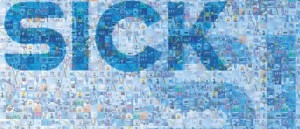
Flexibility is essential when it comes to manufacturing processes. As automotive manufacturing and other areas of manufacturing continues to expand rapidly, finding the right sensor solutions to enhance processes has never been more important. At Automate 2022, SICK showcased numerous solutions that excel in high-productivity environments. This includes digital twin and 3D safety concepts, part localization for bin picking, and LiDAR localization solutions for AMRs.
Digital Twins for Safe Machinery
This year at Automate, SICK showcased how you can keep things safe in your facility using our virtual reality safety services demonstration. As many know, safety solution designs and turnkey installations on manufacturing equipment can often be complex difficult to engineer or install. SICK explained creating a 3D safety concept that is a digital twin of your machinery, showing a 3D safety concept in action, and how it can easily be tailored to your needs. A project like this allows for a preview of your safeguarding measures, efficient project communication with the SICK team, and fast implementation.
Using laser scanner technology with a 1cm accuracy, we gather point cloud data that can be used to design your technical protective measures, such as light curtains, laser scanners, muting sensors, and hard guarding. This way our 3D safety concepts can be more precise by defining critical mounting distance and guarding measurements in relationship to the relevant standards. The 3D safety concept offered by SICK Safety Services team allows for optimization of the safety solution to achieve the highest possible productivity while also keep personnel safe and compliant to current relevant standards. We call this safe productivity.
Part Localization for Bin Picking
With the boom in manufacturing, throughput needs to scale up. A wide variety of items need to be handled at high speed. Floor space and worker availability are limited resources. This is when fully automated picking robots can step in to increase pick-and-place accuracy and speed with a 24/7 uptime and a small footprint.
SICK displayed its high precision robot guidance system for localizing items to be picked. A high-resolution, high-speed camera detects a wide range of objects of different shapes and colors. The robot has automatic detection of all kinds of objects and colors, even in challenging applications with reflective and shiny objects. It can localize items in multiple bins and has a highly accurate picking rate due to a high-precision 3D point cloud.
In addition, the robot provides machine learning and AI solutions that allows for it to be trained for new scenarios using dStudio from SICK and the classification of a wide range of objects.
Localization of Autonomous Mobile Robots
At Automate, SICK displayed solutions for autonomous vehicles and mobile robots, including our latest LiDAR Localization technology. Assets in a factory can be tracked continuously using localization solutions and their space-time coordinates can be continuously recorded and stored. Having this data means complete transparency about all the important movements on the warehouse floor. Today's analytics tools can already use this data to make connections between different events, presenting an unfiltered look into actual production processes.
All the established technologies—ultra wide-band tags, LiDAR Contour Mapping, line guidance sensors, infrastructure sensors—record either their own position or the position of the desired objects. Depending on the application as well as the positioning accuracy and update rate required, the right technology is selected, or various technologies are combined with each other.
Localization technology is one of the key factors in achieving the type of networked production needed for digital transformation. It can be used to boost optimization potential in several areas by allowing for agile planning of production processes. Localization data gives companies a high level of transparency and understanding of all production-related assets, load carriers, and loading equipment. Travel paths can be optimized and adapted dynamically, and setup times can be prepared or scheduled flexibly. The material flow can be planned and controlled based on consumption, boosting delivery quality and on-time delivery.