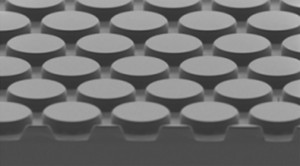
While Vertical Cavity Surface Emitting Lasers (VCSELs) have been used in data communications for over 20 years, there are a host of emerging applications that are boosting demand for VCSEL production and performance. These include less well-known applications such as infrared illumination/heating and atomic clocks, to better-known proximity sensing for automotive safety, high-resolution video display, and gesture/facial recognition.
Generally, the advantages of VCSELs over alternatives like edge emitting lasers (EELs) and light emitting diodes (LEDs) are low cost and optical efficiency, within a small footprint. VCSELs also have the advantage of wavelength stability over temperature and are directionally focused to maximize output efficiency. As VCSELs are top-emitting (as are LEDs), they can be tested on-wafer, integrated with simpler optics and mounted as dies on printed circuit boards, or integrated with a laser, driver, and control logic all within the same package. Power output, while less than EELs, is scalable by creating arrays of individual VCSELs.
Applications driving demand
A number of high-end smartphones from different suppliers (e.g., Apple, Samsung, Huawei, Xiaomi and OPPO) now incorporate VCSELs in 3D sensing applications, in front-facing (screen side) and/or world-facing sensors. Such mobile and consumer applications are the largest drivers for volume manufacturing of VCSELs, with a smaller yet growing demand from automotive and industrial markets. Market researchers[1-2] forecast the global VCSEL market will grow at a CAGR of 17 to 31% over the next 5 years.
Another application that is currently driving much research and product development is the use of VCSELs in light detection and ranging (lidar), which is a technique for monitoring relative distances and movement, essential for the development of autonomous vehicles. Lidar works in a similar way to radar but emits pulsed light instead of radio waves to reflect off surrounding objects. The time of flight for the reflected pulse to return to the lidar sensor is used to calculate the relative distance from the object. The shorter wavelength of the UV/visible/IR light (100nm -100µm), compared to the wavelength of radar’s radio waves (~1mm), enables detection of smaller objects and higher definition images.
VCSELs work well in short range applications like face recognition in mobile phones or driver attention monitoring in cars. However, longer range sensing needed for autonomous driving presents challenges due to the lower power output of VCSELs compared to other IR light sources. There have also been concerns about eye safety when using lower wavelength VCSELs at higher power to obtain long distance sensing. Eye safety involves a complex combination of factors such as power, divergence angle, pulse duration, exposure direction and wavelength. By tailoring the VCSEL’s wavelength using a short pulse, and optimizing optical detection, eye-safe long-distance sensing using arrays of low-power VCSELs is achievable.
VCSEL manufacturing
A VCSEL is created from a complex multilayer structure deposited onto the substrate by Molecular Beam Epitaxy (MBE) or Metal Organic Chemical Vapor Deposition (MOCVD). The epitaxial layers include an active layer that produces the photons, sandwiched between two distributed Bragg reflectors (DBRs) that act as mirrors to reflect the light back and forth through the active area multiple times to amplify the signal. Each DBR is made up of many epilayers in mirror pairs (typically >20 pairs), with the refractive index and thickness of each epilayer tailored to induce constructive interference to create light waves at the desired wavelength.
An aperture can be created to confine the current into a small area of the active layer by selective ion implantation or oxidizing certain epitaxial layers. For example, in the case of GaAs-based VCSELs, AlGaAs layers are partly oxidized to create a non-conductive region around the aperture. This concentration of current flow lowers the threshold current to produce laser emission and controls the beam width.
Critical wafer processes for volume manufacturing of VCSELs
Inductively coupled plasma (ICP) is used to etch either vertical or tapered mesa structures forming the VCSEL. The key requirement for next generation VCSELs is a smooth etch, with no sidewall damage or preferential etching of any of the layers. An uneven sidewall can lead to optical losses from the side of the VCSEL. An optimally smooth profile is difficult to achieve using wet etching, which is isotropic in nature and can lead to notching into the epi layers. Dry ICP etching is more directional and can be tailored to result in a much smoother profile. Accurate control of etch depth is critical to VCSEL performance, and in volume production applications accurate end-point detection is achieved using either fringe counting by laser interferometry or Optical Emission Spectroscopy (OES).
Plasma Enhanced Chemical Vapor Deposition (PECVD) is used by VCSEL manufacturers to deposit silicon nitride layers of the highest quality. The most critical application is an anti-reflective coating that improves laser performance by maximizing the optical output from the cavity. Here, the lowest possible non-uniformities of thickness and refractive index are required. Silicon nitride is also used to provide sacrificial stress compensation layers that minimize the bow and warpage of thinned substrates, and also passivation and hard mask layers.
Physical Vapor Deposition (PVD) technology is used to deposit TiW/Au seed layers and Au for contacts that supply the current or aid heat dissipation from the front side of the device. PVD layers with tailored stress properties can also be deposited to compensate for wafer stresses, which would otherwise cause warpage once a wafer is thinned and debonded from a carrier.
Since the second half of 2016, SPTS has experienced a surge in demand for its wafer processing technologies for VCSEL manufacturing. Manufacturers are choosing SPTS’s Omega etch, Delta PECVD, and Sigma PVD solutions because of their accurate processing capabilities, extensive process libraries, and SPTS’s years of experience serving customers in volume production of related technologies and products such as GaAs RF devices and LEDs.
Written by Dave Thomas, Ph.D. Senior Director, Etch Product Management, SPTS Technologies, A KLA Company
References
[1] “Vertical-Cavity Surface-Emitting Laser (VCSEL) - Market Analysis, Trends, and Forecasts” Global Industry Analysts Inc, Oct 2019 (www.strategyr.com/market-repor...try-analysts-inc.asp)
[2] " VCSELs – Market and Technology Trends 2019" Yole Développement, May 2019 (yole-i-micronews-com.osu.eu-we...CSELs_2019_flyer.pdf)