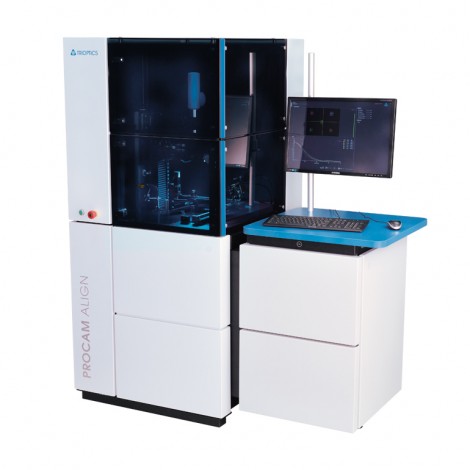
The short pulse durations and high peak powers of ultrafast lasers make them beneficial for laser materials processing, multiphoton microscopy, and a wide range of other applications, but these systems are particularly sensitive to thermal lensing.1 Heat can build up and change the geometry of optical components in the laser, destabilizing the system and potentially even preventing it from generating ultrafast pulses. Thankfully, new low-thermal lensing, highly-dispersive mirror technology can minimize thermal lensing while still maintaining high reflectivities and dispersion control.
Image above: Highly-dispersive mirrors with negligible thermal lensing allow ultrafast laser systems to achieve high powers without becoming destabilized by heat buildup and thermal lensing
What is thermal lensing?
Thermal lensing is a phenomenon where heat buildup in laser gain media reduces the performance of solid-state lasers, particularly when they are operating at high powers. The density of the gain medium may decrease as temperature increases, causing components closer to the beam axis to become more curved than areas further away from the beam. This curvature gradient can misalign the laser's resonance cavity, generate unwanted laser mode profiles, and lead to drifts in the laser's beam pointing. These effects become even more of an issue at higher repetition rates. A portion of these effects can be controlled through careful design of the resonator, but there are not many steps that can be taken to change thermal behavior inherent to the gain medium.2
Thermal expansion can also induce stress and warp intracavity optics. If thermal lensing is severe enough to change the radius of curvature of the mirrors making up the resonance cavity, the laser may not be able to achieve mode-locking and generate ultrafast pulses. This would essentially render the laser useless. Thankfully, selecting the proper intracavity optics can prevent thermal lensing and maintain desired performance.
Beat the heat with low thermal lensing mirrors
Pulse compression optics such as highly-dispersive mirrors are critical for compensating for the positive group delay dispersion (GDD) inherent to most optical media. Left unchecked, this would elongate pulse durations, reduce peak powers, and reduce system performance. Pulse compression optics have a negative GDD that balances out this positive dispersion, resulting in short laser pulses. Highly-dispersive mirrors feature several advantages over other pulse compressing optics like gratings and prisms including negative GDDs with a high magnitude, large bandwidth, low levels of loss, and compact size.3 However, thermal lensing can warp these mirrors as described earlier.
Advancements in ultrafast coating technology have thankfully resulted in novel highly-dispersive mirrors with negligible thermal lensing, allowing ultrafast laser systems to reach higher powers without thermal lensing destabilizing the system (Figure 1). They still achieve a broad bandwidth and highly-negative GDD, but they also have minimized thermal lensing thanks to unique coating designs and precise control of the coating deposition process. This allows for them to be used in high-power ultrafast systems without suffering from thermal lensing. The coatings can be designed to work with a wide variety of different laser types such as Er:YAG, Yb:YAG, holmium, and thulium laser sources.
Verifying Thermal Performance
To verify whether these mirrors really do reduce thermal lensing, an infrared camera (FLIR SC305) measured temperature fluctuations while they were they were used to reflect a Yb:YAG thin disk laser operating at continuous wave (CW) mode. Their performance was compared with other highly-dispersive mirrors without the coatings designed to minimize thermal effects. Figure 2 shows a temperature change of 57K of a dispersive mirror without the new, low-thermal lensing coating. This mirror features reflectivity >99.8% and a GDD of -3000 fs2 for wavelengths from 1010 and 1050nm. This increase in temperature led to deterioration of the laser mode and oscillator stability. Figures 3 and 4 show the measured temperature for two highly-dispersive mirrors with the novel reduced thermal lensing coatings. They featured GDD values of -1000 fs2 and -3000 fs2, respectively, and slightly lower reflectivities of >99.5% over a comparable waveband. They exhibited temperature changes of 10K and 20K, which is significantly lower than that of the first mirror. No detectable changes in laser mode and oscillator stability were observed, so system performance was unaffected by thermal lensing. This allowed the system to maintain desired performance.
Figure 2: The mirror without the coating optimized for thermal lensing exhibited a 57K temperature change during the test, which reduced system performance
Figure 3: The first low-thermal lensing mirror with a GDD of -1,000 fs2 exhibited a 10K temperature change throughout the test, which did not lead to any detectable performance reduction due to thermal lensing
Figure 4: The second low-thermal lensing mirror with a GDD of -3,000 fs2 exhibited a 20K temperature change throughout the test, which also did not lead to any detectable performance reduction due to thermal lensing even though it was double that of the other low-thermal lensing mirror
Should I Use a low-thermal lensing ultrafast mirror?
There is a small tradeoff in reflectivity when using a highly-dispersive mirror optimized for thermal lensing, as they achieve reflectivities around >99.5% compared to 99.8% for other highly-dispersive mirrors. However, this tradeoff could be very worth it in high-power systems where thermal lensing threatens to destabilize the laser and potentially prevent mode-locking. This allows these systems to push to limits of what peak powers are achievable.
Negligible thermal lensing coatings are not required for all ultrafast applications. Ti:sapphire lasers usually do not reach powers high enough for significant thermal lensing to be an issue. Fiber lasers do not use solid-state resonance cavities, so this technology is also not needed in these systems. Other types of highly-dispersive mirrors are sufficient and can allow for slightly higher throughput because of their higher reflectivities. However, high-power, solid-state ultrafast laser systems could benefit from reducing thermal lensing. High-power Er:YAG, Yb:YAG, holmium, and thulium laser sources can take advantage of low-thermal lensing coating technology to beat the heat and maintain system stability and performance.
Written by Cory Boone, Technical Marketing Manager, and Vladimir Pervak, Head of Optical Coatings at UltraFast Innovations, Edmund Optics
References:
- Backus, S.; Durfee III C. G.; Murane, M. M.; Kapteyn, H. C. (1998). High power ultrafast lasers. Review of Scientific Instruments, 69(1207), https://doi.org/10.1063/1.1148795
- Vanherzeele, H. (1988). Thermal lensing measurement and compensation in a continuous-wave mode-locked Nd:YLF laser. Optics Letters, 13(5), pp. 369-371, https://doi.org/10.1364/OL.13.000369
- Pervak, V., et al. (2008). High-Dispersive Mirrors for Femtosecond Lasers. Optics Express, 16(14), pp. 10220–10233, https://doi.org/10.1364/OE.16.010220