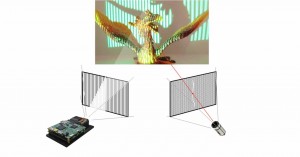
3D representation of real-world objects is increasing in demand as many new technologies emerge. Machine vision and robotics, in particular, benefit from accurate and adaptive 3D capture capabilities. Other applications for 3D scanning include biometrics, security, industrial inspection, quality control, medical, dental and prototyping.
Three-dimensional (3D) scanning is the extraction of an object's surface and physical measurements into a digital representation. The data is acquired as a point cloud consisting of X, Y and Z coordinates representing the external surface of an object. Analysis of a 3D scan can determine the surface area, volume, topology, shape and feature dimensions of the scanned object.
A 3D scanner requires a probe to determine the distance to each point on the surface of an object. In principle, the probe can be a tactile (physical contact) probe. However, many applications require contactless measurement. Optical techniques using only light to probe the object of interest offer solutions to this problem. One method utilizes at least two cameras to provide stereoscopic vision techniques, which is often computationally demanding and sensitive to ambient light conditions. Another method utilizes structured illumination patterns requiring only a projector (to generate the light patterns) and a single camera, plus algorithms requiring only moderate computational power.
Structured light
Structured light is an optical method of 3D scanning which projects a set of mathematically constructed light patterns which sequentially illuminate the object being measured. A camera, at a known distance from the projector, synchronously captures a set of images of the illuminated object. Relative to a flat reference surface used for calibration, the patterns seen by the camera are distorted by the topography of the scanned object. The principle of geometric triangulation makes it possible to calculate the XYZ coordinates of each point on the surface of the scanned object (see the graphic above). The resulting point cloud data is then used for computational construction of a detailed 3D model of the scanned object’s surface.
Programmable pattern structured light
Programmable pattern scanners use laser or LED illumination with a digital spatial light modulator (SLM) to project a series of patterns on the surface of the object. A programmable structured light scanner can obtain greater accuracy through the use of multiple patterns as well as the ability to adapt the patterns in response to ambient light conditions, the object’s surface, and the object’s optical reflection characteristics.
Since programmable pattern structured light requires the display of multiple patterns, a spatial light modulator is a key component of such a scanner. Several spatial light modulation technologies exist in the market including Texas Instruments DLP technology, specifically the DLP6500 and DLP9000 chipsets.
Different structured light scanning algorithms require the ability of the SLM to produce either or both binary and grayscale patterns. High contrast patterns help to maximize accuracy and operational robustness when dealing with varying object reflectance and ambient lighting conditions. System design puts a premium on optical throughput and energy efficiency due to size, cooling and battery requirements.
Many techniques exist to optimize the 3D structured light patterns. One particularly effective approach is an adaptive pattern set. Algorithms determine the best combination of patterns and wavelengths to improve the resolution of the scanned object. Varying colors (wavelengths of light) can be selected depending on an object’s colors. Adaptive patterns improve the ability to scan objects with complex surface textures or discontinuities.
Design considerations
There are several important design considerations for programmable structured light solutions. The size and distance of the measured object as well as the desired spatial accuracy of the 3D measurement determine the performance characteristics required of the spatial light modulator and image capture cameras. SLM resolution (number of pixels) and scan field size (pixels/mm) determine the achievable accuracy. Cameras must be of adequate resolution, usually at least four times the pixel density of the SLM, due to sampling theory.
Any object movement during a scan blurs the data and reduces measurement accuracy. The faster the expected motion of the object, the quicker a complete scan must be made in order to achieve a desired level of 3D accuracy. Faster scans require faster spatial light modulators and cameras with higher frame capture rates, and may also benefit from brighter pattern illumination. Pattern rates from a few per second up to several hundred per second may be necessary in various 3D measurement systems.
3D scanning evolves
Machine and robotic vision and other 3D applications are enabling intelligent machines to achieve ever greater capabilities. 3D scanning has evolved with the development of new technologies and algorithms. As the processing and sensor capabilities increase while their costs decrease, these new technologies provide several options to the end user. Active, non-contact 3D scanning systems that use structured light offer distinct advantages to the user but must be evaluated based on a specific application need.
Written by Pedro Gelabert, Ph.D. and V. Pascal Nelson, Texas Instruments Incorporated