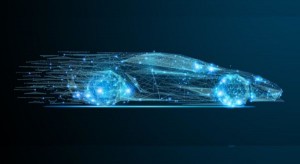
The vehicle of the future will be autonomous, electric and will run with low emissions. Photonics are a key enabler in this development. They facilitate the efficient production of batteries, fuel cells and electric engines, and guarantee both effective lightweight design and safety with automated driving. Leading players in the photonic-driven transformation will meet this year from April 26 to 29 at LASER World of PHOTONICS.
Thanks to a proven protection and hygiene concept, the trade fair will take place on site at the Munich exhibition center.
Electromobility is coming
A look at the battery projects announced in Europe alone eliminates all doubts. Almost 40 cell factories in twelve countries with a total capacity of 1,200 gigawatt hours (GWh) are planned here by 2030. Factories for fuel cells, which will guarantee long-distance mobility with hydrogen as the energy source, are also under construction. Along with this transformation of the drive systems, automotive manufacturers are also focusing on lightweight design – the more weight is saved with multi-material concepts, without sacrificing occupant safety, the higher the range and the lower the energy requirements. And as if that wasn’t enough, vehicle networking and automated driving are also making enormous progress.
Laser processes for new variety in electric powertrains
Laser processes and photonics play a key role in all innovation areas.LASER World of PHOTONICS exhibitors provide the required stimuli here. The bipolar plates used to build fuel cell stacks, for example, are welded and formed with laser processes from TRUMPF, Precitec, Blackbird or RAYLASE. Companies such as ZEISS or 4D Photonics drive the process monitoring, while teams fromthe Fraunhofer Institutes for Laser Technology (ILT), Production Technology (IPT), Telecommunications (HHI) and Material and Beam Technology (IWS) further develop the laser processes.
As the fuel cell market moves up a gear, solutions for battery production are also booming. TRUMPF reports they have tripled in just three years. The company delivers laser technology to all major battery manufacturers, with over 500 lasers projected for the first six months of 2022 alone. More than half of all automotive revenue here is from solutions for electromobility. Laser processes now have a firm foothold in both cell, module and battery production and in the manufacturing of electric motors and power electronics. As the energy input in the process can be controlled precisely, lasers ensure clean cutting edges and weld seams, with minimum mechanical and thermal stress on the surrounding areas. They also deliver more efficient and therefore cost-cutting processes.
Demanding welding and cutting tasks
The wide-ranging repertoire of photonic solutions is most evident with copper cutting and welding. The reflective non-ferrous metal is omnipresent in electric vehicles as micrometer-thin anode material. For connecting battery cells and modules. In the electric motors and power electronics. But due to insufficient absorption, infrared laser light, commonplace in laser processing, reaches its limits here. Coherent solves the problem with the aid of the ARM (Adjustable Ring Mode) strategy. The fiber laser’s processing spot is surrounded by a light ring, which precisely increases the absorption in the processing area. The process consequently runs swiftly and spatter-free. Laserline and RAYLASE achieve this result with blue diode lasers and precise deflection units. As copper absorbs blue light much better, speedy multikilowatt processes are possible. TRUMPF on the other hand uses the green, also well-absorbed light of its disk lasers to weld the non-ferrous metal.
Short-pulse lasers are often used for cutting the micrometer-thin copper and aluminum films of electrodes. Lasers are also required for drying electrode films that have just been coated with active material. TRUMPF replaces bulky energy-intensive ovens with semiconductor VCSELs here. Laserline and the Fraunhofer Institutes for Laser Technology (ILT) and for Production Technology (IPT) also focus on energy-efficient drying per laser.
New laser processes for more efficiency and quality assurance
Exhibitors such as SCANLAB, SCANSONIC or IPG Laser have also evolvedinto electromobility enablers with their production solutions. Along with their concepts for efficiency improvement, production-related quality assurance is also critical in reducing battery costs. Providers such as ZEISS, Keyence or Mahr, who, with imaging, analytical and metrological processes, ensure that the electrode films are coated homogeneously and uniformly and that electric motors, bipolar plates and the increasingly more densely packed powerelectronics comply with the required quality parameters. Their solutions then allow developers the required deep microscopic and spectroscopic insights, on the basis of which they can optimize battery chemistry and the assembly of anodes, cathodes and separators.
Photonics also provide pivotal impulses for the production-related handling of fiber-reinforced plastics and for durable bondings between the most diverse metals and plastics of a multi-material lightweight design. A consortium of the LASER exhibitors neoLASE, Coherent, Sill Optics, PRIMES and LZH, just recently developed an innovative diode laser for this with nine individually controllable laser spots. The temperature in the weld seam can therefore be regulated depending on the local thickness and quality of the material and the required weld seam geometry. The team succeeded in firmly bonding pre-laser structured metals with plastics. In another project the Fraunhofer IPT developed energy-efficient processes for new fiber composites, cold hardened under UV irradiation.
Photonics as enablers for lightweight design and autonomous driving It is precisely this combination of precision, flexibility and innovative spirit with which the photonics industry establishes itself as a key solution provider for the mobility of the future. The leading players will present themselves at LASER World of PHOTONICS in Munich from April 26 to 29, 2022. They include various providers of environment sensors for autonomous vehicles. Jenoptik, Hamamatsu, eagleyard, Viaoptic or the Fraunhofer Institute for Photonic Microsystems (IPMS) – they all have something up their sleeves for the LiDAR (Light Detection and Ranging) technology, which scans the vehicle environment per laser for a few hundred meters. With a micromirror, for example, which steers and detects the laser beam in two dimensions and at the same time records the spatial depth between object and detector using the light’s travel-time measurement. Unlike rotating mirrors, the tiny, monocrystalline silicon MEMS scanner is robust, shock-resistant and fatigue-proof, and thanks to more economical, established semiconductor production processes, is also quickly upscaled to industrial scale.