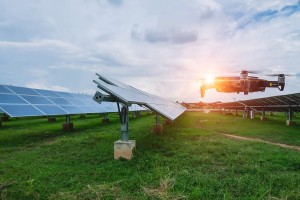
Imaging lenses are critically important components for systems deployed in many environments such as manufacturing and factory automation, autonomous vehicles and robotics, and industrial inspection. Standard imaging lenses may not be able to function in or withstand the extreme environmental factors such as temperature, moisture, vibration, or shock. However, standard imaging lenses can be modified in a few key ways and made to withstand one or more extreme environmental conditions. Imaging lenses are typically ruggedized in a variety of ways, according to one of three different options: industrial, ingress protected, and stability ruggedization.
What is industrial ruggedization?
Industrial ruggedized lenses are designed to survive in environments that may have vibration or shock and are manufactured to not become damaged or to shift in focus or f-number during use. To achieve this, many movable mechanical features are removed from the lens design and replaced with static components, reducing flexibility but making the assembly easier to lock down. Standard imaging lenses typically feature an adjustable iris composed of thin leaves and ball detents which are used for adjusting the aperture size of the lens and therefore the f-number. Industrial ruggedized lenses remove this adjustable iris and replace it with a fixed aperture stop, eliminating parts that would be more susceptible to damage in harsh conditions.
Figure 1: A standard imaging lens (left) typically makes use of an adjustable iris, whereas an industrial ruggedized imaging lens (right) makes use of more simplified mechanics.
Industrial ruggedization is ideal for applications where an imaging system is to be set up once and then not changed afterwards. One additional advantage when reducing the number of complex movable components from the lens design is that static parts are usually less expensive than movable parts. Because of this, a significant cost savings is achieved at volume and passed along in the form of a mechanically simpler, more robust product. There are numerous applications for industrial ruggedized lenses including high-vibration production-line environments where the camera is quickly accelerated or decelerated, inspection systems where multiple similar camera systems are set up, and autonomous systems such as self-driving cars and warehouse sorting robots.
What is ingress protection?
Ingress protection ruggedization is applied to an imaging lens to seal it from external elements such as moisture or foreign debris. These lenses provide a cost-effective alternative to covering the entire imaging system with a protective enclosure. While using an enclosure does offer an additional external layer of protection from environmental factors, the use of an enclosure limits the user from being able to refocus the lens while it is operating within the application. Additionally, enclosures may be cost-prohibitive or unreasonable to manufacture for short focal length and wide field of view lens systems which often feature lenses with outer diameters larger than the characteristic size of the camera and a final optical element which may protrude out of the assembly.
Ingress protected lenses are typically industrially ruggedized as well, due to the susceptible nature of complex movable components to moisture and other factors. This type of ruggedization is often achieved by inserting O-rings or injecting RTV silicone into especially susceptible locations within the assembly (see in Figure 2).
Figure 2: An ingress protected ruggedized lens features an O-ring to seal out contaminants like dust, dirt, or moisture.
Lenses with this type of ruggedization are typically tested against specific IPX ratings. The first digit of the IP rating specifies the intrusion protection for a lens against solids (e.g. dust); this digit spans from zero, or “X,” to six where zero is no protection from solids at all and six is complete protection from dust (Table 1).
First Digit: Intrusion protection |
Definition |
0 or X |
No protection from solids. |
1 |
Protection from objects 50mm in diameter. |
2 |
Protection from objects not greater than 80mm and 12mm in diameter. |
3 |
Protection from objects 2.5mm or greater. |
4 |
Protection from objects 1mm in size. |
5 |
Partial protection from dust. |
6 |
Completely dust tight. |
Table 1: The second digit describes the protection from moisture and spans from zero to nine where zero, or “X,” offers no protection from moisture at all and nine is complete protection from moisture (Table 2).Table 1: The first digit of the IP rating describes the amount of protection an enclosure has from solids.
Second Digit: Moisture protection |
Definition |
0 or X |
No protection from moisture. |
1 |
Protection from falling droplets. |
2 |
Protection from water droplets deflected up to 15° from vertical. |
3 |
Protection from water sprayed up to 60° from vertical. |
4 |
Protected from water splashes from all directions, tested for a minimum of 10 minutes. |
5 |
Protection from low-pressure jets 6.3mm in diameter. |
6 |
Protection from direct pressure jets 12.5mm in diameter. |
7 |
Protection from full immersion for up to 30 minutes at a depth between 15cm and 1m. |
8 |
Protection from extended immersion under higher pressure from depths greater than 1m. |
9 |
Complete moisture protection. |
Table 2: The second digit of the IP rating describes the amount of protection an enclosure has from moisture.
Modern ingress protected lenses are rated IP67, IP68, or better. These ruggedized lenses excel in applications that may feature high amounts of humidity, sputter, dust, or small particles. These lenses are also typically used in applications where enclosing the full imaging lens and camera system is not an option.
What is stability ruggedization?
Stability ruggedization is a technique similar to industrial ruggedization that protects the lens assembly from damage. However, stability ruggedization also ensures that optical pointing stability and positioning are maintained after applied shock and vibration whereas industrial ruggedization does not. This means that industrial ruggedized lenses may map points on an object to different nearby pixels after applied vibration or shock.
In addition to having the moving iris and focus mechanism removed, stability ruggedized lenses are further stabilized by gluing down all internal lens elements and using a clamping lock to simplify the mechanics for focusing (Figure 3).
Figure 3: A stability ruggedized lens assembly is composed of optical elements that are all glued in place.
Lens elements sit within the inner bore of the barrel of an imaging lens assembly. Between the outer diameter of the lens and the inner diameter of the barrel is a small space, typically 50 microns or less. Though this space is of very small magnitude, decenters of only tens of microns are sufficient in affecting the quality of the pointing stability of the lens (Figure 4).
Figure 4: In an unperturbed system (a) with no shock or vibration, the object crosshairs are mapped to the image crosshair. In system that has been perturbed by shock or vibration (b), lenses within the barrel decenter causing a change in optical pointing stability and resulting in the object crosshairs becoming mapped to a different image location.
For a stability ruggedized lens, if an object point is in the center of the field of view and falls on the exact center pixel, it will always fall on this same pixel even when the lens has been heavily shocked or vibrated (Figure 5).
Figure 5: The pixel shift for a standard imaging lenses (a) experiencing 50G of shock is more than one pixel whereas the pixel shift for a stability ruggedized lens (b) under the same conditions is less than 1μm and much smaller than the size of pixel.
Stability Ruggedization is an important manufacturing technique used for imaging lenses which will be used in applications where the field of view must be calibrated and maintained. These types of applications require imaging lenses to make accurate measurements and include 3D stereo vision, machine vision sensing for robotics, and for the tracking of moving object locations. For these applications, the required value for the acceptable amount of optical pointing stability is oftentimes much smaller than that of a single pixel.
Reference: Hemmingway, H. (n.d.). IP Rated Enclosures Explained. Retrieved July 16, 2020, https://www.enclosurecompany.com/ip-ratings-explained.php
Written by Kyle Firestone, Technical Marketing Engineer, Edmund Optics