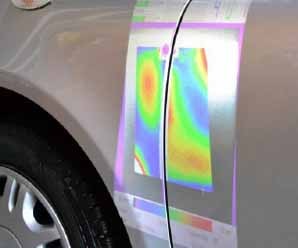
Over the past two decades, general purpose scanners have been widely deployed in various industries to capture 3D images of shapes and surfaces of objects that can then be analyzed for quality control, reverse engineering and fit and finish purposes.
The approach, however, is not without its drawbacks. Due to the general purpose nature of the scanners themselves, engineering companies must often invest valuable resources to program and configure the systems to enable them to analyze the 3D data captured by the scanners and to train their personnel to interpret the results generated from the analysis.
Recognizing the onerous burden those tasks place on customer companies, a three year old Denver (US) and Konstanz (Germany) based company has taken a completely different approach to scanner design. Rather than develop a single general purpose system that can be used in a variety of disparate applications, 8-tree has created a number of application specific scanners that deliver the same or better performance as legacy systems, but do so while relieving a user from the complex tasks of configuring and programming scanner systems and subsequently analyzing and interpreting the mountain of data captured by them.
8-tree has developed three application specific scanners that can be deployed to accurately measure the dimensions of dents, fasteners and gaps. From right to left: dentCHECK, fastCHECK and gapCHECK.
Currently, the company has three such fully self-contained portable battery-powered systems that produce immediate "go/no-go" results of surface metrology measurements and display them directly on the surfaces under inspection. More specifically, the three existing 8tree products -- dentCHECK, fastCHECK and the gapCHECK systems -- can be deployed to accurately measure the dimensions of dents, fasteners and panel alignment.
System design
All three instruments share a similar hardware architecture. They all include a Texas Instruments MEMS-based projector that projects patterns of structured-light successively on the surface of a target. Features, contours, and textures of the target surface distort each of the projected patterns, and the distorted images are then captured by a variety of different Allied Vision Manta cameras housed within the units.
Images from the camera are transferred to on-board memory and processed by software running on a CPU that extracts measurement data from the detected distortions, and creates a new image that highlights the results of the analysis. The scanner then warps the image to compensate for distortions from the surface after which it is projected back onto the surface under inspection. This all happens within 1 to 2 seconds so that the user experiences almost immediate feedback.
According to Arun Chhabra, a co-founder and CEO of 8tree, the software analysis performed by each of the systems has been optimized to solve the specific peculiarities related to measuring surface deformation, fastener flushness and panel alignment. Although all three of the scanners inspect surfaces, the unique nature of each of the inspection tasks mandated the use of software dedicated to each one, and is a key differentiating factor that enables each of the scanners to deliver results at high speed.
Metrology data from the scanners can be presented to a user in many data formats, of which three are most commonly used by customers. The first is the actual scanned image of the surface under inspection with the annotated results mapped onto it. Related to that is a corresponding XML file that highlights each of the points of interest that has been measured on the surface. For each point of interest, there is a dedicated line item in the XML file that details the time at which the measurement was taken, the x, y and z coordinates of the surface, angular orientation and a variety of other measurement information.
For archiving or internal engineering purposes, an STL file of the data captured by the scanner is also available. Should users then choose to duplicate the analysis performed by the scanner to validate the results from it, they can do so using third party analysis software.
Gage R&R Analysis
Through working closely with early adopters of the system, 8tree has been able to perform detailed a Gage Repeatability and Reproducibility (Gage R&R) analysis to assess the performance of the scanners. Gage R&R is a statistical tool that measures the amount of variation in the measurement system arising from the measurement device and the people taking the measurement.
According to 8tree’s CEO Mr. Chhabra, the company has demonstrated that the Gage R&R analysis results sit well below the required quality benchmark. Gage R& R measures the consistency of results of a system based on three degrees of ranking -- if the results of the Gage R& R are greater than 30%, the system is not suitable for use. If the results lie between 10 to 30% then it is considered acceptable. If it is less than 10 %it is considered a benchmark figure.
Automotive and Aerospace
At the present time, 8tree products find homes in both automotive and aerospace inspection applications. In the automotive industry, the dentCHECK system, for example, can be used to enable manufacturers to analyze the surface uniformity of bodies of automobiles, while viewing the results in real-time directly on the surface of the vehicle (Figure 2a).
Figure 2a: The dentCHECK system can be used by manufacturers to analyze the surface uniformity of bodies of automobiles, while viewing the results in real-time directly on the surface of the vehicle.
Similarly, the gapCHECK scanner can be deployed to measure the gaps and flushness of closure panels on a vehicle body (Figure 2b).
Figure 2b: The gapCHECK scanner can be deployed to measure the gaps and flushness of closure panels on a vehicle body.
In the aerospace industry, where keeping fasteners flush is critically important for maintaining long-term structural safety, the fastCHECK scanner is deployed to deliver fastener-flushness results instantly to a user (Figure 2c).
The dentCHECK scanner, on the other hand, is being adopted to inspect and to quantify any damage on the body of an aircraft that may have been caused by bird-strikes, food-service trucks, jet-bridges and luggage cars. Until today, assessing such damage has been a labor intensive task done by measuring many individual points with a handheld dial gauge.
.
Figure 2c: In the aerospace industry, where keeping fasteners flush is critically important for maintaining long-term structural safety, the fastCHECK scanner can be deployed to deliver fastener-flushness results instantly to a user.
Unlike general purpose scanners, of course, 8tree's application specific scanners do not require programming, and users no longer need to spend hours analyzing and then learning how to interpret the 3D data acquired by their scanners. Instead, 8tree products are immediately ready to use out-of-the-box and deliver instant analysis. The systems can deliver "go/no-go" results projected directly on the surface of the objects they are inspecting in less than two seconds.
As for future plans, Mr. Chhabra says that 8tree continues to carefully assess other areas of industry that might benefit from such application specific scanners. He says that although the current product line up enjoys a similar hardware architecture, if the company were to identify a compelling market opportunity where a different combination of hardware and associated software might be required, then 8tree's foundational architecture is both flexible and scalable, allowing the company to react quickly to emerging market demands for new measurement application.
Written by Dave Wilson, Senior Editor, Novus Light Technologies Today