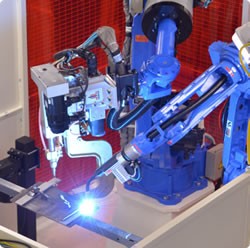
While the humble computer cable might not initially appear to be one of the most significant components of a computer system, for builders of machine vision systems, it is a critical link.
When developing a system based on the USB 3 Vision specification, for example, it is important to acknowledge that the type and length of cable used in the design of the system will impact the integrity of the video signal from the camera due to attenuation losses.
Because the technology underpinning the USB 3.0 Vision standard is based on the USB 3.0 specification, suppliers of vision components have been quick to realize that they can take advantage of some of the attributes of the USB 3.0 standard, including the "SuperSpeed" mode that enables video data to be bi-directionally transferred at speeds up to 625MB/sec.
Addressing USB 3.0 shortcomings
However, because it was originally developed as a bus used to interconnect peripheral devices to a PC, the USB 3.0 specification also has its shortcomings, which manufacturers building cables for the machine vision marketplace have been required to address.
The USB 3.0 specification, for example, defines a means by which data can be transmitted bi-directionally over shielded pair cabling. However, in many vision-based systems, the use of such cabling may be unsuitable. In a robotics application, for example, the cable linking the camera on the arm of a pick and place robot connected to a PC-based system may be continuously flexed as the robot arm moves to accomplish its tasks. In such a case, twisted pair cabling might not be suitable because it may degrade too rapidly and need to be regularly replaced.
Cable length
What is more, the USB 3.0 specification does not explicitly specify the maximum cable length that can be used to connect one USB compatible device with another. Guidelines issued by the USB Implementers Forum in April 2013, however, advised system builders using the USB 3.0 standard to restrict cable lengths to a maximum of three meters. However, where a USB 3.0 Vision based camera is deployed in an electrically noisy environment where EMI is generated from machinery, a computer connected to the camera may need to be located at some distance from it to eliminate any interference issues. And here, a three meter length of cable might prove inadequate.
Clearly then, the unique requirements of industrial vision systems have placed an onus of burden onto cable suppliers to not only create a more robust cabling solution, but also to address the issue of how to enable it to reliably function beyond a length of three meters.
To do just that, Art Didyk, VP Engineering R&D at Components Express, has developed an active computer to camera cabling system called BitMaxx. While the technology was originally created to address length and signal integrity concerns in the Camera Link market, today the company has repurposed the technology to build a cabling system that enables system integrators to build a USB 3.0 Vision complaint system that will operate at distances of 25m.
According to Ray Berst, the President of Components Express, the system itself comprises a USB 3.0 PCI based host controller card that moves data between system memory and devices on the USB 3.0. On the same host controller, a physical layer (PHY) transceiver handles low level USB protocol and signaling. The output from the PHY is used to drive data onto two sets of USB 3.0 Superspeed busses via transmitter differential drivers and differential receivers and equalizers.
In a traditional USB design, the output from the PHY would be used to drive data down a differential pair of cables. But in the BitMaxx design, the differential pairs of signals are routed onto one pair of coaxial cables with a high degree of resistance to noise.
With the BitMaxx design because the differential pairs of signals are routed onto one pair of coaxial cables with a high degree of noise resistance, system builders can implement a USB 3 Vision solution in robotics applications where the cable is continuously flexed during operation.
That alone, however, would not resolve the three meter distance limitation of the USB 3.0 standard. To do that, the coaxial output from the USB connector is connected to a dongle that contains circuitry to ensure the integrity of the signal over 25 meters.
“Specifically, the circuitry in the dongle eliminates the frequency-dependent attenuation of the signals over the long run of the cables,” says Berst. To do so, the dongle employs a pre-emphasis technique which boosts the signal's high-frequency components -- present each time a transition in the data occurs -- before the signals are transmitted down the cable. The dongle also contains equalization circuitry that overcomes the distortion of the received signal resulting from the high-frequency losses induced by the cable.
Ensuring a low bit error rate
During the development of the BitMaxx cabling solution, the amount of pre-emphasis and equalization applied to the signals was specifically programmed into the circuitry in the dongle to ensure that the bit error rate (BER) of data transferred down the 25 meter length cable would be as low as possible. To measure the BER of their 25 meter coaxial cable solution, Components Express worked with Stemmer Imaging to fund a project that saw engineers at Sensor to Image develop a PCI interface board that could analyze the video data by sending a stream of data down the cable and comparing the input to the output.
Ray Berst explains the rational behind the decision. “If you go to a USB 3 test lab and ask them to certify a cable that is longer than three meters, they won’t even test it. So we had to ensure that if we were going to develop a USB 3 cabling solution longer than three meters that it would perform adequately. Having developed the PCI interface board, we verified that the BitMaxx USB Vision 3.0 cabling solution could achieve a zero BER at a distance of 25 meters.”
Controller card included
The BitMaxx solution has one other important benefit too. The fact that the cabling system comes with its own USB 3.0 host vision controller card alleviates the system developer from mix and matching his own controller card and cabling. According to Mr. Berst, some engineers who chose to take that route in the past ran into difficulties with signal integrity issues on the cable due to the inadequate performance of the physical layer (PHY) transceiver that was used on the controller card they chose.
The Bitmaxx USB 3.0 PCI based host controller card moves data between system memory and devices on the USB 3.0. On the same host controller, a physical layer (PHY) transceiver is used to drive data onto two sets of USB 3.0 Superspeed busses.
System integrators considering using the active coaxial system should be aware, however, that because it meets the USB 3 Vision specification, it is not backward compatible to the older USB 2.0 specification. Nevertheless, because many cameras developed for machine vision applications now support USB 3.0, the issue of backward compatibility to the lower speed version of the bus may now be relatively unimportant.
Written by Dave Wilson, Senior Editor, Novus Light Technologies Today
Photo at top: In electrically noisy vision-based robotics applications, a computer may need to be located at some distance from a camera to eliminate any interference issues. Image courtesy Yaskawa Motoman Robotics.