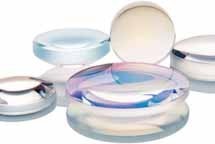
Today aspheric lenses are an integral part of modern technology, in the consumer market as well as in high-end research. Starting from small aspherical elements (Ø < 1.5mm) made of transparent plastic that are combined into a precise lens for smartphone cameras up to very large surfaces of about four meters in diameter as part of very large telescopes for astronomy.
However, we do not have to take a glance at these extremes to find aspheres. A broad spectrum of applications can be found in between. For a good deal of laser manufacturing processes, the beam is predominantly traveling without any field angle through the elements. Thus, spherical aberrations dominate the optical performance and correction requires multiple spherical lens elements.
For this, aspherical lenses can be a perfect solution. With their deviation from a spherical shape, spherical aberrations are completely corrected or do not even emerge. Decreased component size and increased transmission are immediate benefits, as one asphere can substitute two to four lens elements. Indeed, in laser material processing decreased absorption and internal back reflection foci, as often caused by multi-element objectives, are important properties to prevent.
What are spherical aberrations?
Spherical aberrations occur in systems with spherical surfaces. Spherical surfaces reflect or refract incident light rays stronger at margins than close to the optical axis. The result are widespread focus sports or blurred images as no distinct focus is formed.
Aspheric lenses made by Sill Optics GmbH & Co. KG in Germany
Production of aspheres: The not so complicated first steps
Countering the intuition right from the start: asphere production begins with grinding a spherical shape on the aspherical side – the so-called “best fit sphere”. It describes the closest spherical shape in comparison to the final aspherical form. Production efficiency is maximized by using a ring tool with a large working surface. As aspherical surfaces require point based production tools, removing this volume would take a lot more time. Additionally, oscillating movements of the ring tool take care of local surface errors laying the foundation for smooth surfaces.
Before creating the aspheric surface, first the opposite face is being made. It may be flat, but a spherical shape offers a significant advantage: it increases the tolerance for tilt of the asphere in the final setup a lot, making integration easy and reducing the effort for alignment. Production is based on the well-known procedure of grinding, lapping and polishing with large area ring and bowl tools. For further steps, a protective film preserves the finished spherical surface from damage.
Turning the attention back on the elementary part of the production: grinding the aspherical shape to a pre-grinded best-fit sphere is a rather quick step (< 10 min), despite the small tool surface. The grinding step is done with two increments of grain roughness by wheel tools, directly followed by a polishing step with CNC control. Five-axis machines based on point interaction tools offer the freedom to polish any rotationally symmetric surface form. The spatial extend of the tool is the only limitation there. The downside of point tools is the small interaction area that leads to long production periods and is a significant cost factor.
Illustration of the manufacturing sequence in aspheric lens manufacturing
Loop control between metrology and processing is the key for precision
Of course, having five high precision axes with a lot of freedom in their movement affects the intended deterministic process. Their uncertainty in movement leads to varying deviations from the specified target aspheric shape in the range of 0.5 to 1.0 micrometers Peak to Valley (P-V). Especially for laser applications, such accuracy is not good enough.
To correct these deviations, knowledge of the exact current surface shape is crucial. A tactile measurement, where a small sphere is traveling in straight and circular paths along the surface quantifies every difference to the target shape. Alternatively, this measurement can be done optically at short distances via white light interferometry.
Magnetorheological finishing (MRF) is the most commonly used technology for final correction of aspheres. Without the need for special tools, this technique is very flexible. The gathered information about the surface shape deviation is directly fed into the machine digitally. Based on a calibration of the impact of the magnetorheological fluid, the machine is able to calculate the optimal correction parameters and starts the finishing.
The MR fluid can be described as a two part slurry. A polishing solution as carrier and particles that are responsive to magnetic fields as a “smart” supplement. Based on the previous measurement results and a calibrated treatment area on the aspheric surface, an electromagnetic field is adjusted. The fluid particles build up chains along the magnetic field lines and greatly increase the fluid viscosity based on the field strength. The abrasion of the asphere substrate is therefore locally adjustable with high precision.
Resulting absolute surface from errors are below 0.3 micrometers P-V. To take this to a more imaginable dimension: would a standard aspheric surface (Ø50 mm) be of the size of a football field (90 m x 45 m), the maximum allowed height variation from the total flat would be about 360 micrometers. That is smaller than four sheets of copy paper. The first correction procedure does not always get to the required precision, thus measurement and finishing are repeated until specifications are fulfilled.
With finished surfaces, one of the last steps is centering. The outside diameter is oriented toward both surfaces via laser measurements and grinded down to the specified value. Optionally, optical anti-reflection coatings are applied.
Close look at the magnetorheological finishing process
Furthermore, several more technologies are accommodating asphere production, but were not mentioned in detail. For example, Fizeau interferometry can be of great benefit in metrology. By measuring the resulting wavefront of focusing or collimating aspheres, their high precision and fast testing time are unmatched. Similar to MRF correction, ion beam figuring can be consulted. The benefit lies in the freedom to process none-rotationally-symmetric aspheric surfaces.
Aspherical production is only as good as the measurement system
As compact solutions in many applications, aspheres offer many advantages over spherical lenses, outweighing the increased production effort. There are even applications areas where a spherical solution would not be possible, for example, beam shaping. However, the usability is nevertheless strongly driven by specific application demands. While aspheres already dominate various areas, they will not replace spheres in the long term, even as a versatile supplement. Their adaptability presents a powerful tool in the hand of optical designers – a tool that is constantly improved by developments in production and high precision metrology, reminding us that aspherical production can only be as good as the measurement system. Furthermore, during the optical design process, it is important to consider the different manufacturing methods and their strengths and weaknesses.
Written by Martin Hauer, Project Management, R&D, Sill Optics GmbH & Co. KG