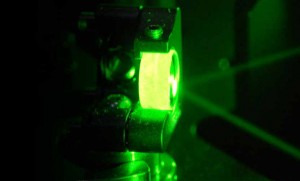
High-power ultrafast laser sources have gained traction in materials processing systems over the last few years due to the market need for a robust, turnkey ultrafast laser that is capable of delivering intense peak powers in the megawatt and terawatt regimes.1 Such ultrafast laser systems are highly advantageous for micromachining because of their unique properties. For example, using a high-power ultrafast source in micromachining provides the ability to machine a larger breadth of materials and reach higher precision.
One of the key limitations in increasing the peak power of ultrafast lasers is thermal lensing, which could be catastrophic to the laser cavity. High-peak power ultrafast laser systems can cause strong nonlinear effect in cavity optics that could lead to heat accumulation in high-repetition rate systems. This non-uniform heat distribution will cause a refractive index gradient in the optics that can shift its focal length. Some of these effects can be carefully modeled and mitigated through a thorough design of the resonator.2 On the other hand, high-order aberrations are very difficult to compensate for and could lead to low-quality laser beam.
In some cases, thermal lensing effects can be even more detrimental where the laser cavity is completely out of alignment and no resonance is observed. Diffraction-limited performance in mode-locked lasers can only be reached by minimizing thermal effects in the laser cavity.
Fighting back with specialized dispersive mirrors
Advancements in multi-layer dielectric coatings have made dispersive mirrors an essential part of ultrafast laser cavities by compensating for the positive group delay dispersion (GDD) found in most optical media, which elongates pulse duration and reduces peak power. Such pulse compressing mirrors offer a negative GDD over a broad wavelength range that can support very short laser pulses while limiting the losses and the constant need for laser alignment. However, highly-dispersive mirrors can experience thermal lensing, hindering system performance.
Thankfully, new developments in coating technology allow for the creation of novel dispersive mirrors with negligible thermal lensing (Figure 1 above). These mirrors are ideal for developing high-power ultrafast materials processing systems by reducing the thermal effects generated by the cavity mirrors. These mirrors combine the highly-negative broadband GDD and low loss over a broad wavelength range that dispersive mirrors offer with reduced thermal lensing (Figure 2). This is achieved by a careful manipulation of the various parameters of the optical design and the deposition process leading to unmatched performance in high-power ultrafast laser systems such as Yb:YAG, Er:YAG, thulium, and holmium laser systems.
Figure 2: Dispersive mirrors with low thermal lensing still maintain high reflectivity and negative GDD with a high magnitude, which is critical in high-precision materials processing systems.
Testing thermal performance
The thermal lensing effects of these mirrors were tested in a Yb:YAG thin disk laser operating at continuous wave (CW) mode by measuring the increase in temperature at the surface of the mirrors using an infrared camera (FLIR SC305). Figure 3 shows the spectral performance of a dispersive mirror without the new, low-thermal lensing coating with a GDD of -3000 fs2 between 1010 and 1050 nm and high reflectivity. This mirror experienced a temperature change of 57K, which caused the laser mode and oscillator stability to deteriorate. Figures 4 and 5 show the increases in temperature measured for two dispersive mirrors with reduced thermal lensing with GDD values of -1000 fs2 and -3000 fs2, respectively. The dispersive mirrors with reduced thermal lensing showed a much lower temperature increase compared to the traditional mirror. Temperature increases of 10K and 20K were observed in the mirrors with GDD of -1000 fs2 and -3000 fs2, respectively, significantly less than that of the traditional dispersive mirror. Both laser mode and oscillator stability were maintained, allowing the laser system to achieve mode-locking and function properly.
Figure 3: The dispersive mirror without new, low-thermal lensing coatings experienced a 57K temperature change during testing, which destabilizes the laser and causes system performance to deteriorate.
Figure 4: The low-thermal lensing dispersive mirror with a GDD of -1,000 fs2 experienced a 10K temperature change during testing, avoiding any detectable thermally-induced performance reduction.
Figure 5: The low-thermal lensing dispersive mirror with a GDD of -3,000 fs2 experienced a 20K temperature change during testing, still avoiding any detectable thermally-induced performance reduction.
When are low-thermal lensing coatings needed?
Such reduction in heat buildup in these mirrors is highly-advantageous in reducing thermal lensing in high-power ultrafast mode-locked lasers that will allow for pushing the power barriers of materials processing systems. However, this technology is not required for all ultrafast laser systems. Ti:sapphire laser sources do not typically achieve high-enough average powers for heat buildup and thermal lensing to become significant problems. Fiber laser sources also do not require low-thermal lensing coatings, as they do not have solid-state lasing cavities where detrimental thermal effects could occur. In these situations, pulse compressing optics without the novel thermally-stable coatings are sufficient. However, reducing thermal lensing is important for high-power, solid-state ultrafast laser materials processing systems using sources such as Er:YAG, holmium, and thulium lasers.
Written by Tony Karam, Ultrafast Optics Product Line Manager, Edmund Optics
References:
- Backus, S.; Durfee III C. G.; Murane, M. M.; Kapteyn, H. C. High power ultrafast lasers. Rev. Sci. Inst. 1998, 69, 1207
- Vanherzeele, H. Thermal lensing measurement and compensation in a continuous-wave mode-locked Nd:YLF laser. 1988, 13, 369