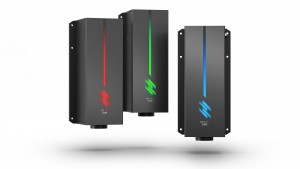
In this interview, Antonio Castelo, PhD, EPIC’s Technology Manager for Bio-Medical and Lasers, talks to Tim Kunze CEO of Fusion Bionic, a German manufacture of modular solutions based on Direct Laser Interference Patterning (DLIP) technology for laser-based surface functionalization.
What’s the background to you co-founding Fusion Bionic as CEO?
In 2009, I went to the Dresden University of Technology to do a PhD on the simulation of Tetrahedral Amorphous Carbon coatings using molecular dynamics. Although the work was very interesting academically, it had no real-world applications and a limited impact. So when I finished my PhD in 2013, I joined Fraunhofer IWS in Dresden as a Senior Researcher with the aim of using my knowledge of computational and natural sciences to do something useful for mankind.
I started out at Fraunhofer in 2014 first as an application engineer and later as R & D Project Manager in the field of surface functionalization using laser-based processes. During this period, we developed the first industrial-grade DLIP machine for demonstrating interference patterning to improve the surface performance of various materials. Our inspiration were the surfaces created by nature such as the lotus leaf, sharkskin, and morpho butterfly. What we wanted to do was to use laser-based surface functionalization to reproduce the properties of these natural surface on metals, polymers etc. to create advanced surface features such as self-cleaning, anti-icing, antibacterial, decoration and drag reduction. In 2017, I became team leader of the surface functionalization group and dedicated all my energy to further industrialize the DLIP technology together with a passionate team from Fraunhofer and the Technical University Dresden.
We spent several years building more DLIP hardware, getting a better understanding of the technology and how to scale it. We also explored various applications by talking potential end-users and though these discussions I came to realise more and more the commercial potential for laser-based surface functionalization. Accordingly, in 2021, three partner and I co-founded Fusion Bionic as a spin off from Fraunhofer IWS to commercialise the technology.
How has the company developed?
In the last three years, we’ve developed two products - the CORE series, a versatile interference module, and the CORErapid series, a scanner-based interference module. These devices are based on Direct Laser Interference Patterning (DLIP) whereby laser beams are combined in a controlled manner to create a defined interference pattern within the machining area. The patterns can be transferred into almost any material, from metals to polymers to ceramics, coatings and glass for applications including decoration, holograms & matting, light control, self-cleaning & wetting, and biocompatibility. We’ve also built an application center to help people understand the capabilities of our technology and how it can be used to advance their products. It also offers a demonstration area for ultrafast laser processes with the latest laser sources and large-scale equipment.
In 2021, we closed our first round of pre-seed funding and in the same year we were selected by Heraeus as one of ten winners of its 2021 accelerator program from more than 1800 global startups. In 2022, we began our first strategic partnerships, such as with MOEWE optical solutions, to push the boundaries of ultra-fast surface processing. Later that year 2022, we were also awarded the Biomimicry Institute's Ray of Hope Prize as one of the world's best nature-inspired start-ups.
Till today, our workforce has grown from 4 to 18 and we’ve nearly doubled our office and production space from 450 to 800 m2.
What are the main applications?
Our DLIP technology offers a completely different solution as the new standard for surface functionalization. Firstly, it has excellent potential replacing ecologically harmful and expensive processes, such as chemical etching, sandblasting, or plasma. Additionally, traditional methods using coatings or lithographic processes are more and more inapplicable, ineffective or inflexible to achieve required pattern for a range of materials and applications. Laser solutions offer extreme advantages here, especially as a sustainable tool with a perspectively CO2-neutral footprint. Secondly, our DLIP technology boosts the processing speed compared to established laser methods, whereby functional surfaces can be created at a speed of up to 3.26 m²/min, enabling cost-effective industrial production of functional surfaces. Nowadays, laser sources have become the limiting factor.
Our technology is well suited for applications in photovoltaics, for example, to improve yield efficiency and reduce surface contamination through dust and dirt on glass surfaces used in solar panels. Similarly in automotive, the benefits of our DLIP method include improved bonding and adhesion between surfaces, improved lubrication, and clearer optical properties of sensors due to anti-fogging effects. Medical technology can also benefit from improved efficiency for medical diagnosis, tailor-made contact mechanics, and anti-sticking functionalities. For some time now, we have also had strong activities in the field of semiconductor technology.
Who are your main customers?
Our customer landscape is diverse and extends along the value chain from end users to technology providers and material manufacturers. We also love to work with laser suppliers, machine builders, subsystem providers for monitoring systems and beam shaping & optical system providers.
What are your main target markets?
We’re currently focussing very strongly on the direct processing of glass surfaces to give them new properties such as anti-glare, anti-fogging, anti-slip and anti-reflection. Our laser technology provides a serious alternative to coatings, chemical etching or sand blasting processes. There's a huge variety of industry demands for glass surface processing particularly for anti-soiling and an anti-contamination functionality, e.g. for cover glass used in photovoltaics panels. Our aim here is to scale our technology platform to be able to process PV glass covers at speeds of up to 3.26 m2 /min. As our DLIP technology is a platform technology for large-area surface processing, it can also be used for roll-to-roll and other mass production processes.
What have been your main challenges?
Apart from the mammoth project of creating a completely new company from scratch, the biggest challenge lies in the novelty of the technology itself. Quite a few branches of industry are conservative or subject to strict regulations, such as medical technology. Furthermore, many applications are very complex and require longer evaluation times. Nevertheless, more and more people are investing in this technology, which is currently leading to the establishment of further application centers in Taiwan and Japan, for example, and we are a little proud to be able to accompany our customers on this journey. Successful applications also present us with the challenge of building up more capacity in contract manufacturing. In the future, we will have to work more closely with job shoppers to meet demand.
What techniques have you found most effective in increase the visibility of the company?
In the beginning – around May 2021 - we made a coordinated marketing campaign with Fraunhofer and EPIC, and we got some good media exposure from being selected by Heraeus as part of its 2021 accelerator program. We also prepared a lot of marketing material including samples and photos of the surface textures we could achieve, and of course, we’ve been present on all the social media platforms from day 1.
Additionally, we’ve attended exhibitions like Glasstec and Photonics West, and in November 2023, we organised our first of its kind event - the 1st Bionic Laser Forum in Dresden, Germany, which brough together experts and researchers, to explore the intersection between bionics and laser technology. It was a great success, especially since we were able to coordinate this event with our former colleagues from the Fraunhofer IWS shortly before the regular laser symposium.
How long does it take to convince customers to adopt your technology?
It depends on the sector. We have various early adopters who see the benefits immediately. Our first products were basically flexible development tools, which we sold to academic institutions and larger companies who were already using laser machines and knew how they could adapt our technology to advance their surfaces. In the medical sector it takes much longer as you not only have to demonstrate the effectiveness of the technology to clinicians and medical devise builders - there are also legal hurdles to jump over. As we are able to exploit the speed advantages of our products – especially our CORErapid - more and more, we are increasingly being approached by companies that are inexperienced with lasers and are driven by the law to substitute existing manufacturing processes.
What’s your advice for the next generation of entrepreneurs?
Firstly, just do it. At Fraunhofer, I had a very stable position with a good salary. But I wanted a new challenge and to grow on a personal level and I was convinced that setting up my own company would enable me to do this.
Secondly, you will need to develop a mindset that’s resilient because it’s really an exhaustive path, it’s not easy and it won’t happen overnight.
Thirdly, you can’t do it on your own. Build up a good team with people you can trust and go into partnerships with customers and join industry associations like EPIC.
Fourthly, don’t over engineer things. Thers's no such thing as a perfect product. You need to start with a minimum viable product, which works, and you can show to a customer. You can then get feedback and make improvements and/or adjustments where necessary.
Finally, listen to what the market is saying. Academics in research tend to imagine what customers need, but they’re invariably wrong. We started with an 80-page business plan, but when we went out into the market and learnt what was really needed, we completely changed direction.
Written by Antonio Castelo, EPIC’s Technology Manager for Bio-Medical and Lasers