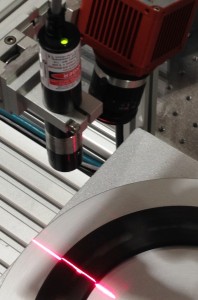
Applications for quantitative, three-dimensional (3D) machine vision/inspection are currently growing at a very healthy pace, with laser triangulation often the preferred choice of technology to quickly verify fit, form and function in a cost-effective way. It is used to monitor key components and key processes across a broad spectrum of industries.
There are several drivers behind this growth. One is to reduce manufacturing costs by improving product consistency while optimizing workforce headcount. Specifically, this means increasing efficiency and automation in product assembly, functional testing and final inspection. Another factor is the push to decrease costs by reducing scrap. A standout example is increasing the amount of usable timber when cutting raw logs in the lumber industry. Other examples are measuring extrusion processes for metal, rubber, and plastic components at the point of extrusion, thus immediately identifying quality issues and preventing the production of scrap product. Another example is monitoring tire treads (so-called green treads) before they are bonded onto sidewalls to make the final assembled tires.
Manufacturers are also trying to improve their perceived product quality and are creating an even stronger market force driving 3D inspection growth. Here, manufacturers of consumer products strive to maintain a high quality, high value, brand image in order to help differentiate their products and justify a premium price. This perceived value is directly affected by product cosmetics, including surface and edge roughness, and consistent, well-aligned and uniform seams for visible, joined parts. Examples range from the bonded seams in the cases of smart phone and tablets, to the gap between panels in automobile bodies.
For the fast growing “perceived quality” applications, laser triangulation, is often the preferred choice because it provides significantly higher spatial resolution.
The three most widely used technologies for 3D inspection are laser triangulation, time of flight optical sensors, and stereoscopic vision. Each has a place in the market. But, for the fast growing “perceived quality” applications, laser triangulation is often the preferred choice because it provides significantly higher spatial resolution.
Laser triangulation
Laser triangulation is able to make 3D measurements by projecting structured light patterns onto the object, which is then imaged with a conventional 2D array camera. A narrow bandpass filter at the laser wavelength is often used in front of the camera to maximize line visibility by blocking most of the ambient light. Figure 1 schematically illustrates a very simple example of how laser triangulation works to record a vertical (z axis) profile using parallax. Here a single line of laser light is projected across a 3D object. This line is then imaged by the camera. Providing either the laser or the camera (or often both) are oriented at non-normal incidence to the axis being profiled, then variations in the object height create pixel shifts in the camera-recorded line. Simple trigonometric algorithms can then automatically and quantitatively convert the image to a cross-section profile.
Laser triangulation enables 3D information to be recorded using a simple 2D camera.
Typically, laser manufacturers support this market with integrated, structured light products. An example is the Coherent StingRay series, in which the laser and various optics (refractive and/or diffractive), are integrated in a small, robust head suitable for use even in hostile, dirty production line environments. Product diversity is key for laser manufacturers because the optimum laser power and type, and the projected pattern, are all highly dependent on the application specifics. In off-the-shelf products, these structured patterns can range from a simple circular spot to a single straight line, to a pattern of lines, or a complex matrix of spots. Many applications use custom patterns tailored for highly specific tasks.
In terms of wavelength, the majority of applications still use red laser diodes as these provide the lowest cost and are an excellent match for silicon sensor based cameras. Currently there is a demand for laser modules ranging from the UV (375 nm) to the near-IR (830 nm). In terms of output power, most applications utilize output powers of < 250 milliwatts, and often just a few milliwatts. But some applications, particularly outdoor applications, require powers approaching 10 watts.
Light structure patterns requirements are equally diverse. For example, a single point is used to provide 2D information for objects on a moving production line. A single line is used to produce a 3D map of a moving part on production line or web. A multiline pattern is used to produce a 3D map of the same moving part, but it can do this X times faster, where X is the number lines. A single line or multiline pattern is also used for 3D applications where it is the laser that is moving relative to a stationary object, such as for inspecting road surfaces or rail wear in the railroad industry. And lastly, a complex pattern of dots and/or lines is typically used to perform static measurements with a single shot; to verify the overall part shape or orientation, rather than extreme dimensional accuracy.
In conclusion, the machine vision market continues to mature and diversify in order to support increasingly sophisticated and demanding inspection tasks. Supporting this trend means offering a wide range of options in terms of source output and projected patterns.
Written by Wallace Latimer, PLM Machine Vision, Coherent Inc.
Photo at top: Laser triangulation enables 3D information to be recorded using a simple 2D camera.