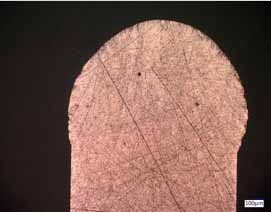
Welding is one of the industrial applications made much more efficient with the laser. Lasers transfer energy from the source to the workpiece without the need for physical contact, so the geometry of the joints is much more flexible than with alternative methods. But many important industrial metals — such as copper, aluminum, gold, and stainless steel — don’t absorb much of the infrared wavelengths output from traditional industrial lasers.
In contrast, these materials absorb much more energy at blue wavelengths. Until 2017, that was just an interesting fact, then Nuburu introduced the AO-150, the first blue laser capable of delivering the power and brightness required for industrial applications. In 2019 the AO-500 was released, opening up an entirely new range of applications — enabled by both the 500 watts of output power at 450 nm and (just as importantly) by the beam-parameter-product (BPP) of better than 30 mm-mrad.
New designs call for new fabrication technology
The unique capabilities of the high-brightness blue laser enable new applications. Consider, for example, the push for new compact electric motor design, motivated in large part by the growing production of electric vehicles. An efficient vehicle begins with an efficient and lightweight motor. The “bar winding” design uses individual rectangular-profile wires in the stator, and is both thermally and electrically more efficient than traditional wire-wound motors.
The problem is, though, that the bar-wound design requires that the ends of each wire in the stator be joined to one another. Specially designed wire winding machines can wrap one to the other, but that requires extra (non-functional) length to be added to each bar wire. Traditional joining methods require a modified welding head in proximity or in contact with the joint, which takes more space. That also reduces the flexibility, because if the motor design is tweaked then the weld head must be redesigned. Laser welding solves those problems, but traditional infrared lasers produce low quality joints — with defects that both mechanically weaken and increase the electrical resistivity of the joint.
The high absorption and brightness of the blue laser solves all those problems. The joints are high quality and compact, and the lack of physical contact between the laser and the workpiece means the laser parameters can be simply adjusted to match any part geometry. For example, video 1 shows a slow motion image of a hairpin weld, where two adjacent wires are welded. Figure 1 is a cross-section of a completed hairpin, showing the lack of defects characteristic of blue laser welds.
Video 1. This video of a hairpin weld in action demonstrates the smooth transition into the melt, with no spatter.
These same advantages extend to such applications as battery fabrication and e-mobility device manufacturing. The blue laser is so flexible that a simple adjustment of process parameters suffices to transition from, for example, welding stacks of thin battery foils, then thicker tabs, busbars, the connections for battery pack integration — essentially every copper connection in an electric vehicle. The blue laser also can address such complicated situations as the joining of dissimilar metals. Alternative methods run into trouble when they deliver more energy to one metal than the other, which leads to the formation of random-composition alloys throughout the joint, so-called “intermetallics.” Those intermetallics lead to mechanical weakness and electrical resistivity variations — defects in the joint.
As laser development continues to offer even higher brightness, and higher energy density, the range of materials and thicknesses accessible to this powerful materials processing method will continue to grow.
Absorption matters
To initiate a weld a certain amount of thermal energy must be delivered to a metal. For example, as shown in Figure 2, copper absorbs only about 5 percent of the energy from ~1 µm incident infrared radiation. The real problem, though, is that the melt pool thus created absorbs more infrared energy than does the raw material. So once the weld is initiated, it suddenly is getting many times more energy than it needs to sustain the weld. That extra energy creates miniature explosions within the melt pool, “bubbles” that eject material out of the weld and leave voids behind. Spatter and voids degrade both the mechanical and electronic properties of the joint.
Figure 2. The fundamental physical advantage of blue light over other wavelengths comes from absorption. Copper, for example, absorbs ~13 times more blue light than it absorbs of 1 µm radiation.
The high absorption of blue laser energy eliminates all those issues. The raw metal and the melt pool have almost the same absorption, so the process is always under control (something which cannot be said for other visible wavelengths). As shown in videos 2 and 3, the 1 kW blue laser produces defect-free welds under a variety of conditions. The fundamental physics leads to unmatched performance in a variety of metal processing applications.
Video 2. This video of a 1 kW blue laser shows the complete lack of spatter during keyhole welding of 1 mm-thick copper at 1.5 m per minute.
Video 3. The 1 kW blue laser also shows no spatter when performing conduction-mode welding of 254 µm-thick copper at 17.5 m per minute.
Some bright ideas
Good materials processing performance requires high energy density, and that comes down to brightness.
Brightness is a measure of the energy and “tightness” of both the laser spot and the laser divergence. Imagine two equally powerful sources both coupled through optical fibers of the same numerical aperture, but different diameters. The smaller diameter fiber leads to a system BPP of 30 mm-mrad, as opposed to the 60 mm-mrad of the larger diameter fiber system. That factor of 2 in BPP leads to a factor of 4 improvement in energy density for the smaller diameter fiber.
This is important because the speed and depth of welding, for example, is a function of brightness. It’s relatively easy, to convert a high-brightness source to a lower brightness source. But it’s impossible to go the other way: to convert a low-brightness source to have high-brightness. So the initial brightness of the laser source is critical. The increased energy density, as shown in Figure 3, leads directly to either increased weld depth, increased weld speed, or a combination of both.
Figure 3. Higher brightness leads to higher energy density, which translates directly into speed and/or penetration depth improvements. The chip-based design has intrinsically higher brightness than, for example, a bar-based system.
One more thing to know about brightness. It doesn’t do you any good to have a brightness far higher than your needs. The ideal laser will have a brightness higher than required for a given application, because it can always be reduced. But you wouldn’t want the brightness orders of magnitude higher than the application needs, because that just adds cost and complexity to the system.
Image at top: This cross-section of a hairpin weld illustrates the lack of defects when joining two adjacent wire ends.
Written by Jean-Michel Pelaprat, co-founder; Matthew Finuf, applications manager; Robert Fritz, applications engineer; and Mark Zediker, CEO and co-founder of Nuburu