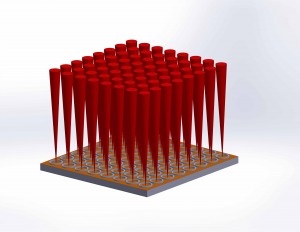
In laser beam profiling technologies, the standard of the industry is measuring one beam at a time. However, the laser diode market has recently increased in size as well as in new technology concepts. Many new applications such as gesture recognition, autonomous driving, high performing lasers, etc., are based on the concept of parallel emissions consisting of several lasers and emitting from one wafer. A good example is the new iPhone 10 where about 30,000 dots are created and projected toward the user's face, while back reflected information is used to reconstruct the 3D face features for recognition. Another example is the vertical surface emitting laser family VCSEL, which has rapidly become one of the world's most advanced technology because of its low power, good beam characteristics and the capability of building multiple laser sources on one wafer.
Users are interested in uniformity quality of the beams, their profile characteristics such as flat-top or Gaussian, their heat stability and high-power level output from single chips exceeding 1 kW/cm^2. In high-power applications, the VCSEL array is usually used with chillers and it's important to monitor stability of lasers as a function of chilling in order to avoid disoperation of the laser diodes. For all these applications, it's important to measure not only the total output power of the array, but also the relative emission levels and beam profiles of each VCSEL laser on the given chip. In this industry of multiple sources, one can find a single chip with one or two lasers, or densely packed with more than 30,000 lasers.
DOE (diffractive optical element) components, as offered by Holo/Or, have an increasingly central role in beam-splitting of high-power lasers for improved performance in Industry 4.0. One high power laser can be divided into multiple beams to perform material processing in parallel. The following image shows typical beam splitting of one beam into multiple beams.
Figure 1: High-power beam splitting for brazing applications.
Figure 2: Beam splitting into 16 sub-beams. Courtesy of Holo/Or
Figure 3: Picture of typical 2D high power VCSEL array. Courtesy of Finisar Corporation
As for VCSEL, the technology allows to pack multiple lasers on a single chip. In this case, VCSELs output is linearly scalable by size. Each one of the lasers is independent and identical to each other. The more lasers on a chip, the more power it puts out. Connecting them all to a single power source causes them all to emit in parallel. Different wiring into zones makes it possible to emit in different patterns. However, side-effects such as heating, geometrical inaccuracies and irregularities will cause the various lasers to emit at different power and different divergence. Carefully designed beam profilers as offered will analyze sources in parallel and compare outputs in the near and far field instantaneously.
The various applications pose a measurement challenge to provide an agile and accurate beam-measuring technology capable of measuring multiple beams from a few to thousands in parallel. The measurements need to provide profiling information and relative inter-relations between the beams. Moreover, those measurements should be performed over wide power levels and wavelengths.
Measurements made easy
To meet the challenge, a high-resolution beam profiler (2.4 megaPixel, 11x7 mm in size) has been developed for analyzing the profile of the parallel lasers in real-time. The design permits high resolution beam profiling with a flexible choice of the number of lasers to be tested according to the examined chip. Using a fast laser beam profiler, this enabling technology is also suitable for mass production and in-process inspection. Special attenuators and beam samplers will allow measurement of various power levels, including high power lasers.
As shown in Figures 3 & 4, a typical one-die laser array should be examined and compared for various parameters as explained above. Moreover, far-field and near-field should be examined – this could be achieved by attaching a focusing lens to a beam profiler and performing measurements when the lens is in its infinity position, and focusing on the die's surface. Alternatively, for beams that are not fast expanding, by moving the beam profiler literally near and far from the die. Typical measurements as performed by a beam profiler based on a high-resolution camera and divided into sections according to user division or by automatic best division as provided by software.
Figure 4: One die multiple laser array.
This setup behaves like multiple independent beam profilers, each analyzing one beam wherein all beams are analyzed in parallel and typical results such as: distance between beams, relative brightness, profiles, and long-time stability are collected and conveniently displayed for further analysis.
Figure 5: Multiple real beams displayed in parallel, including pop-up windows showing results for each beam. Courtesy of Duma Optronic
As shown in Figure 5, beside the real-time relative brightness of each beam, the user can open or close a Results window clearly numerated, for detailed information of each virtual beam profiler. Typical information includes beam profile size at three levels, position, and more information is displayed in a non-graphical way as a real-time file.
For vivid and clear information, a 3D reconstruction for all dies' beams as recorded by the virtual multiple beam profilers is displayed, showing the beams and division on the camera surface.
Figure 6: 3D multiple beam reconstruction. Courtesy of Duma Optronics
For far field divergence calculation, the beam profiler should include a non-distorting lens system which is positioned exactly one focal length away from the detector's surface.In this case, for small beams, the beam divergence of each laser is given by:
For high power applications, direct measurements will be impossible, thus a reflective beam sampler should be used in such a way that most of the power will be directed toward a beam dump and only a fraction should be directed toward the measuring instrument. In the following drawing, a typical device is shown. If extremely high power is involved, then the beam sampler itself should be cooled as shown in Figure 7, the cooling is achieved by blowing compressed air onto the prismatic beam sampler. Furthermore, this pressurized cooling will provide a protective curtain to the beam sampler and actively remove particles, preventing build-up on the surface. This will allow measurements of high-power laser beams in parallel.
Figure 7: A BeamOn U3 High Power beam profiler, including high power beam sampling with built-in inlet pressurized air for cooling.
High quality and resolution beam profilers have the potential to assist the newly emerging market for testing multiple laser source or laser beams working in parallel. Such applications as lidar, material processing, medical applications and more will benefit for in-parallel beam analysis to deliver better and more accurate devices. Aside from higher quality, those devices could substantially reduce testing tome and GONO-GO decisions for higher throughput of laser systems.
Figure 8: Specifications at a glance.
Written by Oren Aharon, CTO, Duma Optronics