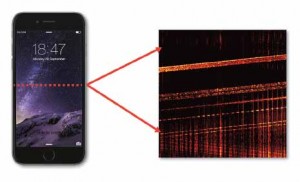
Optical coherence tomography (OCT), the most widely used optical medical imaging technology, has finally made its move into the non-destructive testing (NDT) and inspection arena, much as ultrasound did in the 1960’s. Valued for its ability to provide non-contact imaging of surface morphology and subsurface structure with micron-level resolution, the technique can provide quantitative analysis of structure, features, and defects for a wide range of materials. It is also rapid; 3D images may be captured in within few seconds, or a cross-section can be monitored at faster than video rates for real-time manufacturing or process control feedback. It is an interesting time for OCT in nondestructive testing; while it has been qualified as a viable candidate for several NDT applications, it remains to be seen in which markets it will become the technology of choice. We discuss a number of possible applications below.
OCT for next generation NDT
Based on low-coherence interferometry, OCT uses infrared light to probe the sample and rapidly create a 3D image from a series of cross-sections. It may be used with any dielectric material, including paints, glasses, foils, coatings, polymers, silicone, and rubber, as well as plastics, and for surface features of metals.
While ultrasonic inspection has been the manufacturing industry’s standard in subsurface imaging for simple cross-sections, the technique is limited in its speed and resolution, and requires the use of a coupling medium.
Confocal imaging offers submicron resolution, but is very expensive, and limited to depths of less than 1 mm. OCT bridges the cost gap, retaining ultrasound’s flexibility in taking the probe to the sample, while offering 2-10 µm resolution and eliminating the need for contact. Its ability to compete with other inspection and process monitoring techniques depends not only on these factors, but also on the unique needs of each industry.
Medical devices
Not surprisingly, the medical industry has been quick to adopt OCT for the analysis of high precision medical devices due to its ability to generate non-contact images of very small, thin, and delicate structures such as contact lenses and stents.
OCT can also provide information about pores, defects, and gaps in the production of critical membranes and seals. In the medical industry, resolution and accuracy are more important than speed or cost for quality assurance of critical parts.
Materials and textiles
In the materials and textile industries, quality control often requires destructive sampling in combination with manual or machine vision inspection. Woven fabrics pose a particular problem to image processing algorithms when the weave is complex or composed of multiple structures and colors, resulting in errors when dealing with checked and colored fabrics. By looking below the surface, OCT has shown promise in discriminating weave from weft threads to validate the weave pattern quickly and accurately. It is also being used to nondestructively identify defects in polymer composite materials, and to characterize the layers in sound-absorbing fibrous composites for the development of specialized acoustic materials.
Aviation and automotive
OCT is a natural match for the evaluation of critical coatings and paints in aviation and automotive. High resolution layer imaging enables analysis of thickness uniformity and defects that can impact quality and safety, as can be seen in this cross-section of paint layer thickness through a scratched region.
Cost-effective techniques like ultrasound imaging, magnetic and eddy current systems are used currently, but require direct contact and yield limited information. Terahertz (THz) imaging and optical confocal microscopy can provide much greater detail, but at prohibitive cost. OCT is emerging as a promising alternative to accurately measure the thickness of both base and clear coats, and for analyzing the distribution and characteristics of the metallic flakes that give many vehicles their sheen.
Display technology
The high axial resolution of OCT is ideal for imaging the multilayered structures used in displays and solar cells. The 3D information acquired can be used to evaluate flatness uniformity and identify subsurface defects affecting display quality that cannot be detected using visual inspection, doing so early enough in the manufacturing process to significantly improve quality assurance. OCT can also clearly image sublayers < 10 µm in thickness – superior to X-ray, computed tomography, and ultrasonic imaging techniques.
Laser material processing
OCT may be used for evaluation of shapes and dimensions of tools, molds, and final parts. Increasingly, it is being used for real-time detection and dynamic correction of defects in polymer-based additive 3D printing, as well as loose powder detection and assessment of integrity on a layer-by-layer basis.
Its ability to deliver rapid, high-resolution, non-contact imaging in hostile environments has led to the development of several commercial systems for real-time process feedback during laser machining and welding. It may be used in conjunction with machine vision to control laser power or speed, or as a secondary diagnostic for 100% inspection on critical parts.
Pharmaceutical coatings
Assessment of coating thickness and quality is of particular importance in pharmaceutical tablets, particularly for advanced coatings such as active coatings and sustained release formulations, where the drug release kinetics determines therapeutic efficacy. While near-infrared and Raman spectroscopy, nuclear magnetic resonance imaging, and THz imaging may be used, OCT appeals because it offers a direct thickness measurement at sub-micron resolution for coatings thicker than 10 μm that can be used to study both inter-tablet and intra-tablet coating variation.
OCT solving needs in NDT
As the technology matures, OCT is being evaluated to solve many unmet needs in nondestructive testing. That being said, each application has its own unique demands; some require lower-cost instrumentation, while others require the system to be operated in far less controlled environments. More sophisticated data processing techniques are being developed to translate images into actionable information. Facilitated by improved availability, performance, and breadth of robust component offerings to build these systems, the use of OCT as a dominant NDT technique is inevitable.
Written by Nishant Mohan, VP of OCT Division & Dave Freihofer, Global Business Development Manager, OCT Products, Wasatch Photonics