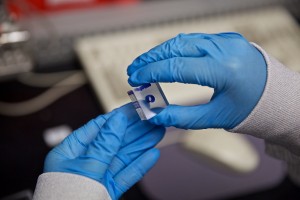
Micromanufacturing becomes increasingly important in medical manufacturing where precise tolerances, minimal heat output and miniaturization are critical. Lasers add many benefits to the manufacturing process, such as the ability to remove material by micron units and to manufacture parts without initiating physical contact with the materials. The tremendous advantages of laser manufacturing processes include better miniaturization, sterile shaping processes and faster prototyping and production of medical devices.
Laser-based medical manufacturing grows each year, and decision makers need to consider the benefits of changing some of their medical device manufacturing processes to incorporate lasers. The benefits include managing diseases at lower costs, enabling home and mobile care and preventing contamination. Lasers deliver incredible benefits to the manufacture of medical devices. These include incorporating biological and nanostructured materials into devices and scaffolds with better control, sensitivity and selectivity.
The issues facing the medical manufacturing industry aren’t just the need for manufacturing efficiency and cost-savings. In-patient care has become cost-prohibitive, and statistics show that outpatient and in-home care are at the forefront of the future of medical manufacturing. Miniaturized laser-made devices are a big part of advanced medical technology that can be used in the home, mobile medical services and outpatient settings. Some of the advanced laser manufacturing techniques include:
Laser ablation
Laser ablation ranks as one of the top medical manufacturing procedures because of its versatility. Manufacturers can remove one micron layer at a time to shape medical devices with extraordinary precision. The technique works on both the macro and micro scales and can be used on metals and polymers for a wide variety of medical products for neurovascular, cardiovascular and catheterization products.
The technique can be performed with a variety of lasers that include eximer, ultrafast and CO2 diode-pumped lasers. The applications of laser ablation technology include:
- Removing coatings from fine wires
- Catheter tip shaping
- Manufacturing micro surgical instruments
- Building micro implants
- Balloon surface texturing
The potential of laser ablation techniques is almost limitless because it employs techniques that are similar to additive manufacturing. Instead of adding one layer at a time, the process removes a single layer until the desired specifications are achieved. The technique extends the boundaries of micromanufacturing capability.
Laser cutting
Laser cutting uses a laser beam to cut material by melting or ablating the material. Coaxial gas nozzles are used to remove the waste material. This is one of the most frequently used medical manufacturing techniques because it’s simple, fast and free of contamination. The process usually employs a fiber or Nd:YAG laser. Ultrafast laser cutting can eliminate wasted heat and burrs while ensuring a clean-edged cut.
The medical device applications of laser cutting include manufacturing stents, heart valves, medical tools and device components. The benefits of laser cutting include minimal part distortion, precision cutting ability, no wear and tear on tools, faster prototyping and the ability to cut most metals and materials. Some of the top products that are manufactured with laser cutting include:
- Thin-walled stents
- Pull rings
- Customized medical instruments
- Delivery system components
- Precision tube cutting
- Bioresorbable scaffolds
- Ability to customize the geometry of device parts and components
Nitinol laser cutting
Cutting nitinol is a special ultrafast laser cutting process for the material used in catheter components. Any manufacturing process generates heat, and that can be a big problem with today’s smart materials, such as nitinol. Cutting thin elastic plates for catheters takes special lasers that include femtosecond and continuous wave lasers. This process doesn’t damage the diamond shaped elements of the material. Ultrafast cutting eliminates most of the thermal heat output of the cutting process and provides a cut that leaves the underlying structure of nitinol intact.
Laser welding
Laser welding can join two similar materials without the essential filler materials used in traditional welding. The medical applications of the technology include the ability to join parts that are too small to be connected by other methods. The technology can utilize industrial lasers that have precise control, measurement and monitoring capabilities of the laser power levels. Generally, minimal heat is applied, and the welding process requires experienced technicians using optical microscopes and micro-manipulators. The uses of laser welding in medical manufacturing include:
- Repairing damaged instruments
- Welding pull ring assemblies
- Connecting wires
- Welding wire components for delivery systems
- Welding components of ophthalmic, interventional cardiology, sports medicine, neurovascular and electrophysiology devices
Laser drilling
Collaborative robotic arm integrated into a UV DPSS laser production workcell.
Laser drilling is a subcategory of laser ablation that drills one layer at a time through metals and polymers to create micon-width holes to the desired depth or completely through the material. Holes as small as a couple of microns in width can’t be drilled by conventional methods. The most common uses for the technology in medical manufacturing are drilling infusion catheters and embolic protection filters. Devices that benefit from precision laser drilling include:
- Balloon catheters
- Micro hole arrays
- Infusion catheters
- Flow access holes
- Embolic protection filters
- Glucose monitoring sensors
- Angioplasty balloons
- Pacemaker components
- Drug-delivery balloons
Laser micromachining has become increasingly critical in today’s medical manufacturing processes. The approach eliminates the use of expensive photomasks and provides the greatest possible precision, given today’s technology. The technique is especially beneficial in dealing with polymeric substrates because the laser processes employ photoelectrons that are large enough to do the job without dissociating the chemical bonds of the polymer.
The need for speed in medical manufacturing
Studies, statistics and anecdotal evidence overwhelmingly support the idea that speed is the most important aspect of medical manufacturing. Regulatory hurdles, cost overruns and competitive technology make every manufacturing initiative dependent on speed to make a profit. Laser manufacturing provides the necessary speed to meet deadlines, lower costs and achieve miniaturization goals. The processes are clearly superior to Swiss machining and electrical discharge machining in meeting the demands of agile manufacturing in the competitive medical industry.
Written by Mikayla St. Clair, PR Specialist, and Laser Light Technologies