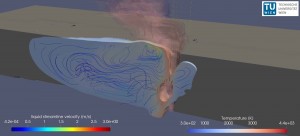
Laser experts at the Technical University Wien (TU Wien) in Vienna, have collaborated with Civan Lasers (Jerusalem) to simulate its disruptive dynamic beam laser technology. As the first and only multiphysics simulation software capable of modeling the megahertz-level frequencies of Civan’s dynamic beam lasers (DBLs), the work improves understanding of how these beam-shaping lasers influence control of keyhole and melt-pool dynamics.
“The beam-shaping capability of Civan’s laser opens up new possibilities for increasing welding quality and speed in many of today’s challenging applications,” explains professor Andreas Otto at the Institute of Production Engineering and Photonic Technologies, TU Wien. “It's a really significant development that will shape the future of laser materials-processing technology and even open up the development of entirely new applications.”
Providing unique insight into the effect of each beam shape and frequency on keyhole and melt-pool dynamics, this simulation tool will play a critical role in process development, helping to optimize beam shape and frequency for a variety of laser materials-processing applications. Current simulations have focused on butt welding of stainless-steel pipe with a gap. Future collaboration will target other welding, drilling, and surface treatment applications involving a variety of materials.
The welding of a stainless-steel pipe in a butt-joint configuration was particularly challenging. The finite precision in the cut pipe fronts plus limitations of the clamping system resulted in a small gap (of the order of tens of microns, up to a few hundred microns). This welding process, which relied on standard static laser sources, did not use filler material, and the result was a gap at the contact line and low-quality weld seams.
To come up with a solution, Civan experimented with its DBL and then collaborated with TU Wien to simulate the process. The result was a better understanding of why certain shapes work better than others. The simulation also helped in the design of alternative beam shapes that might work for this problem and led to the development of general guidelines on how to design suitable beam shapes for such situations.
While current beam-shaping solutions such as diffractive optical elements can’t be changed on the fly, the use of beam oscillation with scanners and 2-in-1 fibers has led to improvements in processes in recent years. However, such mechanical scanners often can’t change fast enough to minimize keyhole instability issues. In contrast, Civan’s patented coherent beam combination modulates beam shape as desired at megahertz frequencies, without any moving parts.
Civan’s lasers use optical phased array coherent beam combining, which merges many single-mode laser beams into one larger beam. Each laser emits its own light, which overlaps with other beams in the far field, to create a diffraction pattern that unlocks the flexibility needed to easily manipulate the beam shape in real time to create a DBL. By using phase modulators to control individual beams, the resulting interference pattern can be changed to maximize the beam spot position and produce various shape patterns inscribed by the beam's motion — all of which can be done at speeds of up to hundreds of megahertz.
“We have a very powerful tool offering complex control of many parameters, such as beam shape, shape frequency, shape sequencing, and focus steering,” explains Dr. Eyal Shekel, CEO of Civan. “Until now, we’ve used basic theory, intuition, and experience to guide us in process optimization. Dr. Otto’s novel simulation tool for beam-based manufacturing processes is a real eye-opener and provides key insights into the dynamics of the keyhole, melt pool, and resolidification, so every problem should start with a good simulation such as this.”