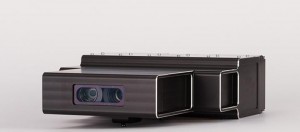
Machine vision integrators are confronted with seemingly endless options when designing an inspection system. Perhaps the most critical decision is whether to use line-scan or area-scan cameras. While both perform a similar role, these technologies are miles apart in how an image is captured.
"Line-scan cameras build images a single pixel row at a time using a sensor which passes in a linear motion over an object, or more often when the object passes under the sensor," notes Klaus Riemer, Product Manager for Chromasens GmbH, a leading manufacturer of line-scan camera systems. "As a conveyor or web moves, a 2D image can be reconstructed in software line-by-line for inspection. This makes it ideal for high-speed continuous applications such as document scanning, print inspection, web inspection of paper, aluminum, steel or glass, and in detailed inspections requiring measurements be done in microns. Line-scan can also inspect round bodies without perspective distortion."
Continuous images
Because line-scan cameras use a single row of pixels, they can build continuous images not limited to a specific vertical resolution, allowing for much higher resolutions than area-scan cameras in both 2D and 3D. Chromasens has been at the forefront of line scan technology for more than a decade. It recently introduced its 3DPIXA HR 2 µm 3D line scan camera that covers a 16mm field of view and achieves 0.5µm height resolution or twice the resolution of previous versions. As a result of this precision, manufacturers of semiconductors and other electronics can improve productivity by preventing defects, reducing waste, and increasing yield while achieving compliance with traceability requirements.
In contrast, area-scan cameras are more general purpose. Used in the majority of machine vision systems, they contain a large matrix of pixels that capture a 2D image of a given scene in one exposure cycle with horizontal and vertical elements, for example in 640 x 480 pixels. While they may offer easier setup and alignment, they are not always effective when an object under inspection is moving or if it cannot be contained in a practical size field of view. Area-scan cameras are best suited towards applications where the object is stationary, even if only momentarily. Uninterrupted capture of continuous materials by an area-scan camera is achieved only by capturing overlapping images. Software must painstakingly crop each individual image, eliminate distortion and assemble the images in the correct sequence.
Fit more easily
Additional benefits of line-scan systems include their more compact footprints that allow them to fit more easily into tight spaces, for instance, when a camera must peek through rollers on a conveyor to view the bottom of a part. Also, line-scan cameras create smear-free images of fast moving objects without requiring strobing or the redundant processing of frame overlaps.
Despite these advantages, integrators regularly harbor reservations about deploying line-scan cameras because of perceived system complexities or higher cost. In reality, a single line-scan camera will often do the job of several area-scan cameras, minimizing setup and overall system cost. And while coordination and acquisition timing are critical, line-scan cameras require only simple illumination.