’d think about doing things differently. I was never fixated about becoming a professor, I just wanted to do science. I had a type of juvenile, light-hearted way of looking at life. I was happy to do research and was not obsessed with success. As a matter of fact, doing good science automatically leads to success. I’ve always been open-minded enough to take chances and I think I would do this again.
Having said that, when I was young, I was just fascinated with science and went from one solution to the next without thinking too much about the future. Of course, once you are the director of an institute you have to be more strategically oriented. So, if I started again, I would probably start to think strategically a little bit earlier but try not to lose the enjoyment or the enthusiasm for science.
What advice do you have for the next generation of scientists?
The main thing I’d recommend is not to be too fixated on an outcome. Try to enjoy the science and stay open-minded to new opportunities. Irrespective of age, it’s never too late to adopt this attitude to life.
Written by Jose Pozo, Chief Technology Officer at EPIC (European Photonics Industry Consortium).