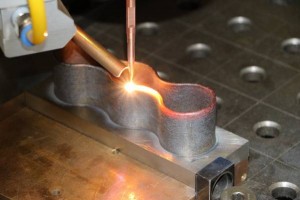
Additive laser manufacturing processes are revolutionizing the market: The market for laser systems for additive manufacturing has increased annually by more than 25% in the last five years. In particular, additive manufacturing of metal parts has been the main reason for the strong market growth, according to Optech Consulting. Additive manufacturing processes can be broken down into two main areas: whereas complete component production using laser construction technology is still in its infancy and is responsible for the strong growth, laser deposition welding with powder or wire has been established for many years. Laser deposition welding is used to carry out high-quality repairs and modifications of components from turbo machine production, toolmaking, mold-making and many other branches of industry. LASYS 2018, which will be held in Stuttgart from 5–7 June 2018 as a trade fair for laser material processing, will also focus on additive laser manufacturing processes. Efficiency, cost-effectiveness and productivity will be the focal points in this respect.
New machine concepts make laser deposition welding even more efficient
The CEO of OR Laser says one of the biggest advantages of laser deposition welding is that welding into the component can be carried out on freeform surfaces with a near-neat shape. Since the amount of energy required is very low, only small material distortions occur, which means only a small machining allowance is necessary — a major advantage during re-machining, compared with other welding technologies. Based on the example of tool modification of an injection moulded part using the direct metal deposition (DMD) process, the company shows that substantial time savings are possible from the third component onwards.
For example, Laservorm’s laser production systems are used to produce high-temperature-resistant thermal barrier layers on aircraft turbine components or to repair components in power station turbines. They integrate, for example, both the adaptive machining process and part measurement processes in the CNC control system, so data need not be transferred to external systems, according to the company, which enables them to synchronize measurement routines relating to the machining process with the CNC control system in real time. The bi-axiai, piezo-driven adjustable mirror system LV SpinScan is able to display fine and coarser weld beads in a ratio of 1:5. Therefore, the machine maker can influence the weld bead geometry during machining.
When integrated in machine tools, lasers optimize production processes
The CEO of Laserline projects that the integration of laser beam sources in machine tools is one of the most promising approaches for optimized production processes. Diode lasers are therefore used, for example, in a five-axis milling machine where they allow switching between additive and subtractive processing. The laser deposits the powder while the milling head cuts the metal. The various applications of their diode lasers provide additive manufacturing with other options beyond the interaction between additive powder deposition and subtractive metal cutting. Lasers can be integrated, for example, in lathe turning/milling centers and can be used, apart from power deposition, for welding and hardening. In addition to the laser and powder nozzle, corresponding optics are installed for this purpose. Depending on the processing operation, it is possible to switch between these optics. Ultimately, complex manufacturing processes can therefore be carried out based on a single beam source, saving time and costs.
Fiber lasers produce impermeable 3D solid bodies
The fiber laser systems from IPG Laser use laser deposition welding to repair, for example, shut-off valves, crankshafts, O-rings, etc. Additive manufacturing was originally developed for prototype construction. However, according to an IPG Laser project manager, additive manufacturing processes have now become an entirely new industry for the production of 3D solid bodies.
Metal powder is melted layer by layer using laser technology to produce a complete component. These methods benefits from recent improvements in computing power and movement and process control of laser production systems to precisely deposit many different materials at high speed. Selective laser melting (SLM) produces completely impermeable metal parts with improved mechanical properties. IPG Laser’s fiber lasers in the YLR series are utilized in this area and can be integrated compactly with up to 2 kW in a 19" rack design.
Additive generative manufacturing also affordable for SMEs
The CEO of OR Laser emphasizes that in times of increasing digitalization and Industry 4.0, the production environment of the future will require ever more intelligent systems and solution approaches along the entire process chain of additive manufacturing. His company has therefore developed a high-end 3D metal printer for components and designs that feature virtually any geometrical shape but cannot be produced using traditional manufacturing methods. This printer will also be presented at LASYS 2018. The company aimed to make 3D printing accessible and, thus, affordable, for both prototype manufacturers and small and medium-sized companies, e.g., in the designer, dental technology and jewelry industries. They believe to have achieved this with their latest development. Components with filigree structures, high surface quality and a high density are built up quickly and easily without using any additional tools. The print data is therefore handled and processed directly from the CAD file through the 3D printing module in the CAD/CAM software.
Outlook
Additive manufacturing is being developed still further in current research projects. Laservorm’s CEO says, in summary, that hardware and software solutions for bionic lightweight construction structures are required, for example, for the future challenges posed by laser deposition welding. He says it is also necessary to improve the process monitoring methods accompanying manufacturing in order to satisfy the increasing demands for quality control and documentation. Decision-makers will find out at LASYS 2018 how laser systems are now helping to optimize production processes and will continue to do so in future. The accompanying program of LASYS 2018 will also provide visitors with the opportunity to enhance their knowledge of the current state of laser technology for material processing. For example, the Bavarian Laser Centre will hold a workshop on the topic of "Deposition and repair welding.” The workshop "Stuttgart Laser Marketplace“ will also be held again.
Optech Consulting will announce the latest data regarding the international market for lasers and laser systems with an eye on the future. Messe Stuttgart is expecting around 200 exhibitors at LASYS 2018. Visitors will be able to explore state-of-the-art laser systems, machines and processes, as well as services for laser material processing.