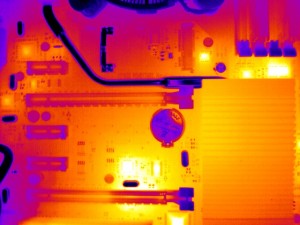
While traditional cameras rely on visible light to capture images of what they “see,” infrared cameras generate images that depict the invisible energy or heat of objects. Every object emits thermal radiation, and the warmer an object, the more it stands out against cooler backgrounds in a captured infrared camera image. With applications in everything from food production to healthcare to security, the infrared camera market will be valued at $6.82 billion by 2023, according to Global Market Insights, Inc.
Infrared cameras operate in three wavelength bands—short wavelength infrared (SWIR), medium wavelength infrared (MWIR), and long wavelength infrared (LWIR)—using electromagnetic energy between 0.7 µm and 15 µm wavelengths to detect heat and generate an image. Of these, LWIR, which is electromagnetic energy between 5 µm and 14 µm, is most commonly used in infrared camera technology. (Both SWIR and MLIR cameras have some application in science and industry, but special requirements; most often for cost, size and cooling, limit their use.)
Unlike optoelectronic camera technology in which the quality of images can vary based on the amount of ambient light around a scene, LWIR cameras depend on the content of the scene and the temperature of the objects to ensure the quality of an image. In addition, LWIR cameras can work at a variety of ambient temperatures, and microbolometer-based LWIR cameras (see below) don’t require special cooling to function.
It begins with a microbolometer
Visible cameras work with optoelectronic sensors, which detect and control light to capture an image. Since most objects don’t emit visible light at normal temperature, this process is greatly influenced by ambient light and external sources.
Infrared cameras measure heat using microbolometer technology, sensitive electrical detectors that process infrared radiation into temperature ranges to create grey scale or color images. Each pixel of information within is made up of a comparison between two heat-sensitive resistors, one of which is exposed to the LWIR light emitted in a scene and one which is not. These resistors are encapsulated in a vacuum to shield them from thermal conduction or convection, isolating them from their environment. The image generated is based on the temperature variation between the exposed and unexposed resistors.
The disparity between the two resistors causes fixed pattern noise (FPN) in the image, jeopardizing image quality. Even if the camera can detect and correct the FPN, with any changes in ambient temperature the disparity, and hence the pattern, can reappear. Usually, FPN is corrected through a “shutter action” using the shutter in the camera, but this added mechanical assembly with moving parts is sometimes inconvenient, driving a demand for shutterless alternatives.
Shutterless cameras rely on dynamic correction to address fixed pattern noise in an image, accounting for disparities in substrate temperature by predicting and applying the right amount of correction per pixel. Dynamic correction also considers the heat distribution around the camera itself, including the casing and lenses, at a given ambient temperature to limit fixed pattern noise.
In addition to the elimination of shutter movement that can impact the positioning of the camera—and image quality—shutterless cameras also deliver image output that remains stable across time and a temperature range; there is no interruption for recalibration. With no shutter, there are also no frames and the camera is never “blinded”; subjects can remain in view consistently. Plus, shutterless cameras can be less complex to operate, are less prone to mechanical failure, and can be manufactured in a much smaller form factor and lower weight.
When knowing relative temperature isn’t enough
LWIR thermography cameras rely on relative temperature information, or how warm an object is when compared to other objects in the scene; the specific temperature of an object isn’t calculated. For some applications, more data about the actual temperature of the object—or even the actual temperature of each part of an object—is needed. LWIR radiometric cameras can provide this level of refined temperature measurement.
LWIR radiometric cameras work by measuring the total radiance emitted from objects in a scene over a period of time, down to the energy absorbed by each individual pixel, to determine absolute temperature. These cameras also assess variables such as the distance from the object and the ambient temperature and relative humidity of the surrounding environment, and then use an algorithm to calculate the temperature of each point. This data is translated into the image.
Long wavelength infrared cameras in action
Both LWIR thermography and radiometric cameras have applications in a range of industries. For example, LWIR thermography cameras have commonly been used in search and rescue and other defense and security applications. With their ability to “see” through perfect darkness, fog, and smoke, these cameras now have exciting new applications anywhere automated piloting is required: in robots and drones, and even in self-driving vehicles.
For one power company, LWIR camera technology has simplified the process of identifying faults in power-line circuits and has ensured that these faults can be identified before a problem that can disrupt transmission occurs. A LWIR camera system, attached to a drone, is deployed along miles of power lines in all types of weather. The camera, which is shutterless, is able to take a continuous image of each line, and when this data is analyzed, the images display brighter spots in any place on the line where there is a problem and the temperature is higher than it should be. Teams can then prioritize issues and send line crews to address problem areas.
Similarly, in automotive production, a manufacturer might use LWIR camera technology to ensure that bumpers are tightly adhered to its vehicles. Bumpers are attached using a high-strength epoxy that is cured with heat, and because the strip of epoxy is located behind the bumper, it is impossible for assemblers to see.
Automotive application
This makes it challenging to be certain that the epoxy is aligned correctly and that the placement of epoxy is consistent. Using LWIR camera technology, the manufacturer can see how the epoxy is performing. When placed accurately, the epoxy appears in an LWIR image as a continuous strip of warmth.
LWIR radiometric cameras—which provide information about the absolute temperature of objects—are seeing expanded use in firefighting and fire prevention, identifying warm spots at faulty electrical junctions in walls for example. In healthcare, these cameras can help identify infections, monitor blood flow, or even tell from a distance if a person has a fever.
Healthcare application
In particular, radiometric LWIR cameras are gaining widespread acceptance in food production. In one example, a fruit producer determined that it was easier and less damaging to pit a piece of fruit once it reached a certain temperature. Before the integration of an LWIR camera in the production process, it was challenging to detect manually when a piece of fruit was warm enough to pit, but not so warm that it would be damaged by overheating. Today, fruit is tumbled in a warming oven, and as LWIR camera technology identifies that each piece has reached the appropriate temperature, it triggers the system and the fruit is sent down a shoot to the pitting phase of the process. Pitting is completed more quickly overall, and the producer sees less waste in the new process.
The potential for long wavelength infrared cameras is limitless, bounded only by the imagination of camera users, and the use of this technology is sure to surge as camera performance improves, the size of cameras shrinks, and the technology becomes even more affordable.
Written by Jean Brunelle, the technical leader, Sensor Integration, for Teledyne DALSA.