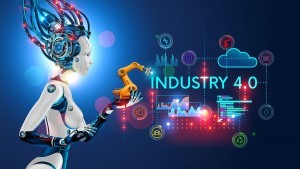
Non-contact measurement technologies are at the forefront of the transformative shift known as Industry 4.0, revolutionizing modern manufacturing and production processes. This era of digital industrial technology integrates smart automation, data exchange and innovative manufacturing techniques.
These methods, leveraging advanced sensors and light technologies, offer unparalleled precision, speed and efficiency. These methods significantly reduce the risk of damage to materials, enhance product quality and streamline production workflows. It marks a significant leap over traditional contact-based measurement techniques.
What Is Non-Contact Measurement?
Non-contact measurement is pivotal in Industry 4.0, aligning with the era’s emphasis on automation, data exchange and interconnected systems. By leveraging advanced sensors, laser technologies and imaging systems, it employs smart systems that can increasingly assist workers or expand their abilities. This approach enables more precise control over manufacturing processes and enhances quality assurance practices across various stages of production.
The applications of this technology span numerous industries — including automotive, aerospace, electronics and health care — facilitating tasks from the inspection of complex components to monitoring production lines in real time.
The advantages of adopting non-contact methods are manifold. Increased accuracy and repeatability are achieved as these techniques eliminate the variability and potential deformation of physical contact approaches.
Additionally, they offer faster processing times, as workers can take measurements quickly and from a distance, significantly boosting productivity. Further, the minimal risk of product damage ensures high-value or delicate items undergo quality control without fearing impairment. It underscores the critical value non-contact measurement brings to modern industrial operations.
The Role of Light Technologies in Non-Contact Measurement
Light technologies — like laser scanning, photogrammetry and lidar — enable non-contact methods within Industry 4.0. Laser scanners emit a laser beam toward an object and measure the time it takes for the light to return, which creates detailed 3D models of objects or scenes at speeds of nearly 500,000 points per second.
Meanwhile, photogrammetry uses photographs from different angles to measure and record precise distances. On the other hand, lidar sensors emit pulsed light waves into the surrounding environment and measure the time it takes for each pulse to return to calculate distances. These technologies capture intricate details of objects and spaces without physical contact and ensure high-fidelity data collection.
In various industries, these light technologies are revolutionizing non-contact measurement practices. For instance, in the automotive industry, they use laser scanning to control the quality of components and guarantee they meet stringent specifications. In construction, lidar creates detailed topographical maps and aids in planning and monitoring. Moreover, the entertainment industry uses photogrammetry to create detailed digital models for visual effects.
The advancements in light technologies — like increased accuracy, faster processing times and the ability to process and interpret vast amounts of data — have made them indispensable in Industry 4.0. They enhance efficiency and precision and enable new possibilities in automation and intelligent manufacturing processes. These applications underscore their importance in the next generation of industrial operations.
Integration Strategies for Light Technologies in Industry 4.0
Integrating light technologies into existing industrial systems requires strategic planning and execution to harness their full potential. One practical approach is adopting digital optical comparators. These advanced tools project magnified images of parts onto a screen for precise measurements.
These devices increase throughput and improve accuracy and repeatability in measurements. They are instrumental in quality control processes, where they can swiftly compare parts to their digital CAD models. Integrating such technologies streamlines their inspection processes, reduces errors and elevates the quality of their products.
The successful integration of light technologies also hinges on the collaboration between various disciplines within an organization. Engineers, IT professionals and operations managers are crucial in this process.
Engineers bring a deep understanding of the technical requirements and capabilities. At the same time, IT professionals are essential for integrating new technologies with existing digital infrastructure. Operations managers, on the other hand, ensure the implementation aligns with production goals and workflow efficiencies.
This cross-disciplinary collaboration overcomes challenges related to compatibility, training and workflow adaptation. It ensures a smooth transition and maximizes the benefits of light technologies in industrial applications.
Challenges and Limitations
Implementing light-based non-contact measurement technologies in industrial settings has challenges, including technical limitations, cost considerations and integration issues. One notable technical challenge is accurately measuring semitransparent surfaces or multiple thin layers, which can confuse sensors and lead to inaccurate readings. It is particularly relevant in electronics and materials science industries, where precision is paramount.
Additionally, the initial cost of acquiring advanced light technologies can be significant, which poses a barrier for smaller operations. Integration with existing systems also presents a hurdle, as it requires compatibility with current workflows and may necessitate substantial changes to infrastructure and processes.
Continuous innovation in light technology is essential to address these challenges. Manufacturers constantly develop more sophisticated sensors and algorithms capable of handling complex measures, such as semitransparent materials. Training programs are also crucial, as they equip personnel with the necessary skills to operate new technologies effectively and integrate them into their workflows.
Moreover, many companies offer customized solutions and support services to facilitate smoother integration, which minimizes disruption to existing operations. Through these concerted efforts, industries can increasingly leverage the benefits of light-based non-contact technologies. This approach overcomes initial obstacles to enhance precision, efficiency and product quality.
The Future of Non-Contact Measurement with Light Technologies
Trends and developments that promise to revolutionize industry standards mark the future of light technologies for non-contact methods. Advancements — like higher resolution sensors, faster data processing algorithms and the integration of AI for real-time analytics — are on the horizon.
These innovations could vastly improve efficiency, accuracy and the ability to measure complex or delicate structures without contact. They open the door to new health care and aerospace engineering applications.
Moreover, integrating these technologies into IoT devices could enable unprecedented automation and precision in manufacturing processes. As these technologies evolve, industry professionals must stay informed and adaptable. This approach ensures they leverage the latest advancements to maintain a competitive edge and push the boundaries of what’s possible in their respective fields.
Leveraging Non-Contact Measurement for Future Success
Organizations must consider the transformative potential of light-based non-contact measurement technologies in their field and how they can elevate their projects' precision, efficiency and innovation. They can embrace these advancements to stay at the forefront of their respective industries, unlocking new possibilities and maintaining a competiti