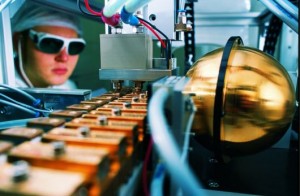
At the leading trade fair for plastics and rubber, the “K” in Düsseldorf (Germany), Jenoptik’s Lasers & Material Processing division is to demonstrate its competence in the fields of plastics processing and exhaust air purification.
The Lasers & Material Processing division of Jenoptik will present solutions for welding, cutting and perforating plastic materials in hall 11, at booth no. C45, Jenoptik will present the Jenoptik Votan W series for laser welding, the JenLas disk IR70E disk laser, a fiber-coupled diode laser module and Katasorb Print, the new system for exhaust air purification in the printing industry.
Non-contact laser welding with the Jenoptik Votan W
Thanks to the latest laser technology, new fields of application in material processing keep opening up. In the fields of plastics cutting, welding and perforating, laser technology is an established and recognized practice, for example in the automotive and supply industries. Due to the increase in vehicle interior equipment and the growing demand for safety, automotive manufacturers face one new challenge after the other. These can reliably be mastered by using the Jenoptik Votan W.
At the “K” plastics trade fair in Düsseldorf, Jenoptik is to show its latest development in the field of plastics welding: In order to broaden the field of application of transmission welding, Jenoptik has developed a welding process involving a laser line that can be switched on and off in sections. This novel process has successfully been applied in the industry several times already.
The non-contact joining method without any mechanical and thermal influence is not the only essential benefit of this new technology. It also brings high productivity and comparatively low operating costs. This innovative method is applied in the transmission welding of large plastic components, e.g. welding of shot channels in instrument panels or welding of door linings.
Innovative Jenoptik diode lasers with a width of 10 millimeters (mm) and an optical laser power of up to 100 watts per submount for the standard wavelengths of 808, 940 and 980 nanometers are used for the newly developed laser welding technique. The diode laser line, that can be switched on and off in sections, comprises eight diode laser submounts in a compact housing and generates a line of about 100 mm in overall length. Each submount can be switched on and off individually based on the contour to be welded and thus produce nearly any welding geometry. By combining several diode laser lines in one overall line, the so-called diode nest, nearly all component sizes can be welded in a highly productive way during one and the same passage. All in all, an area of maximally 1,500 mm x 600 mm can be welded in one passage.
Inside the laser welding machine, the diode nest moves along a linear axis, across the components to be joined, and firmly welds them to each other without leaving any marks (sinks) on the top surface or causing any thermal distortion – at welding speeds of up to 100 mm/s. In order to ensure a constant weld quality, the entire welding process is made subject to online process control for quality assurance. When directly comparing this to alternative joining technologies, the strengths (pulling forces) of the welded joint in the boundary area and of the cover are 25 percent higher on average.
Experience a live demonstration of the switchable laser line of the robot system, the heart of the Jenoptik Votan W laser machine, at the “K” in Düsseldorf, hall 11, booth C45, from October 16 to 23 2013.