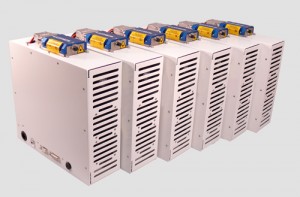
Diode lasers gain more and more importance as tools for applications in welding of plastic and synthetic material. We see joined plastic and synthetic material in our every day lives: from the battle in the morning of opening of your corn-flakes bag, plastic joints hold together your smartphone, shelter vendor parts and components wrapped in protective foil and hold microchips in smart cards in place. To name just a few applications.
Joints of plastic or synthetic material are usually either glued or welded. Welded joints are mostly chosen, when thermoplastic material shall be joined.
Conventionally, plastic welding is carried out by direct application of heat to both plastic parts which shall be joined. Several methods for this process have been developed in the past.
However, all these methods have disadvantages: they are either inflexible to change of design (e.g., heatable molds), require high-maintenance (e.g., heated filaments), or are energy inefficient (e.g., furnaces or hot-air blowers). Furthermore, all methods require a rather slow process speed and do not really allow to precisely position your joint.
Diode lasers for plastic welding
Using diode lasers for the welding and joining of plastic material enables you (i) to work remotely by attaching a focusing or scanner optic to your laser and hence (ii) to stay versatile concerning the shape of your joint due to the flexibility of your scanner optic and (iii) to be able to process complex geometries in 3D. Furthermore, you can (iv) achieve smaller and more precise joints due to the well-controlled positioning of your laser spot on the material, and (v) increase your energy efficiency due to the superb energy efficiency of the diode laser.
Choosing the right wavelength
Still, the use of diode lasers leaves you with one challenge: finding the right wavelength for your material combination. Since you are working remotely and not applying heat locally any more, at least one of your plastic partners to join has to absorb the energy of your laser in order to melt and join with the other material partner. Hence, you have to make sure, that the material is responsive to the wavelength you use. Typically, you are facing situations to join (i) transparent plastic on black substrate, (ii) colored plastic on colored plastic substrate, (iii) transparent plastic on transparent plastic substrate and (iv) white plastic on white plastic substrate
The ideal match in wavelength varies from 1064 nm to 1940 nm.
Generally, one can say that joining of transparent plastic to black substrate can be performed best with wavelengths from 808 nm to 980 nm and joining of colored, transparent and white plastics works better with wavelengths in the range of 1064 nm to 1940 nm. Of course, the ideal match in wavelength varies from application to application and should be tested before employing a diode laser.
Meanwhile, even new synthetic material is developed which responses specifically to one wavelength. Radiation of this plastic material with this specific wavelength triggers its functionality and starts a reaction in this material (e.g., laser induced foaming for additional sealing of joints).
Laser plastic welding for microwellplate sealing
Lumics GmbH, Berlin (Germany), demonstrates a biomedical application for plastic welding with diode lasers: together with LGC Genomics and Laser 2000 U.K. Lumics has developed a diode laser system for the sealing of microwellplates allowing to seal microwellplates of 96, 284 and 1536 wells size.
Microwellplates are a common tool in biochemical analytics and clinical diagnostics. They are flat plastic trays which host dozens or hundreds of tiny wells of sub-microliter volume in which biochemical reactions can take place. Multiple reactions on the microwellplate can then be screened in parallel on large scale.
To shelter the reaction wells from the outside, a thin transparent plastic foil is used to seal the top of the microwellplate after filling the wells with liquid reagents. This plastic foil is welded onto the microwellplate with a joint around every well in order to seal it not only to the outside, but also against the other wells on the plate.
Because the volume of reagents to perform clinical diagnostics has decreased tremendously in recent years, also the volume of the wells has decreased. Instead more and more wells are placed on one microwellplate. Due to the sensitivity of small amounts of liquid reagents to heat, conventional heating based sealing technology has come to an end here and a new, more precise technology which exposes the reagents to less heat is required. This is an ideal application example for the advantages of diode lasers for plastic welding which only locally heats up the plastic material.
Lumics solution uses a 980 nm diode laser with 50 W optical output power together with a laser driver and a controller which communicate with the customer interface of the LGC Fusion 3 welding device. The entire laser system is delivered in a custom designed casing, neatly fitting into the casing of the LGC Fusion 3 system.
Written by Michael Berndt, Product Manager Diode Laser Modules, Lumics GmbH