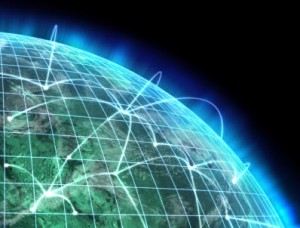
Fibre optic proof testing is a commonly used and convenient method to ensure the mechanical strength and long term reliability of a stripped and spliced optical fibre. While it is quite easy to obtain a low loss splice joint today with modern equipment, strong splices with high long term reliability are much more difficult to create. From a systems perspective, the reliability of fibre fusion splices are therefore mainly determined by their mechanical strength degradation.
Two types of tests
When an optical fibre is proof tested, a carefully determined tensile load is applied onto the fibre for a certain set period of time. Most commercially available proof testing equipment allows the user to control the pulling speed during ramp up as well as the hold time at maximum force. More specifically, two types of tensile strength tests can be performed. First, proof testing can be employed as part of the quality testing in an industrial manufacturing process. Within telecommunication, various standards bodies have published detailed fibre strength requirements. Force levels should correspond to the maximum tensile load that the fibre will likely experience during its lifetime, with a certain safe margin added (without affecting the production yield adversely). Secondly, breaking strength tests, destroying the fibre under inspection, can also be performed as part of process verification. During these tests a high level of force is applied and the level achieved at the moment of breaking is displayed. Mandrels instead of linear clamps are often used to prevent the fibre from slipping, since force levels up to 70 N are sometimes required to break very strong splices of standard telecommunication fibre.
Proof testing can be employed as part of the quality testing in an industrial manufacturing process.
Proof testing, both destructive and non-destructive, has become an integral part of what is commonly called the “high strength splicing”concept. High strength splicing means not only that the optical loss should be minimized, but that as much as possible of the original fibre strength should be preserved through the splicing process. Much attention is therefore paid to the fibre preparation process, since improper handling and stripping is s common cause of mechanical fracture, and also to fibre post-processing and splice protection. Restoring the coating on the stripped and spliced fibre is one of the last steps of the high strength splicing process and proof testing functionality is commonly integrated in fibre optic recoating systems, like those from Nyfors Teknologi AB. Recoating should be performed prior to testing in order to ensure that the fibre strength has not been affected.
Nyfors Teknologi Fibre Optic Proof Tester
Predicting the lifetime
Mechanics in combination with statistics can be used to calculate the probability of failure and thus predict the lifetime of a splice joint under a known and constant level of tensile stress, something which may be useful when dealing with components that are expected to last for long periods of time as parts of fibre optic systems operating under harsh conditions. Undersea optical fibre cabling is perhaps the most illustrative case at hand. Submarine cables are subject to very high tensile load during initial deployment when they are suspended from a cable ship, and the cost of repair is significant, since this involves recovering the cable from the seafloor. For this reason, proof testing requirements for undersea cables are significantly higher than for terrestrial fibre optic telecommunication cables. A similar case, but with constant tensile loads, is when a spliced fibre is tightly coiled around a spool in e.g. fibre optic gyroscopes.
Breaking strength tests, destroying the fibre under inspection, can also be performed as part of process verification.
A subject of some discussion within the research on this field has been the effect of the proof test itself on the mechanical strength of the fibre, to what extent the procedure compromises the integrity of the splice joint. It has been shown that a splice surviving a proof test may have a mechanical strength below the applied tensile load, for reasons that have to do with stress corrosion weakening the fibre during unloading, but the practical implications of this are limited. For most applications fibre optic proof testing is a fast and cost efficient way to check production quality in fusion splicing operations, to ensure that high mechanical strengths accompany low optical transmission losses.
Written by Johan Gribbe of Nyfors Teknologi AB, a specialist in fibre preparation equipment for high-strength splicing and glass processing operations based in Stockholm, Sweden