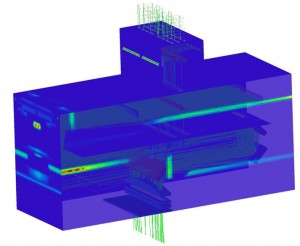
Laser manufacturer nLIGHT uses Zemax OpticStudio to develop a multi-kilowatt laser system used in making next-generation smartphone displays.
nLIGHT develops and manufactures direct diode and fiber lasers based on industry-leading semiconductor laser and optical fiber technology. Recently, nLIGHT used OpticStudio to work on a complex project with specifications requested by a customer that challenged the limits of laser technology. Over the course of a year, nLIGHT engineers developed a precision multi-kilowatt laser system that will be used to bring about a new generation of smartphone screen/display resolution.
nLIGHT’s core technology is semiconductor diode lasers—semiconductor chips that emit light instead of electrons. Most applications require some form of optical system to deliver and manipulate the light from the laser source to the application work surface.
One of nLIGHT’s customers is a display manufacturer that makes TV screens, as well as cell phone and tablet displays. They’re constantly researching ways to make higher-resolution displays.
The company had an idea for a way to create higher-resolution displays that involved using a high-power line of light to deliver the energy for a thermal process.
The challenge was that, while a laser can provide enough energy to create a thermal reaction, you need lots of power over a wide area. Specifically, the customer required a line longer than 200mm and narrower than 200 microns, with greater than 7,000 watts of power, to achieve the optical density on the work surface. In addition, the line of light had to have ultra-high uniformity.
72 lasers into a single beam of light
Principal Engineer Scott Karlsen, the technical lead on this project, explained that nLIGHT’s approach was to combine 72 of the company’s 100-watt diode laser modules into a single beam of light shaped into a line with an initial optical module.
The cylinder lens imaging module (shown partially assembled) is used to image the homogenizer onto the work surface
Then they used a second optical module to homogenize the light to achieve the ultra-high uniformity. A third optical module was used to image the homogenized line beam onto the work surface. They used OpticStudio’s sequential ray tracing feature for this.
"Our imaging system was unusual in that it was made out of all cylinder lenses because of this high aspect ratio line—very long by very narrow. There are subtleties involved in designing with cylinder lenses that don’t appear with systems that use spherical lenses," Karlsen said.
Optical module close up
nLIGHT made a couple of different lens assemblies. Karlsen noted that "Very high-tolerance lens design of individual lens components was critical for us in making sure this whole project met all specs the first time around."
They also used the software to solve another challenge, which was that they needed to process extremely small pixels on a screen, so the laser needed to operate at very high power with incredible mechanical stability. It couldn’t move more than 10 micrometers.
Karlsen said the software helped add that stability. "To control that movement, you have to control the heat and the stray light. We had 7,000 watts going through this system, and every optical surface, every lens reflects a little bit of light. That lights goes somewhere and heats up some mechanical part. When something heats up it thermally expands, and thermal expansion leads to movement."
With OpticStudio’s non-sequential ray tracing capability, nLIGHT did a stray light analysis of the entire system, including all mechanical and optical parts, assessing how much reflection each surface would produce. With this modeling (see image at top), they figured out what parts would get warm, and that enabled them to take steps to control that heat—adding water-cooling or air-cooling capability. Some parts were plated with gold, since gold reflects light and stops it from absorbing.
They also used the non-sequential capability in designing the homogenizing system. It worked really well. Once we combined the 72 beams, those were launched into what’s called a light pipe, which is a glass rod.
The end product nLight delivered to the customer included a laser line generator, which consisted of an optical head for converting the 72 individual lasers into a single laser line, along with an electronics control rack. The optical head was about four feet long, two feet wide and two feet high. The control rack is about the size of a refrigerator, and it houses 72 100-watt laser modules, a cooling system, power supplies, and control electronics.
The feedback nLIGHT received from the customer was that it enabled a high-resolution process that allowed them to produce screen resolutions up to 1000ppi.
Written by Robyn Landis of Zemax after interviewing Scott Karlsen an Optical Engineering Fellow at nLIGHT.