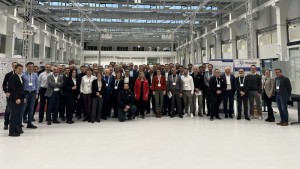
The battery market will have a significant impact in Europe in the coming years, and photonics, in particular lasers and sensors, is set to play a major role. The manufacturing of batteries for electric vehicles necessitates a shift from traditional factories to the establishment of gigafactories – large manufacturing facilities dedicated to the production of components and products related to electrification and decarbonization technologies. Laser cutting and welding techniques have already been seamlessly integrated into battery production lines, reducing time and costs while increasing productivity.
The growing demand for modern electric vehicles has necessitated the development of more efficient batteries with enhanced performance. Laser cutting and welding techniques are already integrated into battery production lines. Laser cutting finds applications in various battery components, including separators and electrodes. Laser welding has evolved to meet the requirements of minimal heat-affected zones, precise control of penetration depth, high processing speed, and the welding of dissimilar metals, thanks to the development of new laser sources with the right parameters. During this two-day meeting hosted by the University of Stuttgart at the cutting-edge research campus ARENA2036, a panel of experts discussed the latest developments, new applications, and market trends. Take a look at the album of pictures of the event.
In the domain of Cathode/Anode Manufacturing, Precitec’s sensors allow the inline and contactless measurement of critical quality criteria in cell production. Meanwhile, TRUMPF highlighted the challenges of Laser Cutting of Battery Foils due to the complexity of foil materials and electrode designs.
In the context of Battery Cell Manufacturing, Ennovasense introduced its single-sided sensor for measuring the thickness of various types and geometries of coatings on bipolar plates. The lightweight and thermally conductive nature of aluminum makes it advantageous for e-mobility applications, and Civan Lasers has developed dynamic laser beam welding for high-strength aluminum battery housings. An improved cycle time is essential for the electric vehicle business model. Which is why Scanlab developed on-the-fly welding for 1D linear stages to enhance battery manufacturing efficiency.
Photonics applications in Battery Module Manufacturing not only reduce time and costs but also enhance productivity, as PRIMES mentioned during their presentation. While in the field of Fuel Cell Manufacturing, the Institut für Strahlwerkzeuge has developed a High-speed X-Ray Imaging that detects the formation of pores during Welding of Copper Pins.
The EPIC Meeting on Laser Applications along Battery Manufacturing Process at ARENA2036 has featured 20 speakers representing the entire supply chain, including automotive companies, battery manufacturers, process monitoring firms, and laser manufacturers. For the complete agenda, please click here.
Below you can find the abstracts of the previously mentioned speakers.
INTRODUCTION TO THE BATTERY MANUFACTURING PROCESS
Jan-Philipp Weberpals, Subject Specialist Laser Beam Processes for Car Body Construction and Electromobility at Audi during his speech
The battery system of an electrically powered vehicle consists of several battery modules, which are assembled by a large number of individual battery cells. The terminals of the battery cells are interconnected by means of cell connectors. Laser welding technology is used to electrically connect the terminals to the cell connectors. This new product requirements described here, such as range, charging behavior and performance compared to requirements in car body construction, have also increased the complexity of the manufacturing methods and require the use of highly flexible manufacturing technologies. Laser beam technology offers a wide range of possible solutions for electromobility. In addition to the cell contacts as the heart of the battery module, its housing must be also connected by using laser beam technology. Thus, the challenges in prototyping are evident and the question of one equipment for different requirements is obvious. The changing materials according to the requirements also increase the possible applications of laser beam technology. In conclusion, the influence of the wavelength of the used laser source on the processing of copper materials is discussed and compared.
Carrs Welding Technologies – SoniLaser – Ultrasonic Assisted Laser Welding for High Volume Assembly of Automotive Battery Packs – Phil Carr, Director
Jens Reiser, Sales & Innovation E-Mobility at Precitec, during his speech.
Carrs, the contract welders, tackle challenging welding tasks, including the difficult task of joining copper to aluminum due to the formation of Intermetallic compounds. Their motivation is to find solutions for repairing metal components. Soni-Laser fulfilled a dream by collaborating with Brunel University to explore ultrasonic excitation for welding copper to aluminum, a critical need in the battery industry. This research aims to optimize battery connections.
SESSION 1: Photonics Applications in Cathode/Anode Manufacturing
Precitec – Photonical Quality Systems for Foil Manufacturing – Jens Reiser, Sales & Innovation E-Mobility
This presentation focuses on Precitec‘s solutions for optical sensors. In the first part, Reiser discussed the physical principles behind Precitec sensors, including chromatic confocal and interferometric measuring techniques that can achieve resolutions below 1 micron. These sensors enable the inline and contactless measurement of critical quality criteria in cell production. In the second part of the presentation, he covered topics such as (i) detecting impurities (e.g., particles in the 10 – 50 micron range), (ii) measuring thickness and edge superelevation, and (iii) inspecting cutting burrs. The presentation concluded by providing an overview of potential closed-loop strategies for future MP (manufacturing process) lines.