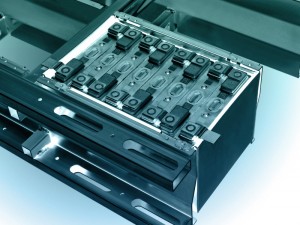
In the future, manufacturers of electric car batteries could further improve the durability and performance of electric car batteries with compact X-ray sources. The XProLas development partnership has now started to develop these laser-driven X-ray sources under the leadership of TRUMPF. The first demonstration systems are to be built by 2026.
The future goal is for manufacturers to be able to use these systems to monitor the charging and discharging of batteries in real time or determine impurities in the battery with particular precision. The findings will be incorporated into the development of new batteries. With conclusions drawn from the analysis, manufacturers will be able to improve, for example, charging speed. Until now, companies have only been able to carry out such investigations on large particle accelerators over 100 meters long. Research stations at these large-scale research facilities are rare. The laser-driven X-ray sources are only about the size of a mobile home and, as such, are cheaper to manufacture. Therefore, they are ideal for use in industry.
The high-tech company TRUMPF is contributing its expertise in the manufacture of lasers for industrial use to the partnership. BASF and Cellforce are providing battery materials and components for the tests. Ushio Germany and Excillum are contributing their expertise in the field of beam sources. Bruker and Viscom are responsible for the construction of the systems. On the academic side, the University of Hanover and the Fraunhofer Institutes in Aachen and Jena, Germany are the driving forces. The research budget amounts to around 15 million euros and the German Federal Ministry of Education and Research (BMBF) is funding the project.
X-rays for better batteries in electric cars
The XProLas development project also aims to create a compact, high-brilliance X-ray source for analyzing the cathode material of electric car batteries. The material from which the cathodes of electric car batteries are made is of central importance for the performance and reliability of electric vehicle batteries. The exact composition of the cathode material can only be determined using X-rays. The compact, laser-driven variants can also replace large-scale research facilities in this field of application. Manufacturers of cathode material can thus speed up their development work.
The laser serves as a so-called upstream beam source in the generation of X-rays. The laser pulse hits the so-called target, a metal such as gallium, indium or tin. A plasma is created; this plasma emits some of the energy as extremely short-wave light, for example X-rays.
X-ray light generated by a laser to inspect core components of electric cars // Laser technology enables particularly brilliant X-ray sources for use in industry
Ditzingen, Germany, February 29, 2024 – In the future, manufacturers of electric car batteries could further improve the durability and performance of electric car batteries with compact X-ray sources. The XProLas development partnership has now started to develop these laser-driven X-ray sources under the leadership of TRUMPF. The first demonstration systems are to be built by 2026. The future goal is for manufacturers to be able to use these systems to monitor the charging and discharging of batteries in real time or determine impurities in the battery with particular precision. The findings will be incorporated into the development of new batteries. With conclusions drawn from the analysis, manufacturers will be able to improve, for example, charging speed. Until now, companies have only been able to carry out such investigations on large particle accelerators over 100 meters long. Research stations at these large-scale research facilities are rare. The laser-driven X-ray sources are only about the size of a mobile home and, as such, are cheaper to manufacture. Therefore, they are ideal for use in industry.
The high-tech company TRUMPF is contributing its expertise in the manufacture of lasers for industrial use to the partnership. BASF and Cellforce are providing battery materials and components for the tests. Ushio Germany and Excillum are contributing their expertise in the field of beam sources. Bruker and Viscom are responsible for the construction of the systems. On the academic side, the University of Hanover and the Fraunhofer Institutes in Aachen and Jena, Germany are the driving forces. The research budget amounts to around 15 million euros and the German Federal Ministry of Education and Research (BMBF) is funding the project.
X-rays for better batteries in electric cars
The XProLas development project also aims to create a compact, high-brilliance X-ray source for analyzing the cathode material of electric car batteries. The material from which the cathodes of electric car batteries are made is of central importance for the performance and reliability of electric vehicle batteries. The exact composition of the cathode material can only be determined using X-rays. The compact, laser-driven variants can also replace large-scale research facilities in this field of application. Manufacturers of cathode material can thus speed up their development work.
The laser serves as a so-called upstream beam source in the generation of X-rays. The laser pulse hits the so-called target, a metal such as gallium, indium or tin. A plasma is created; this plasma emits some of the energy as extremely short-wave light, for example X-rays.