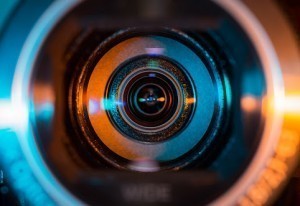
Manufacturers face ever-rising demands for efficiency and product quality — two qualities that are often at odds. Machine vision systems in manufacturing pose a solution, as they can inspect products faster and more reliably than manual alternatives. Despite that advantage, these systems carry unique challenges of their own.
Machine vision requires adequate lighting to process visual data accurately. This lighting must enhance contrast while reducing glare and shadows, but conventional approaches can distract nearby workers or require expensive complementary technology. Recent advances in hidden strobe hardware provide an answer.
What Are Hidden Strobe Systems?
Despite the name, hidden strobe systems don’t technically hide their lights. Instead, they use a strobing effect that’s too fast for human eyes to register the flashes. Most people can’t detect flickering above 50 Hertz, or 50 cycles per second. Consequently, if a light flashes at a rate high enough above that threshold, it’s perceived as continuous.
Strobing at any speed helps machine vision systems because the stroboscopic effect makes fast-moving objects appear stationary. That way, cameras can capture an in-focus and well-lit picture of an object without slowing things down. Machine learning algorithms can then analyze it for reliable quality control without the bottlenecks they may otherwise create.
Hidden strobe hardware takes this concept to extremes by pulsing far above detectable levels for humans. It’s also fast enough to more than compensate for the high shutter speeds necessary to take detailed, blur-free images of fast-moving objects on the production line.
How Hidden Strobe Hardware Improves Machine Vision
This technology has several implications for vision systems in manufacturing. These benefits improve operations for the automated quality control system and human employees working nearby.
Improving Object Lighting
The most obvious advantage of hidden strobe hardware is that it improves machine vision reliability. The LEDs in these systems flash thousands of times per second, ensuring consistent lighting regardless of how fast the scanned objects move or the system’s shutter speed. This consistent lighting reduces motion blur and maximizes contrast for more accurate readings.
Hidden strobe systems also pulse brighter than actual continuous lighting. As a result, they can minimize shadows from wrinkles in plastic wrap or other soft components that may otherwise hinder machine vision accuracy. Manufacturers can attach polarizers to tailor these systems to specific workflow and lighting conditions.
These improvements mean manufacturers don’t have to choose between reliability and efficiency. They can scan products for defects with higher accuracy without slowing the production line. In some cases, these fast strobes may even warrant speeding the workflow.
Protecting Nearby Workers
Conventional strobe lighting can achieve similar benefits but may endanger nearby employees. Roughly 50 million people globally have epilepsy, which could make them sensitive to flashing lights, even to the point of seizures. Even apart from these extremes, light flickering poses a significant hazard.
Flashing lights are distracting and disorienting. Consequently, employees working near or passing by strobe-lit vision systems may be unable to focus, making potentially dangerous mistakes more likely. Hidden strobe hardware addresses this concern through its faster strobing rate.
Cycle rates above 1,000 times a second are far too fast for humans to detect. Workers will perceive it as continuous light, preventing the disorientation that comes with flickering. They’ll be able to focus and work safely alongside these machines as a result, reducing workplace accidents and improving overall productivity.
Cost Efficiency
Hidden strobes also make vision systems in manufacturing more cost-effective. Conventional lighting systems require manufacturers to make sacrifices in one of two ways. They must either use strobes to boost efficiency and install protective shielding or use continuous lighting, which is either slower or consumes more energy.
Using hidden strobes instead offers an ideal middle ground. The light appears continuous to the human eye, removing the need to pay for additional shielding equipment to protect workers. Manufacturers benefit from lower production costs through increased efficiency without more upfront spending.
Simultaneously, hidden strobes benefit from energy savings by cycling instead of remaining on. Unlike other light types, turning LEDs on and off doesn’t affect their life span or use more energy. Consequently, strobing yields utility savings over time and doesn’t sacrifice efficiency or limit equipment service lives.
Implementing Vision Systems in Manufacturing Effectively
The extent to which manufacturers experience these benefits depends on how they implement this technology. A few best practices and extra steps can help hidden strobe hardware and their accompanying machine vision systems.
Employee training is one of the most important areas to address. Vision systems should accelerate workflows to free workers to focus on other tasks, and this adjustment will require some retraining to get employees up to speed. Other vision technologies, like augmented reality (AR), are promising solutions. AR systems can boost training effectiveness by 30% by making workflows more engaging and increasing data accessibility.
Vision systems in manufacturing must also adapt to the specific workflow and products in question. Effective machine vision requires consistent performance along three criteria — maximizing contrast of important features, minimizing contrast elsewhere and ensuring confidence in accuracy.
Hidden strobe hardware meets criteria one and three on its own. Manufacturers may need to install polarizing filters and restrict ambient light around the vision system to meet the second.
The machine learning model analyzing this visual data requires attention, too. Organizations must train these algorithms on information similar to what they’ll measure in the real world to achieve optimal performance. Cleansing this data removes inconsistencies and creates better organization, which is a vital step to minimize mistakes.
Hidden Strobes Unlock Machine Vision’s Potential
Machine vision systems in manufacturing are a potential game-changer, even with older lighting solutions. Their accuracy and efficiency are too high to overlook, especially given manual methods’ high error rates and tendency to create bottlenecks. Hidden strobe hardware takes these benefits further, letting manufacturers enjoy their full extent.
Hidden strobes are more reliable, safer and more cost-effective in the long run than conventional lighting methods. These advantages combine with those of machine vision to unlock new possibilities in quality control. As more manufacturers capitalize on this opportunity, machine vision and hidden strobes could usher in new quality assurance and efficiency standards.
Written by Emily Newton, Editor-in-Chief of Revolutionized, an online magazine that covers innovations in the industrial sector.