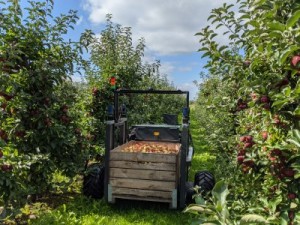
The Autonomous Orchard Assistant Altes Land (Aurora) is a small autonomous vehicle that can move independently around in the field, identify boxes of crops, know when they are full and pick them up and bring them to a specified location. Measurement and sensor specialist SIKO is working on the steering angle detection and positioning of the box holders.
The idea for the project was the brainchild of fruit farmer Johann Schröder from Jork in the region southwest of Hamburg, Germany. He went to Hochschule 21 for help in developing an autonomously operating vehicle of this sort. The project was launched in collaboration with the agricultural equipment manufacturer PWH, and the plan was to deliver a functioning prototype by January 2023 to demonstrate its practical feasibility.
The robot is currently capable of operating largely autonomously in an orchard, but work is still needed in making sure the robot can avoid collisions and detect the ground conditions, to avoid getting the wheels stuck in muddy ground, for example, or drifting off course into a ditch.
A development project of this sort always poses particular challenges, starting with coordination of the interests of various fruit farms. One of the challenges has been having adequate cell phone coverage so that the robot can receive GPS data and communicate with the operator.
SIKO has contributing its expertise to the planning phase and ultimately came up with two suitable rotary encoder types that support autonomous functions.
“We were pleasantly surprised by the willingness of SIKO to support future-oriented projects and how committed they were in offering their advice,” said Alexander Kammann, research assistant at hochschule 21. “In the beginning, we were not even sure what requirements we actually had of the sensors. We worked all this out and defined it together.”
Robust rotary encoder
The sensors used in this application must be extremely robust and resilient in the face of tough outdoor conditions (mud, dust, rain, strong sunshine, and unevenness in the ground). Components in the Pure.Mobile range of sensor modules from SIKO are particularly suitable for use in mobile machines under harsh environmental conditions.
A double wheel is fitted to the back of the vehicle, which can rotate and thus control the steering. The steering angle is recorded, processed, and sent to the controller by the WV5800M magnetic rotary encoder. This is a multiturn rotary encoder by means of which even multiple rotations can be detected absolutely. If the power supply is interrupted, because the batteries are flat for example, the steering angle previously set is still present.
Without an absolute encoder, this would incorrectly be set as the zero degrees angle when the vehicle is started up again. The high precision and reliability of the rotary encoder also impressed the team, meaning that the vehicle always adjusts its steering angle so that it keeps to its defined without deviation. In order to increase safety in interaction with the people working in the orchardr, the WV58MR safety variant of the rotary encoder with redundant position detection will be used for future vehicles to reliably prevent failures.
In the development phase, the focus was initially on technical feasibility, so that the rotary encoder without the safety standard was adequate. The advantage of the SIKO models: the two rotary encoders are identical in design, so that no mechanical adjustments need to be made to the application when swapping them. A CANopen interface was also required for the steering angle detection system so that as many standard electronic components as possible can be used, replaced quickly and integrated into the system bus.
Position sensors
The second SIKO rotary encoder, the AH25S, is even smaller and more compact. It is a single turn rotary encoder that monitors the position of the box holders, the so-called flippers. The filled fruit box is picked up at four points by one flipper for each. When the robot moves over the box and the spring-loaded holders touch it, the flippers swivel to the side, then open automatically and are then located under the four corners of the box for pick-up.
To transport the box safely, the position of each flipper must be known. The space is very restricted, so a miniature rotary encoder was required that could be used directly without a special holder. An analog encoder is adequate here, as the data is less critical than that provided by the steering angle sensor.
One the challenges are overcome, the Aurora may be used with a balanced cost-benefit ratio in numerous orchards. In order to offer farms genuine added value, the intention is to use it for other maintenance work, as well, such as mulching and mowing or as support for planting new trees. Effective use virtually throughout the year is therefore possible and is not just restricted to harvest time.
The project is funded through the ZIM funding program of the Federal Ministry for Economics.