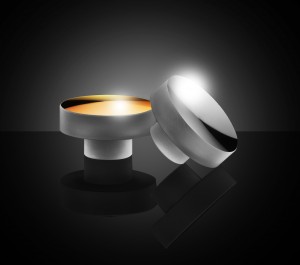
When flat mirrors are mounted by their edges stress is introduced to the mirror surface, warping the surface and reducing the quality of the reflected wavefront. Thankfully, special types of mirrors called stemmed mirrors decouple positional stability from mounting stress. These mirrors are mounted from a stem protruding from the back of the mirror, significantly reducing stress-induced surface warping (see Figure 1 above).
What’s Wrong with Conventional Mirrors?
Mounting-induced stress leads optical system integrators to not achieve the level of performance they were expecting; the surface flatness of the mirror when mounted is worse than what was specified for the mirror. This performance degradation is especially problematic when using tightly-toleranced laser mirrors for precision applications, as small variations in surface flatness have a more noticeable impact on performance. This results in surface distortion and reduced quality of the reflected wavefront, which is particularly impactful when using high-quality mirrors. This reflected wavefront error can decrease system throughput, introduce stray light and noise into the system, and result in larger focused spot sizes in laser focusing systems.
To investigate how typical mounting techniques impact mirror flatness, a mirror with a flatness of λ/10 was secured in a conventional kinematic mount using up to 12 in-oz of torque (“hand-tight”). The mirror's flatness changed to λ/5, degrading the specified flatness by a factor of two. This testing is described in more detail later.
Stemmed Mirrors: A Solution to the Mounting Stress Problem
Stemmed mirrors get their name from the characteristic stem protruding from the back of them, which is the only point of contact between the mirror and its mechanical mount (Figure 2). This significantly decreases the stress-induced deformation of the reflective surface. Simple kinematic mirror mounts can be used to mount stemmed mirrors with a high degree of positional stability while avoiding noticeable impacts on performance. In order to maintain a similar flatness when using a conventional flat mirror, a much more complex and expensive kinematic mounting solution would be required. The substrate (and stem) of stemmed mirrors are monolithic pieces of fused silica or other optical glass. While a stemmed mirror is slightly more expensive than a comparable flat mirror because of the included stem, the total cost of using a stemmed mirror is less than that of using a flat mirror with the same performance. This is because of the more complex mechanical mounting solutions needed to have the conventional mirror maintain a similar flatness and level of wavefront error.
Figure 2: A stemmed mirror in a simple kinematic mount can achieve the same performance as a conventional flat mirror in a more complex mount at a lower total cost.
Testing Stemmed Mirror Performance
To compare the performance of stemmed mirrors with traditional flat mirrors, a λ/10 stemmed mirror and a λ/10 conventional first surface mirror were both secured in identical kinematic mounts while the amount of torque used to lock them in place was controlled. The results showed that the stemmed mirror maintained a flatness of λ/10 through up to 12 in-oz of torque (which is widely considered to be “hand-tight”). On the other hand, the traditional mirror showed more performance degradation under the same torque with a final surface flatness of λ/5. Figure 2 also distinguishes between the contributions of different types of optical aberrations. This reveals that mounting stress introduces more astigmatism and power error than coma and spherical aberration.
Figure 3: Directly measuring the flatness of both stemmed and conventional flat mirrors as they were secured in identical mounts revealed that stemmed mirrors maintained surface flatness better than conventional mirrors by a factor of two.
Stemmed mirrors are a unique solution to the relationship between positional stability and mounting stress. Their monolithic substrate also provides excellent thermal stability. Stemmed mirrors can be coated in a variety of different reflective coatings depending on the application, whether a dielectric, highly-reflective laser coating or a more broadband metallic coating is needed. Simply thinking outside of the box and using a more unique substrate geometry led to the development of these novel mirrors that maintain the flatness of reflective surfaces even after they are securely mounted.
Written by Cory Boone, Technical Marketing Manager at Edmund Optics