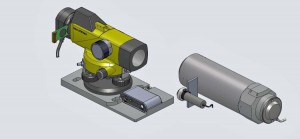
Modern technologies are characterized by extreme complexity, and by the fact that one system is built by fusing several technologies together. A typical system could involve such technologies as accurate mechanics, lasers, vision systems, computers, electronics and packaging. The alignment between lasers, vision systems, optics and state of the art mechanics becomes critical for high-quality products that are produced by these systems.
Alignment is achieved by new techniques involving special state-of-the-art electronic autocollimator and new laser straightness measurements. The autocollimator device comprises of two instruments fused into a single unit, one being an electronic autocollimator and the second is a laser beam profiling system. This combination with some additional optics will be very useful for bore sighting application between an optical sight and laser systems.
Another critical issue is using laser in specific industrial alignment applications. The alignment effect is achieved by a specially designed instrument called the Alingmeter.
The laser autocollimator
Autocollimators are high-precision instruments for measurement of angular reflections. It projects a reticule pattern as a collimated beam to infinity by a telescopic lens. A mirror positioned in its optical propagation path will back reflect the beam into the autocollimators' aperture.
The reflected beam generates the auto collimation image that is observed by the user’s eye via an eyepiece. The autocollimation effect and name is derived from the fact that the same telescopic lens is used to project the image and collect its back reflection from a mirror element.
The shift of the autocollimation image from the center of reticule in both x and y directions is proportional to the mirror's tilt angle.
Because of the laws of reflection that double the angle of the back reflected beams, autocollimators are calibrated to show half the angle of the total incoming beam deviation. Thus when the mirror is perpendicular to the optical axis, the beam is reflected into itself and the displayed back reflected image will be exactly centered.
Working principle of an Autocollimator
Applications are roughly divided into two fields - optical and mechanical engineering. Several typical examples will demonstrate the main area of application and usefulness of this century old technology.
Most common applications in the optical field are:
- Testing of Parallelism of optical surfaces of optical wedge or windows
- Testing of prismatic elements
- Relative Measurement of Angular Error of Prisms
- Testing of Camera Objectives
- Radius Measurement of Concave and concave Spherical Surfaces
- Measurement of the Centration Error
- Applications in Mechanical Engineering:
- Measurement of Parallelism of Two Surfaces
- Measurement of Perpendicularity of Two Parallel Setting of Rolls
- Pitch and Yaw Measurement of Slides
- Measurement of Roll-Angle
- Straightness Measurement
- Flatness Measurement
Development in the laser field created a need for accurate alignment of a laser beam to its mechanical datum. Many other applications require alignment of the laser beam to its optical cavity or to other optical elements. Lasers are frequently found in similar areas as autocollimator application such as straightness measurements, machine alignment and wide-bed printers. Alignment of lasers to an optical or mechanical datum, while adjusting the laser divergence angle along the optical axis will greatly improve the optical performance of laser systems
The new apparatus is based on a state-of-the-art autocollimator combined with an imaging laser beam profiler.
The technology presented allows fusing data of alignment autocollimator with incoming laser beam information to increase the overall performance and possible applications. Laser beam deviation is compared with the autocollimators’ center axis and allows intricate alignment of lasers to optical or mechanical datum planes.
Bore sighting between a laser and other optical sights
A special interest is the alignment of two or more line of sights, one from a laser source and the second from one or more cameras with a significant parallax distance between the devices. Originally bore sighting is defined as the adjustments made to an optical scope to be aligned to the firearm barrel. A device called a bore-sighter or collimator is used to accomplish this. It consists of an optical head and a bore-diameter adaptor which is inserted into the muzzle of the rifle. By observing an external target, once through the bores' optical head and secondly through the weapon scope, an adjustment could be made such that both will point at the same target.
A remote external target is necessary in order to perform the line of sights alignment.
Frequently this concept is borrowed to align multiple lines of sight, although there is no iron weapon involved but, laser to sights, or sight to sight. All these applications have a common trait with the original application and that is that a remote external target is necessary in order to perform the line of sights alignment.
The newly invented Laser Analyzing Autocollimator (LAA) will allow bore sighting between multiple lines of sights to a laser, or laser designator or some other bore sighting application.
This setup allows alignment of lasers to its mechanical axis or external sights without the need of an external target with high accuracy and reliability.
Two enabling technologies for performing the laser& sights bore sighting are required, one is using an accurate periscope to achieve the required offset to neutralize the parallax between the laser and sights, and second the LAA instrument.
.
Periscope working principle
Recent advances in diamond-turning technologies offer the capability of manufacturing a periscope from a single metal piece with very high accuracies.
One piece periscope
The next two schematic drawings outline two applications: one of alignment between laser and optical sight and the second between the laser, its mechanical axis and external sight.
The bore sighting procedure is performed in two stages. In the first stage the periscope is deployed to cancel the parallax between the laser and the LAA. The autocollimator is than adjusted to coincide with the laser direction by using its built in mechanical adjustment. The adjustment is performed in both axis’s pitch and yaw.
Than the periscope is rotated 180 degree to cancel the parallax between the sight and autocollimator. The built in autocollimators' cross is than projected to the sight which will be adjusted to coincide with the projected cross direction.
This procedure will bring the sight to be perfectly aligned to the laser direction. A small angular offset between the two can also can be easily achieved.
Because of this special set up, the effective autocollimator aperture for bore sighting applications will exceed 200mm, these effective aperture conversion is a function of the length of the periscope used.
First step, aligning of Autocollimator to the laser using the periscope
In a second application the basic requirement is to bring the laser and its sight to be aligned with a mechanical mounting interface.
In this application the LAA will be first aligned to a mirror surface representing the mechanical interface. Then the periscope will be mounted to cancel the parallax between the laser and the LAA, allowing adjustment of the laser to the Autocollimator and than in a similar way as previously explained adjust the sight to the LAA. This procedure will ensure perfect alignment between the mechanical interface to its optical means.
First step, aligning of Autocollimator to the mechanical reference using a mirror
In bore sighting applications, the final accuracy and feasibility is crucial. This new technology achieves better results in a shorter time and without the need of external targets, enabling various sensors and lasers to have their line of sight perfectly aligned. So far the system works well with lasers and sights from UV to communication and eye safe lasers of 1550nm although this technology could be further expended to longer wavelengths.
New approaches for better assembly
The development and implementation of state-of-the-art measuring instrumentation that combine laser analyzing and traditional optics allow for a significant advancement in the area of target-less bore-sighting and accurate alignment. New approaches to alignment and lasers combined with diamond machining of intricate optical assemblies will lead to proper assembly of mechanics, lasers and optics.
Written by Oren Aharon Chief Technology Officer at Duma Optronics.