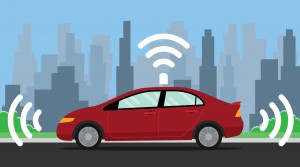
Lidar is enjoying a resurgence as autonomous vehicles leave the development lab and begin to hit the roadways. But lidar actually encompasses a much more varied range of applications and optical designs, each with their own unique optical coating needs.
Lidar technology first caught the public eye in 1971, when it was used during the Apollo 15 mission to map the surface of the moon. Since then, it has seen steady use in a wide range of applications, from airborne surface measurements for environmental, industrial, security, and urban planning to ground-based mapping of architecture, accident scenes, and other environments where a detailed, automated 3D surface map is needed. It’s been getting its biggest push in recent years, however, from the race to create autonomous vehicles, advances in visualization and gaming, and the need for unmanned reconnaissance in hostile zones. All of these applications call for an automated “eye” that does more than just capture an image – they need a precise 3D map of the view ahead, often in real-time.
What is lidar?
Lidar is a light-based analog to sonar or radar, often described as “Light Detection And Ranging” or “Light Imaging, Detection, And Ranging”. It is a method of measuring distance based on the time of flight of light. A light source (typically a laser) is swept across the field of view. Direct reflections from the surfaces it encounters are detected by a sensor, and since the speed of light is constant, the time delay of the round trip can be used to determine the distance to the object, building up a map of the field of view in 3D. The time of flight may be calculated directly or via range-gated imaging using a pulsed light source, or the light source may be modulated and the phase difference calculated via optical heterodyne detection.
Optical coating needs in lidar
As in any application looking at scattered light at a distance, sensitivity is paramount. Greater sensitivity improves accuracy and the ability to see low-reflectivity objects. It also facilitates the use of lower source intensities, increasing safety and reducing power consumption. Many lidar sensors operate in outdoor environments, however, necessitating the use of durable windows and optics with high transmission at the wavelength of operation.
Maintaining low reflectivity across a wide range of angles of incidence is key in lidar, as shown in this plot of reflectance with angle for an AR coating centered at 905 nm on a polycarbonate substrate. Image courtesy of AccuCoat, Inc.
Depending on the design, this may require a narrow V-coat to help exclude some ambient light to broadband AR coatings to allow the use of multiple wavelengths. Visible to NIR wavelengths may be used to match the specific needs of the application and environment (from 532 nm for bathymetric mapping to 1550 nm for eye-safe range finding).
Field of view also varies widely from one application to another. Even within the market for autonomous vehicles, some sensors tout a full 360° field of view, while others are designed to be used in-bumper for adaptive cruise control. AR coating specifications must take the design of the detection optics into consideration to ensure high transmission over the full range of angles to be measured. Additional blocking may also be desired to exclude ambient light for protection of internal optics or further improvement in signal to noise.
Many geometries, many substrates
With so many different applications of lidar, and so many different proprietary approaches to achieving the greatest accuracy, sensitivity, and range, there is no single design approach that dominates. Coated windows for lidar sensors may be flat, curved, or cylindrical – made of one monolithic piece or in sections. Coatings may instead be needed on internal lenses, standard or aspheric. Each design is unique. Even within a given lidar product line, a manufacturer may use different geometries for different applications, requiring a coating supplier that can work with a wide range of substrate geometries.
Substrate materials also vary widely between lidar sensor optics, from glass to plastics or polymers and pigmented materials. Single point diamond-turned (SPDT) optics are often used at the prototyping stage, and even into volume production for complex parts.
Uniformity is king
The one constant specification in all coated optics for lidar is the need for uniformity, both across the surface of a single coated optic, and in volume. This is of particular importance in the autonomous vehicle market, where lidar sensors are being used for navigation, proximity detection, and safety.
Tooling and fixtures factor into coating uniformity, but multi-axis coating systems are the true differentiator, ensuring uniform coating of all parts and all surfaces within a coating run for the most challenging geometries. This requires exquisite control over both the machinery and processes, including choice of the right rotation rate for each axis, careful synchronization between them, and a fine degree of control of the deposition rates within the chamber. Multi-axis coating allows even large optics to be coated with consistently high performance for each part within the coating run, and consistently across batches in volume production.
While the specifications for coatings used in lidar may not be spectrally complex, the wide variety of substrate materials, sizes, and geometries in use can make this seemingly minor aspect of lidar system design one that merits careful attention in order to maximize system performance.
Written by Pat Lulianello, Vice President & Alan Parsons, Sales Manager, AccuCoat Inc.; Cicely Rathmell, Mapleseed LLC