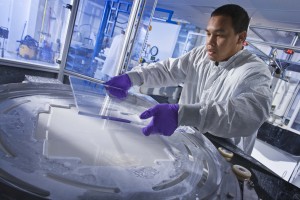
There are many factors which contribute to the successful manufacture of vacuum windows. The understanding and use of cutting-edge technology, quality control via state-of-the-art metrology tools, and understanding of material properties are all critical to their design and manufacture. When combined with a culture of innovation and in-depth and broad experience of precision optics manufacture, these technical capabilities can be honed to ensure optimal manufacture of vacuum windows.
Vacuum windows are components designed to separate different environments while allowing light to pass through. They are commonly used in applications where a controlled atmosphere, such as a vacuum, needs to be maintained on one side of the window while allowing optical observation or the passage of laser beams.
They are made from materials with high transparency to specific wavelengths of light and excellent mechanical strength, common materials including fused silica (known for its low thermal expansion and high transparency in the ultraviolet to infrared range); sapphire (extremely hard and durable, suitable for harsh environments); borosilicate (excellent thermal resistance, low thermal expansion, and high chemical durability); and Zinc Sulfide (high transparency in the visible and infrared spectrum and good mechanical strength and resistance to thermal shock). To enhance performance, vacuum windows may have anti-reflective coatings applied to reduce reflection losses and increase transmission. Coatings are selected based on the specific wavelength range used in the application.
Most obviously vacuum windows need to be able to withstand the pressure differential between the vacuum environment and the external atmosphere. This requires high mechanical strength and careful design to prevent deformation or breakage. Also, in many applications, vacuum windows need to operate under varying temperatures without significant thermal expansion or distortion, which can affect the optical performance.
Applications
Vacuum windows are typically used in laser systems where they are used to transmit laser beams into or out of vacuum chambers; in spectroscopy where they allow light to enter or exit a spectrometer while maintaining a vacuum environment for accurate measurements; in microscopy where they enable observation of samples under vacuum conditions; in space applications where they protect instruments where a vacuum is present; and in semiconductor manufacturing where they are used in vacuum chambers for processes like chemical vapor deposition or etching.
They are typically mounted in specially designed frames or flanges that provide a seal between the window and the chamber, ensuring no leaks that could compromise the vacuum. All in all, by combining appropriate materials, coatings, and design features, vacuum windows ensure high optical performance while maintaining the integrity of the vacuum environment in precision optical systems.
Technical capabilities
Various technical capabilities are required to successfully make vacuum windows, and these capabilities ensure the creation of long-life, high-performance optics.
- Advanced manufacturing capabilities
Advanced manufacturing capabilities are essential for producing high-quality vacuum windows, as they ensure the final product meets stringent performance and reliability standards. This includes precision machining, which is critical in shaping materials to extremely tight tolerances. Such precision is vital because even minor deviations can significantly impact the optical performance and structural integrity of the vacuum windows. In addition, sophisticated polishing techniques are employed to achieve high optical clarity and surface smoothness. These techniques minimize surface irregularities, defects, and sub-surface damage thereby reducing scattering and enhancing light transmission through the window.
Advanced polishing processes are needed to achieve a near flawless surface finish, which is crucial for applications requiring high optical performance. Additionally, the use of state-of-the-art coating facilities is necessary for applying anti-reflective and other specialized coatings with high precision. These coatings play a significant role in enhancing the performance of vacuum windows by reducing reflections, improving light transmission, and providing protection against environmental factors such as moisture and chemical exposure. The ability to apply these coatings uniformly and accurately is vital and only possible with advanced technological capabilities and expertise.
The integration of cutting-edge technologies and equipment in the manufacturing process allows for greater control and consistency in production, ensuring that each vacuum window meets the highest quality standards. This combination of precision machining, sophisticated polishing, and advanced coating techniques underscores the importance of advanced manufacturing capabilities in producing high-quality vacuum windows that perform reliably in demanding environments.
- Material expertise
Expertise in a wide range of materials is another critical technical capability. Manufacturers must be capable of working with various optical materials — as mentioned previously — such as fused silica, sapphire, borosilicate, and Zinc Sulfide, and possess a deep understanding of these materials' properties and behaviours under different environmental conditions, including vacuum and varying temperatures.
For example, fused silica is known for its excellent thermal stability and low thermal expansion, making it ideal for applications where the window will experience significant temperature changes. In a high-temperature environment, fused silica maintains its shape and optical clarity, ensuring consistent performance. Additionally, its low coefficient of thermal expansion minimizes the risk of thermal stress and potential cracking, which is crucial in maintaining the integrity of the vacuum window.
On the other hand, sapphire (shown above) is valued for its exceptional hardness and durability. Sapphire's high mechanical strength makes it suitable for harsh environments where the window might be exposed to abrasive particles or high-pressure conditions. Its durability ensures that the window remains intact and functional even under mechanical stress, which is particularly important in aerospace and industrial applications where reliability and longevity are paramount.
An excellent relationship with material suppliers is also important. The grade and quality of raw optical materials can have a significant impact on both the optical and mechanical performance of the final window. The lead time for raw materials can be a significant contribution to the overall project deadlines. Therefore, both the polisher and raw material vendor need to be in close collaboration to ensure on-time compliance to final performance specification of the vacuum window.
- Quality control
Quality control and metrology are fundamental technical capabilities to ensure that each optical component meets the required specifications and standards. This involves the use of advanced metrology tools which measure surface quality, flatness, and other critical parameters with high accuracy. These sophisticated instruments are capable of detecting minute deviations from design specifications, ensuring that even the smallest imperfections are identified and corrected. High-precision measurements are crucial because any aberrations can significantly impact the performance of vacuum windows, especially in high-stakes applications like those found in aerospace and semiconductor manufacturing.
The use of advanced metrology tools such as laser interferometers and 3D optical profilers facilitates a comprehensive understanding of the optical surfaces' characteristics, enabling precise control over the manufacturing process. This level of precision ensures that components can perform reliably under various operational conditions, such as extreme temperatures or vacuum environments. Alongside these advanced tools, rigorous quality control processes should be implemented at multiple stages of production. This includes thorough inspections of raw materials, in-process evaluations, and final product testing, ensuring consistency and adherence to stringent quality standards.
Continual investment in R&D facilitates the discovery and application of novel materials, coatings, and manufacturing methods that not only enhance the performance of optical products but also lead to significant cost reductions for customers. An innovation-driven culture within an organization drives the technical capabilities needed to address the dynamic needs of the market, and helps to anticipate future demands, thereby sustaining long-term success and customer satisfaction.
Experience and expertise also play pivotal roles in manufacturing high-performance optical components, providing a robust understanding of the intricacies involved in the design and production of sophisticated vacuum windows and the use of cutting-edge technology to optimize outcomes. This experience can be measured in years but also in the breadth of sectors served, a specialized understanding enabling technical solutions that are precisely tailored to meet the unique needs of, for example, the aerospace, semiconductor and specialist instrumentation industries. By integrating state-of-the-art technology with industry-specific insights, complex challenges can be addressed, enhancing performance, and driving innovation in vacuum window manufacturing.
Blending technical capabilities with quality control
The manufacture of vacuum windows relies on a blend of advanced technical capabilities and rigorous quality control measures. These windows, used extensively in applications ranging from laser systems to space instruments, are made using precision machining and sophisticated polishing to achieve high optical clarity, while advanced coating techniques enhance light transmission and durability. Quality control is also paramount to ensure each window meets stringent performance criteria. A culture of innovation and extensive experience in precision optics also allows manufacturers to continuously improve their techniques and adapt to new challenges, thereby maintaining high standards in vacuum window production.
Written by Kevin Quist, National Sales Manager – Optics, Zygo