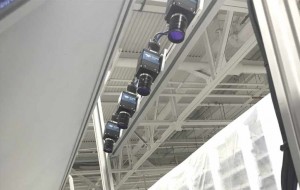
In the ever-evolving landscape of green energy, electric vehicles (EVs) stand out as key players in the transition towards a sustainable future. Electric vehicle sales have been growing exponentially due to affordability, improving technology, and government support for green energy initiatives.
Globally, 10% of passenger vehicles sold in 2022 were all-electric, according to analysis conducted by the World Resources Institute using data from the International Energy Agency—this is 10 times more than just five years prior. Norway led the way with 80% of passenger vehicle sales being all-electric, followed by Iceland (41%), Sweden (32%), the Netherlands (24%), and China (22%).
China’s position is notable as it is the biggest car market in the world; the country had more EV sales in 2022 than the rest of the world combined. China has also made strategic investments in EV manufacturing, and Chinese consumers can now choose from more than 300 EV models.
In comparison, the European Union (at 12%) and the United States (at 6%) had lower EV sales as a percentage of all passenger vehicles sold, but both markets are growing quickly. In the US, market leader Tesla aggressively slashed prices in 2023, which put pressure on competitors to make their vehicles more affordable. With the average price of a new EV dropping 22% in 2023 to $50,683, the average price gap between EVs and all cars is now under $3,000 in the US. And yet, EV supply is currently outpacing demand in the US as automakers navigate how to move forward.
Source: World Resources Institute
Factors such as the cost of EVs, the distance that can be traveled on a single charge (range), and the amount of time it takes to recharge the battery all play into the growth trajectory. Experts predict that when it becomes cheaper to buy, own, and operate an EV than a traditional gas-powered vehicle, the technology will reach a tipping point and the growth trajectory will rapidly curve upward.
As the demand for EVs continues to grow, it's imperative to delve into the heart of these vehicles—the battery pack. The most widely used type of battery for EVs today are lithium-ion battery (LIB) packs due to their high energy density and voltage, stability, low weight, and long-life cycle.
This article explores the trends in electric vehicles, the crucial role of battery packs, the intricacies of LIB manufacturing, and why machine vision inspection and artificial intelligence (AI) are game changers for the industry.
Trends in Electric Vehicles and Lithium-Ion Batteries
According to Grandview Research, the increasing adoption of EVs is catalyzing a remarkable surge in the global production of LIB. The LIB market size was estimated at USD 54.4 billion globally in 2023 and is projected to register a compound annual growth rate (CAGR) of 20.3% from 2024 to 2030.
Governments and industries worldwide are prioritizing the transition toward sustainable and environment-friendly transportation by putting incentives in place to support climate goals, which leads to an increase in the demand for EVs. LIBs have emerged as the cornerstone of this automotive revolution. These batteries power electric vehicles, providing them with the necessary range and performance to compete with traditional internal combustion engine vehicles.
The Crucial Role of Battery Packs
At the core of every electric vehicle lies the battery pack—an essential component that dictates not only the vehicle's performance but also its range. Each battery pack is made up of modules, and these modules are comprised of individual cells that look very similar to well-known AA batteries.
LIBs are the current gold standard in EV power, and the manufacturing and inspection of these batteries is critical. As explained in the Tech Briefs EV Battery Innovation Special Report, many LIBs use cylindrical cells because they are mature and less expensive to manufacture. Since 2008, there has been an 89% drop in the average cost of an EV LIB pack, from $1,355/kilowatt-hour (kWh) to $153/kWh in 2022, and this is expected to decrease even further to $100/kWh by 2026.
Cylindrical cells were one of the first types of mass-produced lithium battery types, and are made up of sheets of anodes, separators, and cathodes that are sandwiched and rolled up. These cells are well-suited for automated manufacturing, and the shape allows the cell to tolerate a higher level of internal pressure without deformation.
Inside a Lithium-ion battery. (Image courtesy of Teledyne DALSA)
These cells are then encased in a clamshell-type plastic enclosure to make up a module. Multiple modules then make up the battery pack that powers an EV. Hundreds to thousands of battery cells are needed for each vehicle and the battery pack is a key determinant of the weight and expense of the final vehicle.
Alan Eddy is the Chief Technology Officer at Tensor ID, a systems integrator that works with the industry’s largest lithium-ion battery manufacturers and leading EV companies. He explains, “When inspecting batteries that power electric vehicles, the inspection system must address multiple challenges, including a thorough inspection of each battery cell for issues like rust or dents. When one cell is damaged, it diminishes the life of the whole battery pack.”
LIB Manufacturing and Inspection
The manufacturing process for LIBs involves intricate steps, from sourcing raw materials to assembling cells and packaging the final battery packs. Detailed quality inspection during this process is crucial to ensuring the efficiency and safety of the batteries.
Inspection takes place at various stages of battery manufacturing, including:
- Inspection of the foils that are used to make the electrodes (cathodes and anodes)
- Inspection at different stages of assembly
- Inspection of the completed battery cells and modules
Quality control in battery manufacturing presents significant challenges due to the variability in production and the potential impact of defects on performance and safety. Identifying internal defects, especially microscopic ones, is a daunting task. This is where machine vision and AI enter the scene.
In the context of battery manufacturing, machine vision inspection systems can analyze intricate details with unmatched accuracy, speed, and efficiency, resulting in EV battery packs that perform at the highest possible level. Optimizing quality inspection increases the life of the battery and the ability of the battery to hold a charge for longer periods of time.
If an EV includes a 95kWh battery pack (Tesla model S) and the cost per kWh adds up to $150, the battery alone contributes $14.3K to the production cost. Therefore, battery quality is a critical component for EV manufacturers in terms of warranty costs, customer satisfaction, and brand reputation.
At Tensor ID, the systems integrator creates machine vision systems for the inspection of completed EV battery cells and modules, but machine vision can be used at any stage of inspection, including manufacturing and assembly. Eddy states, “For years we've been supplying barcode reader cameras to do these inspections, but there's much more to come in terms of machine vision inspection. In order to automate and become more efficient, battery manufacturers are going to need to look at every element of the inspection process again from start to finish.”
Tensor ID’s vision inspection system uses Teledyne DALSA area scan cameras to inspect each battery cell at the individual level, and as they're completely assembled just before they put the clamshell casing over it. The battery manufacturers are concerned about issues such as reading the barcode, identifying rust and dents, and determining polarity.
AI improves inspection performance and is used to identify rust. Four high-resolution cameras from Teledyne DALSA are used to inspect the battery module. (Image courtesy of Tensor ID)
Because the individual battery cells come in boxes from the supplier, a robot is deployed to remove one at a time for inspection. Each individual battery cell must be inspected before it is put into the clamshell module which will become part of the battery pack. To accurately inspect the stack of batteries, Tensor ID uses four Teledyne DALSA Genie Nano cameras that are positioned to capture an image that is “stitched” together from an entire three-foot wide stack.
When it comes to the inspection of rust, an AI-based software platform is used to classify the images. “AI has been a real game changer when it comes to the inspection of batteries. Rust is particularly difficult to identify accurately due to the shiny, reflective surface of the battery cells,” says Eddy. Tensor ID’s system trains the AI model with Teledyne DALSA’s Astrocyte AI training tool to recognize the difference between rust and other anomalies, such as a fingerprint or speck of dust. The system can then identify and remove any battery cells with rust on them, as this erosion of materials damages the battery’s effectiveness.
Beyond inspection, AI is also poised to play a significant role in optimizing battery performance. AI-driven algorithms can analyze vast amounts of data to fine-tune battery management systems (BMS), improving efficiency and extending the lifespan of batteries. Smart charging, guided by AI, is another area where technology is expected to have a substantial impact for consumers, making the charging process more intelligent and convenient for EV drivers.
Benefits of Machine Vision Inspection for LIBs
Accuracy and Precision
One of the primary advantages of machine vision inspection is its accuracy, precision, and the ability to support the highest quality standards. Traditional inspection methods may overlook microscopic defects that can significantly impact battery performance. Machine vision systems coupled with AI, on the other hand, excel at detecting even the tiniest imperfections—such as a 130-micron dent, which is about the width of a human hair. This ensures the highest level of accuracy and precision in the inspection process.
Efficiency and Speed
Machine vision doesn't just enhance accuracy—it also improves efficiency and speed in the inspection process. Automated systems can rapidly analyze vast quantities of batteries, reducing production time and costs. This efficiency not only benefits manufacturers but also contributes to the overall scalability of EV production.
Safety and Reliability
Ensuring the safety and reliability of electric vehicles is paramount. Machine vision inspection plays a crucial role in achieving this by identifying potential defects that could compromise the integrity of the battery pack and limit its ability to fully charge. By eliminating subpar batteries before they reach the market, machine vision contributes to the overall safety of EVs and heightens the reliability of their power sources.
Future Trends in Batteries and EVs
As technology continues to advance, the future of electric vehicle batteries looks promising. Some key trends to watch include the development of solid-state batteries, which offer improved energy density and safety. Next-generation materials are also being explored to enhance the performance and sustainability of batteries. The current average range of an EV is 219 miles, but cobalt-free batteries could have a range of up to 500 miles on a single charge and new solid-state batteries are being tested that could charge in just seven minutes.
Beyond technological advancements, the industry is also focusing on sustainable practices in battery manufacturing. This includes exploring innovative recycling methods to minimize environmental impact and embracing a circular economy approach, where materials from old batteries are repurposed for new ones.
Ensuring reliability
Transportation currently represents 27% of the world’s greenhouse gas emissions; therefore, replacing internal combustion engines with electric engines or hybrid engines can reduce pollution all over the world. To succeed with a transition to EVs, manufacturers know they must focus on ensuring the highest quality LIBs, since they are one of the most important and the most expensive components of electric vehicles.
In the dynamic landscape of electric vehicle battery manufacturing, machine vision inspection emerges as a transformative force. Tensor ID’s Alan Eddy concludes, “The inspection of EV batteries is complex; even if it fails 1% of the time, that’s a lot.” By combining the precision of AI with the demands of quality control, machine vision ensures that the heart of electric vehicles—the battery pack—is not just a powerhouse but a reliable, safe, and efficient one. As we look towards the future, the integration of AI, the development of cutting-edge battery technologies, and a commitment to sustainability promise to reshape the electric vehicle industry, making it not only a cleaner choice for transportation but also a smarter and more reliable one.
Written by Matthias Moser is a Business Development Leader at Teledyne DALSA, and works with systems integrators on a variety of applications, including battery inspection. Matthias is based in Kitchener, ON, Canada.