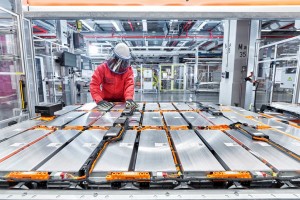
The opportunity for green energy to grow is endless . . . and necessary. According to U.S. Federal Energy Regulatory Commission (FERC), renewable sources of energy will grow to 27% of the country’s capacity by 2023, led by new wind and solar installations. In addition, the evolution of the power grid will require the development and maturation of new supply chains and processes, such as the increase in the production of lithium-ion batteries.
With governments, private industry, and consumers all seeking energy sources that are greener but still affordable, solar cell and wind turbine manufacturers are under pressure to increase the quality of their products and reduce costs. And if the world is going to have a chance of reaching zero carbon emissions, rechargeable batteries will be a critical part of the solution. This article will explore how vision inspection technologies have a vital role in making green energy successful.
Solar Panels
Despite the supply chain disruptions in the underlying components caused by the COVID-19 pandemic, solar energy represents the second-largest absolute generation growth of all renewable technologies, slightly behind wind and ahead of hydropower. According to International Energy Agency’s World Energy Outlook 2020, no other power-generation technology has matched the pace of solar power this past decade, resulting in the “cheapest…electricity in history”; cheaper than coal and gas in most major countries.
Automation and inspection are both critical to high-quality, consistent, and high-throughput solar panel manufacturing. There are delicate components and multiple layers, all requiring precise placement and alignment. Material handling, cell cutting, and component bonding are all very automated in modern factories, but an error in any one of these risks lower initial performance and shorter operational life for each solar panel.
This makes inspection crucial. End-of-line testing of electrical parameters like current voltage and peak power rating ensures that panels perform at expected standards. Imaging allows us to look for quality issues, such as cracks and misalignments that indicate initial quality, but also longevity of the panel itself in the field.
Like many areas of electronics manufacturing, leading manufacturers have already moved to 100% inspection and the rest of the industry is working to catch up. Optical inspection becomes required after every major processing step. Machine vision is a key tool that manufacturers use to improve product quality and production efficiency while increasing the pace of products produced to meet demand. The challenge is detecting these tiny imperfections that are not yet problems but will cause failures, yield reduction, and material damage down the road.
In addition to manufacturing, solar energy relies on preventative maintenance of the Photovoltaic (PV) modules (solar panels or cells), which can be aided by thermal imaging inspection. While the panels just sit in the sun gathering energy, the largest solar farms in the world require continual monitoring, calibration, and repair. The largest solar power plant in the U.S. is called Solar Star and resides in the Mojave Desert in Rosamond, California, about an 80-mile drive north of Los Angeles. The 579-megawatt plant consists of 1.7 million solar panels spread across 13 square kilometers. Manual inspection of each panel across such a large space would require a prohibitive amount of effort.
Instead of manual inspection, companies are turning to automation to ensure panels are receiving light at peak efficiency. An aerial drone equipped with infrared or electroluminescence cameras combined with machine learning algorithms can cut inspection time in half.
Wind Turbines
Wind turbines are massive machines, often the equivalent of a 32-story building from the base to a blade at the apex of its rotation. The blades can be up to 120 feet long and move between 10 and 20 revolutions per minute. These majestic machines are serious business with each blade on the turbine costing up to a million dollars.
Thus, keeping turbines in good working order is essential for efficient energy production, but also for the safety of humans or animals within a turbine’s immediate vicinity. If the blades of a turbine become damaged, or spin too fast because a brake or gear mechanism is damaged, a blade can snap from the turbine and cause significant, life-threatening damage.
The old method of inspecting turbines involved a team of people climbing up the tower and dangling down the sides of the blades for manual visual inspection. The process could take three days to inspect one turbine, a period when the machine is not producing energy. These days the process is not so onerous with the combination of thermal imaging equipment and aerial drones allowing engineers to inspect a single turbine in less than an hour.
A general rule for machines is that components will increase in temperature when they are about to break. In a machine with moving pieces, increased friction creates heat that could be the first sign that a part is about to break down.
Defects in the blade can change its thermal signature, which can be detected with infrared imaging, even while the blades are in motion. Thermal imaging can detect possible defects, such as splits or internal problems, that wouldn’t register with a manual visual inspection.
Thermal imaging for preventative maintenance of wind turbines can allow operators to repair or replace components before a failure occurs, while also detecting precisely where the problem is. Over the course of its lifetime, operating and maintenance costs can make up 20 to 25 percent of the total cost of electricity produced by the turbine. Thermal imaging via aerial drone is quicker than manual inspection, requiring no direct contact with the turbine, and can scan large areas.
Investing in preventative maintenance for wind turbines renewable energy sources to scale more efficiently in the coming decades as the power grid continues to move away from fossil fuels.
Lithium-ion Rechargeable Batteries
Developed in the 80s and 90s, lithium-ion batteries (LIB) made their first big impact on mobile devices: smartphones, tablets, cameras, and power tools. Their high energy densities and voltage, stability, low weight, long life cycle, and diversity of chemistries make them groundbreaking, so far ahead of previous rechargeable battery technologies.
Today, consumer electronics represent only 20% of the demand for LIB. The future for LIB will be in driving the global transport and energy systems to electric power and enabling a more decarbonized future for humanity. According to the World Economic Forum, passenger cars will account for 60% of global battery demand by 2030. Electric vehicles (EVs) are transforming the automotive and transportation industry and are expected to account for most of lithium-ion battery demand.
Still, there are risks. LIBs are complicated to make, especially for EV applications where safety, durability, and modularity compete with competitive pressures on performance, efficiency, and price.
The best quality strategy is to start inspection of batteries as early in the production process as possible, so as not to waste time and resources on scrapping or recycling nearly finished product. Early defect detection allows manufacturers to fine-tune the feedback loop, adjusting process machinery to optimize results.
Often, it’s a matter of a few dark grey defects on a dark grey background that can determine the performance and lifetime of a battery cell. Manufacturers are finding it important to look for these defects from the 50-micron level all the way down to 10 microns. Contact imaging is often used for a ‘rough’ initial pass, but for detailed inspection further down the line, companies turn to line scan cameras, and high-sensitivity TDI (Time Delay & Integration) cameras to provide the necessary resolution and sensitivity.
More innovative solutions have included Multi-Field TDI cameras that provide the additional benefit of simultaneously capturing light from three different spectra and angles, providing more image data for defect detection and analysis without incurring further costs or slowing the system.
Other types of imaging are used at different stages of assembly. High-speed 3D laser profilers are used to measure the form of more 3-dimensional objects such as the contact tab welding uniformity, tab deformity, and orientation. A poorly welded contact tab can break or cause an intermittent loss of contact. Area scan cameras are used primarily in the packaging of individual cells into larger batteries, where the orientation of hundreds of cells in the housing must be precisely controlled.
Today, and for the foreseeable future, the hurdle for LIBs will continue to be manufacturing reliable, high-quality cells in the face of constant optimization and the fluctuations of a global supply chain.
Keeping it green
New green technologies are driving the future of clean energy for the next century. Inspection is helping us keep up and will allow renewable energy sources to scale more efficiently in the coming decades.
Written by Gerard White, a Senior Business Development Manager at Teledyne DALSA.