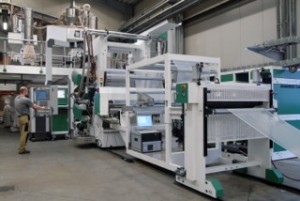
The Fraunhofer Institute for Laser Technology (Fraunhofer ILT) in Aachen, Germany collaborated with the Institute of Plastics Processing (IKV) at RWTH Aachen University, also in Germany, to develop an optical film inspection system for multilayer films. The InnoNet project, as it is called, has concluded with successful testing of the system on a flat film line under production conditions.
The challenge faced by manufacturers of multilayer films is to make the functional layers thick enough to guarantee quality without using excessive amounts of material. This is why precise film inspection systems are critical in monitoring the thickness of each individual layer simultaneously at production speed. An out-of-tolerance reading immediately alerts the manufacturer to adjust the quantity of material used in response to the inline measurements. According to Fraunhofer ILT, there currently is no other tool on the market capable of performing these inline measurements in real time, during production.
Furthermore, the film inspection system aides in ensuring even distribution of the functional layer across the film's entire width. Due to the way it is produced, however, the functional layer does get thinner towards the edges, forcing manufacturers to trim it on either side, which represents a significant waste of material. So it quickly becomes evident that the inline measurement system’s ability to determine precisely where this drop-off in thickness begins is critical for minimizing this wastage. Without Fraunhofer ILT’s innovative measurement system, manufactures of plastic films typically investigate the thicknesses of the individual layers of their multilayer products randomly after the production process. “With our continuously running inline inspection systems, the time for detecting errors has been shortened considerably,” says Stefan Hölters from Fraunhofer ILT.
Applying knowledge to flat films
Hölters and his colleagues have completed long-term measurements covering a period of more than 12 months and were able to attest the optical inline measurement system’s suitability for continuous use on blown films. They now have applied the results to flat films: Under close-to-real-life manufacturing conditions, the experts successfully operated the optical measurement system in a series of tests run over a period of several days.
Hölters explains the optical technology behind the film inspection system: “The interferometric sensor uses infrared light to detect changes of the refractive index within the measuring range. In a single one-dimensional measurement the distances to one or several interfaces can be detected simultaneously, with micrometer accuracy.” The German engineer goes on to explain what specifically is new about his film inspection system and represents an advance over existing technologies: “In comparison to capacitive sensors that are often used for the inline detection of the total film thickness, the interferometric sensor is capable of investigating the single layer’s thicknesses as well.”
Regarding the research that went into the development of the optical technology, the engineer says that interferometric sensors are known to reach highest accuracies in distance and thickness measurements. “The main goal of our activities was the transfer of the technology from the laboratory into the industrial environment. Therefore, the setup had been downsized and stabilized against shocks, vibrations and temperature variations.”
Analysing the data
The next step for Hölters and his team will be to focus the development on data analysis to draw more information from the detected signals. Furthermore, he says he expects the performance of the sensor components to improve. “For example progress in the sector of CCD sensors — like higher sensitivity and higher measuring frequency — will directly be of advantage for the interferometric sensors,” the researcher concludes his outlook.
Written by Sandra Henderson, Research Editor, Novus Light Technologies Today