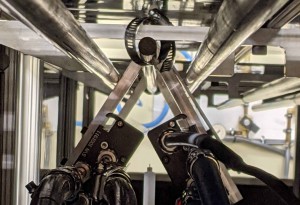
LED UV curing is state-of-the-art technology used in a wide range of industrial applications and is rapidly gaining traction for the measurable advantages it delivers, from superior quality and sustainability to improved productivity and worker safety. High-powered and versatile LED UV, conventional UV and IR systems are used by a vast range of industries to cure or dry inks, coatings, finishes, treatments, adhesives and polymers.
Hans Ulland, Executive Vice President of AMS Spectral UV, said that LED is way more scalable and usable from an industrial standpoint than any other source that's out in the marketplace.
“Some of our lamp heads allow us to be able to maintain the intensity needed for curing longer distances away, so although the light is 10 centimeters away from the lamp; it’s the same beam the whole way down.”
Applications served by LEDs
UV is used as a curing process to turn anything applied as a liquid to a solid or semi-solid. You can typically formulate liquid with photo initiators to react with the LED or conventional UV lamps to dry it faster.
One area that AMS Spectral UV has started to get involved in is with UV-curable powder coating, which is “pretty incredible”, Ulland said, “because instead of using giant gas dryers and ovens and infrared, you can just use a couple of UV lamps to accomplish the same thing.” The company also developed LED solutions for curing varnish for wood products and different types of coatings on all kinds of materials. The company also serves the electronics manufacturing industry with LED, which has been going on for years as one of our first uses for the technology.
Looking five to ten years down the road, Ulland said, “There's a lot of dreaming involved. The first thing that's important to note is everyone involved daily in the world wants to see UV-C become more effective immediately. UV-C is what kills biologicals – viruses, etc. -- which is important with what’s going on right now. What's commercially available generally isn't strong enough for us to use to knock out COVID-19, but that is on its way. So the ability to get into that disinfection stage is a really, really big deal for LED. Just imagine, you could have a cover for your door handle and it just zaps it every time somebody uses it. That's the kind of thing coming.”
“Those lower wavelengths in the low B and C category are on their way”, Ulland said, adding that, “They will get there, and we probably get 100 phone calls a month or so asking if we have it. We don't yet, but we will and believe me you'll read about it when we do. There's huge money funneled into that development of UV-C and that'll come hopefully shortly.”
The rest of the LED world is basically about reimagining everybody's chemistry so that they can get away from these kind of full-spectrum-use chemistries and move into something that's much more specific in the spectrum.
If you have the opportunity, for example, to cure exactly at 375 and that's the single best absorption rate for your product, you'll be able to use that with LED, where in the past you were only grabbing part of it with traditional UV. Ulland said they’re seeing regular UV disappearing over the next five to 10 years. The reason? Ulland said, “because, while it’s a great product, it has a lot of nightmares associated with it, both from both usability and environmental standpoints.”
When you see things in the news about disinfecting, and using UV light, that UV band is usually coming from conventional UV right now. There are also industrial processes that need those lower wavelengths and there are LED dies that can produce it, but they’re still a small fraction, 1% or less, of where the standard UVA 385, 394 or 395 nanometer dies are.
It’s not really viable to make a product that only lasts 100 hours and has a fraction of the output. So until LED catches up in those wavelengths eventually, we will still be used as a great technology for curing the areas we reach now.
Reducing VOCs in atmosphere
As LED technology gets better and stronger and more cost effective and the chemistry associated with it becomes more efficient, we'll have the opportunity to say goodbye to tremendous amounts of industrial volatile organic chemical (VOC) usage.
A good example might be something like powder coating that puts VOCs into the atmosphere on a regular basis. Those can go away because VOCs are not a required part of the LED curing process for any of these industrial applications. And that will be good for the environment, and especially for the health of all the workers around it.
Michael Derrick, Director of Operations at AMS Spectral UV noted that cost has been a huge driver of LEDs getting pushed further and further into industrial processes. “When we started off, they were incredibly expensive with some of the things we were doing just to make a powerful lamp.”
“We’re seeing now that we’re working with customers on their requirements and requoting similar systems that we quoted just two years ago and seeing massive reductions in cost due to the LED die technology catching up and coming down in price.”
And some of these lower wavelengths, like 365 especially, are really starting to become more cost effective nowadays. You can almost purchase LED for the same price or less than conventional systems, which is really going to keep pushing that technology forward into the market.
Written by Hans Ulland, Executive Vice President, and Michael Derrick, Director of Operations of AMS Spectral UV