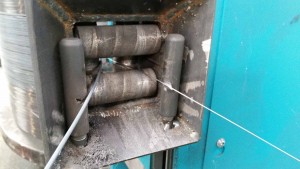
Virtually every manufacturing sector, from heavy equipment to microelectronics, is pursuing the same overarching goal of reducing production costs while simultaneously improving yield and final product quality. Lasers are powering this trend in many industries because of their ability to perform highly precise, non-contact processing. Cladding, in particular, is a process that achieves these ends; this article explores how one Austrian company has implemented a Coherent laser system for cladding of industrial metal parts.
Cladding improves performance and lowers cost
The choice of substrate material for a part invariably represents a compromise between its bulk and surface properties, as well as its cost. For example, it might be desirable to fabricate an engine crankshaft from a material that is sufficiently flexible so that it doesn’t fracture when exposed to high torsional stress. However, it would also be advantageous if the bearing surfaces of this crankshaft were very hard, so that the part would not wear quickly in use.
Cladding is a process that enables independent choice of the bulk and surface properties of a material; thus avoiding this type of compromise. Specifically, cladding involves the creation of a new surface layer on a substrate having a different composition than the base material. For example, it enables a fabricator to utilize a low cost material for the bulk of a part, yet still selectively achieve the wear, corrosion or heat resistance properties of a more expensive alloy. Furthermore, cladding cuts costs in many industries by enabling economical refurbishment of high value parts, rather than expensive replacement.
Cladding technology
The most common traditional methods for metal cladding are all variations on arc welding. In these processes, an arc is established to melt the surface of the base material to a shallow depth. The clad material is then introduced in either wire or powder form and is also melted by the arc, thereby forming the clad layer.
Typically, arc welding techniques deliver a fully welded, metallurgical bond having high strength, good impact properties and low porosity. However, the high heat input into the part usually melts enough of the substrate produce a significant amount of mixing of the base material into the clad layer. Such dilution is undesirable because it alters the very properties for which the clad material was selected. Also, the high heat input can cause mechanical distortion, creating the need for further processing after cladding to restore the part’s dimensional accuracy.
Using the laser as the heat source offers an attractive alternative to arc welding, because the laser can produce the required heating in a highly localized and controlled manner. By melting very little of the bulk material, laser cladding dramatically reduces dilution in the clad layer, while still producing a true metallurgical bond. Also, the lower heat input avoids part distortion, largely eliminating the need for post-processing.
High power diode lasers are a particularly good match for the needs of high speed, large area cladding applications. This is because they produce high output powers (up to 10 kW), at near infrared wavelengths that are well absorbed by most metals. Furthermore, the output of a high power diode laser is typically a long, thin line beam (e.g., 1 mm x 24 mm). This beam shape can be swept over the part to enable rapid processing of large areas with a high degree of control over clad width, thickness and deposition rate.
Cladding at Castolin Eutectic International
Castolin Eutectic International, Wiener Neudorf, Austria, provides surface protection, repair and joining solutions for industrial parts. The company recently developed a large frame laser cladding system for hard facing, cladding, and surface treatment applications, primarily for customers located in Austria and Germany. Their tool is based on a Coherent HighLight 10000D (10 kW diode laser), which can be configured to have an output beam width of 6 mm, 12 mm or 24 mm.
In the laser cladding system developed at Castolin Eutectic International, a Coherent HighLight 10000D is mounted on a large gantry, enabling cladding of parts up to 5m in length.
One representative application at Castolin involves cladding fan blades for ventilation systems used in the cement industry. Typically, the environment in which these fans operate contains a substantial amount of airborne abrasive cement particles, which can rapidly wear the blades.
Cladding allows the fan blades to be produced from a relatively lightweight alloy, yet still have excellent wear resistance properties. However, it is important that the cladding process does not deform the blades; the fan must operate properly under rotation.
Cladding makes fan blades more durable, but it is important that the process does not induce distortion, otherwise expensive rework will be required.
The wide beam from the HighLight laser enables rapid cladding of these steel fan blades with a 1 mm thick layer of LC8, and doesn’t produce any part distortion. This wasn’t true of the arc welding process used previously.
Another cladding application at Castolin involves treating the rollers used in wire drawing equipment. In use, wire is drawn rapidly over the rollers. This action creates cuts in the rollers, and rapid wear. Laser cladding improves the wear resistance of these rollers, without adding significant cost.
In this instance, the 30 mm diameter rollers are produced from structural steel (S235) pipe. Castolin employs their laser cladding system to deposit a 1.5 mm thick layer of Laser LC 8 alloy (a steel alloy containing nickel and a high content of tungsten carbide) around the entire roller circumference. Moreover, the long travel gantry of the Castolin machine allows them to clad large sections of pipe, which can then be cut to length as needed by the wire drawing machine builder. Castolin’s diode laser cladding process has proven to extend roller lifetime by a factor of over five times compared to the previously used heat treating process.
In summary, cladding is one of the ever growing list of laser enabled or enhanced applications that are lowering costs in numerous industries, while improving performance.
Written by Frank Gäbler, Director of Marketing, Coherent Inc.