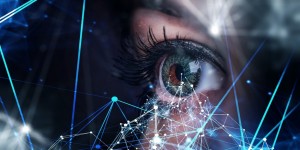
A burst of technologies is reshaping our lives, and these include AR, VR, lidar, autonomous driving, 3D technology, multiple interconnected devices, and intensive software. The common denominator for all these technologies is photonics, more specifically systems integrating lasers, cameras, lidar, sophisticated mechanics, optical elements and image projecting devices. Those all-in-one coming devices require a production line capable of fast measurements with high accuracy of the inter-relationship and accuracies between each sub-component. Typical measurements for which the new Total Station is particularly suitable are:
- Inter-alignment between lasers, the system optical axis and projecting screens of cameras.
- Measuring laser arrays (VCSELs) projection.
- Measuring mechanical axis relative to optical axis.
- Measuring lidar and their angular array distribution
The technology merges multiple instruments into one single Autocollimator, thus opening new horizons to achieve very high measurement performance of complex multi-component systems. The new Autocollimator is a Total Station Autocollimator device.
The multi-tool electronic total station autocollimator
In modern scientific and industrial laser applications, co-alignment between mechanical sub-components, optical devices, laser beams and cameras is often a real contest.
Traditionally, performing such a measurement requires multiple instruments such as Electronic Autocollimator, micrometers, laser beam profilers and various high precision mechanical bits and pieces. To make things even more challenging, usually the required co-alignment embraces multiple wavelength bandwidths. To offer an accurate touch-free system for this intricate co-alignment we merged multi-tooling into one system based on an Electronic Autocollimator. The integrated tools in this platform are: Autocollimation, beam profiling, a focusing telescope with accurate image processing and capability of measuring mechanical deviation from remote. The system also includes a target based on an illuminated reference cross.
Thus, we developed an Electronic Autocollimator and transformed it into a multi-tool device, capable of full alignment of complicated systems, operated by a dedicated software package that also produces alignment reports.
Next, we will discuss typical applications including laser optical sights and mechanical requirements and we´ll demonstrate the measuring method.
The use of multiple-sensors integrated into one advanced autocollimator as an alternative to conventional use of several individual measuring instruments is enabling such complicated alignment or measurement tasks that it can solve many problems in day-to-day applications. The upgraded device uniquely offers a laser beam profiler integrated into an autocollimator measuring capability. This is complemented by motorized focusing of the autocollimator, which also operates with wavelengths from UV to NIR and beyond. All the optical elements including multiwavelength sources are precision mounted and the entire instrument is rugged and stable, providing accurate beam pointing and robustness for various applications. By maintaining the alignment of the beam profiling device with the autocollimator´s line of sight, a new application field is available for integrating and aligning lasers with optical elements and telescopic sights. Moreover, by integrating multiple independent beam profiling measurements from one sensor, a leap forward is achieved for measurements of VCSEL arrays and their alignment to specific optical assemblies.
At first glance, the multitask autocollimator looks similar to its predecessor, but its sensory system has been greatly upgraded as follows:
- A dual-purpose camera sensitive from deep UV to NIR is used as an autocollimator sensor, as well as a beam profiler.
- Multisource illumination can project a cross line with different colors to create multiple crosses, adaptable to specific needs.
- The motorized, computer controlled focusing automatically adapts itself to compensate for the differences created by the projection of various wavelengths.
- By selection in the operation software, the autocollimator transforms itself into a beam profiling telescope, accepting various laser beams to be analyzed for direction and divergence.
- Yet another functionality created by the software enables accurate measurements of a laser´s M2 numbers
- The motorized focusing allows the autocollimator to focus at pre-calibrated distances, controlled by software and the system can project imaginary targets for focusing of external cameras and laser devices.
- A built-in alignment laser points a line of sight in a clearly observable direction, facilitating fast and accurate alignments.
Applications in practice
Today's rapidly growing markets for gesture and facial recognition, as well as autonomous vehicle and 3D scanning applications create an interaction between electronic systems, mechanics and optics thus generating demand for new power tool devices. While alignment and measurement could be performed with current technologies, an integrated device offering multi-task accurate measurements of all sub-systems will perform faster and better inter-alignment.
Figure 2: Inter-alignment of LoS for VCSEL array and external camera (Source: Duma Optronics)
Occasionally, for those applications a need arises to align between a camera system and a laser system such as a typical collimated VCSEL array, as well as mechanical positioning and straightness for scanning applications. The scheme in Fig 2 demonstrates an application wherein a camera and a VCSEL device are coupled together via a Beamsplitter, and the necessary alignment axes are drawn each having a linear mechanical requirement as well as an angular specification around this linear direction.
Figure 3: Inter-alignment of LoS for VCSEL array and external camera using the Total Station Autocollimator (Source: Duma Optronics)
Typical co-alignment requirements for this setup will be:
- Concentricity between VCSEL optical setup and camera setup (each at a different distance from the Autocollimator).
- Characterization of the laser projector individual laser beams and total concentricity of the system.
- Alignment retainment of carriage as a function of distance in all directions.
- Optical devices mounting accuracy in respect to the beamsplitter's front surface.
- Testing at various wavelengths.
- Testing focusing distance of camera or VCSEL assembly from 2.5 meters to infinity.
Figure 5: Typical screenshot demonstrating lateral measurements using the Autocollimator, which is 334 mm away from the measured plane. Deviation in X & Y directions are displayed in mm, with micro resolution. (Source: Duma Optronics)
Upgraded and modernized to serve for years to come
A hundred year old technology that used to be the cornerstone of the optical laboratory was modernized and upgraded to create a Total Station Autocollimator to serve the modern industry for a long time to come.
Written by Oren Aharon, the founder of Duma Optronics.